Planetary Gearset Stress Analysis and Optimization in Inspire Motion
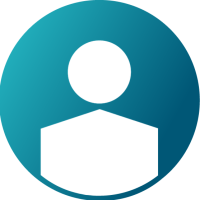

Overview
INTRODUCTION
Planetary gearboxes are useful for their compact design, high torque density, and efficiency. They distribute load across multiple gears, enhancing reliability and durability while reducing maintenance. Modular construction allows flexibility in gear ratios, accommodating specific operational needs. Planetary gearboxes can use high gear reductions to achieve precise control and high-power transmission. Overall, their efficiency, versatility, and reliability make them a valuable choice of gear reduction with applications in robotics, heavy machinery, and beyond.
Under high torque applications, it may be necessary to analyze a planetary gearset for stress and estimate fatigue life. Altair Inspire is an integrated simulation environment with tools for geometry creation, finite element analysis (FEA), multibody dynamics (MBD), optimization, and more. In this example, we will take imported planetary gearset geometry and perform an MBD analysis. Using loads developed from motion, we will perform FEA on the shaft to determine the stresses in the shaft. Then we will optimize the shaft to reduce the mass while keeping stresses below the fatigue limit of the material. Although a simple scenario, the same workflow can be adopted for complex systems. Inspire flattens the learning curve with semi-automated tools and a singular environment while leveraging high-performance CAE solvers.
Pre-Requisite
SOFTWARE REQUIREMENTS
Inspire (2024 or newer)
MODEL FILES
Planetary_Gearset.zip (See attachments)
Usage/Installation Instructions
Understanding the Workflow in Inspire
Multibody Dynamics Model Building
- CAD data can be imported into Inspire or built using a full suite of geometry tools.
- See Planetary_Geometry.x_b for the geometry.
- Materials are defined and assigned to each part.
- Mathematical relationships are built between parts with joints, rigid groups, or by grounding components.
- Motors are used to apply position, velocity, acceleration, or torque profiles to the input and output shafts.
- The input shaft uses a torque profile to represent the torque produced by a motor or engine.
- The output shaft uses a velocity profile to model the desired output velocity of the planetary gearset.
- Motion contacts are built between the gears with precise contact events enabled.
- If gear stresses are not of interest, couplers can be used to speed up computations.
- After running a motion analysis, the resulting motion can be animated.
- See Planetary_Baseline.stmod for the setup model.
Calculating Baseline Stresses
- By using the analyze part option, shaft stresses can be calculated at the timesteps with the highest loads.
- The shaft reaches 280 MPa. With an approximate fatigue limit of 430 MPa for the Steel 4340 shaft, the shaft can be optimized to reduce mass.
Optimizing the Input Shaft
- The gear teeth and splines must be partitioned or made into separate parts. This guarantees the optimization doesn’t remove any gear teeth or splines.
- The gear teeth, splines, and input shaft are added to a rigid group.
- The input shaft is changed to a design space.
- A motion analysis is run to develop loads for optimization.
- The input shaft is optimized with a goal of minimizing the mass and a stress target of 430 MPa or half the yield strength of the shaft.
- See Planetary_Optimized.stmod for the optimized planetary gearset model.
Calculating Optimized Part Stresses
- The optimized part is combined with the splines and gear teeth into one component.
- The geometry can be fitted with PolyNURBs to smooth the part.
- New geometry can be created with Inspire’s geometry tools to capture the optimized shape.
- By using the analyze part option, shaft stresses can be calculated at the timesteps with the highest loads.
- Stresses increase from 287 MPa to 424 MPa
- The mass decreases from 32.4 kg to 15.9 kg!
Post-Requisite
CONCLUSION
Planetary gearboxes are used across a wide range of industries for their efficient torque transmission, high gear reductions, and compact design. To ensure their durability and performance under various operating conditions, industries often employ techniques like multibody dynamics simulations. These simulations can be used to analyze the distribution of forces and stresses within the gears, ensuring that the gearbox can withstand operational demands without failure. In Inspire, an integrated simulation environment allows users to optimize components from loads developed during motion. The flattened learning curve makes it easy for designers or CAE specialists to analyze and improve systems from early design explorations to validation.
AUTHORS
John Dagg, Systems Engineering Intern
Christopher Fadanelli, Solutions Engineer – Systems Integration
Ananth Kamath Kota, Global Technical Manager – Systems Integration
Comments
-
hi team,
model is not working properly and maybe contacts are missing
after running the simulation i got below results
0 -
I am able to open both models and run successfully for the default duration and timesteps without any modifications.
- Did you make any changes to the model before running?
- Are you using Inspire 2024 or newer?
Hope this helps!
Adam Reid
0