How to find Contact stress in Gear ?
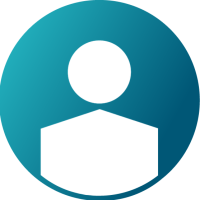
Hi ,
I have a Two sets of gear, here I want to perform an FEA Analysis to find out the contact stress in the gear tooth using Simlab?
I have gone through the rack and Pinion gear tutorial in Hypermesh. But in my case, there are Bevel and spur type gears.
Which type of analysis suitable to find the above outputs and which type of contact should I give?
I attached the image for your reference.
Thanks & Regards,
Sivaprakash V.
Answers
-
Hello @Sivaprakash_V ,
what kind of analysis do you need to run? Are the gears intended to deform, or is it a pure multibody analysis?
Best Regards,
Michael
0 -
Hi Michael,
I want to perform MBD Analysis. Is there any specific method for finding the contact stress in gears?
or Please let me know which type of analysis suitable for above gears to find the contact stresses.
Thankyou,
Sivaprakash0 -
Hello again @Sivaprakash_V ,
I'll let some of my colleagues complete but you need to use MotionSolve, and to apply cointact best practices:
Best Practices for Running 3D Contact Models in MotionSolve (altair.com)
You can even start your modeling directly in Inspire Motion, here's an example that was set using it:
Planetary Gearset Stress Analysis and Optimization in Inspire Motion — Altair Community
Best Regards,
Michael
0 -
Hi ,
Thanks for your reply.
I am currently learning Altair Inspire for performing analysis for our other application & gone through the above mentioned Planetary gear Simulation and Optimization.
Please correct me If I am wrong: If we use Inspire for the Gear analysis, First we Simulate the Actual working mechanism. If the simulation works fine then, Model the flex body and find the Stress & Strain.
Is the above statement correct or not?
In Inspire Can we find the Stress developed in the Contact Area when the gear is in motion ?
Thanks & Regards,
Sivaprakash V0 -
Hi ,
I tried to perform the gear analysis in Inspire. I am facing Issues in Rotating the gears and How to find the contact stress in Inspire.
Thanks & Regards,
Sivaprakash V.0