How are the position at t=0 and gamma defined in Flux, and how is end winding impedance calculated?
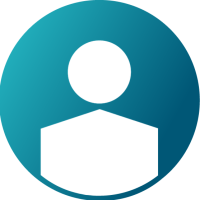
Hi
I am following the example "Flux - Twin Activate Coupling: IPM Motor Speed Control", focusing on Case 3, where the initial rotor position at t=0t = 0t=0 is set to 7.5°. I understand this is determined as the zero-crossing point of the phase-one voltage through back EMF analysis, as explained in the example "Brushless IPM Motor (Embedded Magnets)".
However, I am unclear about how the gamma value of 45° is chosen. Could you clarify the criteria or method for selecting the gamma value for my motor design?
When I use the macro "Find_Rotor_Angle_2D.PFM", it calculates the POS_INI value as approximately 52.5° for the example motor. For my motor, the back EMF analysis shows the zero-crossing point of phase-one voltage at 7°, but the macro calculates POS_INI around -106°.
How should I select the initial rotor position and gamma value for my motor to ensure proper setup in the controller for FOC implementation?
Secondly, I would like to know how the end winding inductance (0.159E-3 H) and coil conductor resistance (0.088 ohms) are calculated in the "Brushless IPM Motor (Embedded Magnets)" example.
I reviewed the "Induction Motor with Skew Tutorial" (page 90), which provides the formula for calculating end winding reactance, as shown in the attached figure. I have followed all the steps from this document and applied them to the Brushless IPM Motor (Embedded Magnets) example. However, I am unable to obtain the 0.159E-3 H value for the end winding inductance, and I believe I might be making a mistake in my calculations. I would appreciate your help in identifying where I might be going wrong.
The parameters I am using, as mentioned in the "Brushless IPM Motor (Embedded Magnets)" example (p. 20), are:
- Nss = 48
- p = 4
- Dext = 184 mm
- hss = 30 mm
- Number of coils per pole per phase = 2
The number of turns assigned to a conductor is 26, as mentioned in the example. I am also trying to understand how to calculate the following:
- Ntpp: Number of turns per slot per phase
- Nc: Number of coils in parallel per phase
Could you please guide me on how to correctly calculate these values?
Thanks,
Answers
-
Hello,
As you pointed out, the starting position for the IPM motor case corresponds to zero crossing point of the BackEMF considering the positive versus of it.
Gamma = 45° is the value that maximizes the torque, to find it you could set up a model where the Gamma angle will change or use FluxMotor: with the test “Characterization - Datasheet”, you can find the graph "T [Nm]-GAMMA". About the macro “Find_Rotor_Angle_2D.PFM” it is difficult to verify it without see the model and the inputs you set. Please keep in mind that the macro takes the first phase you indicated as reference; you can find more information about this macro in the document attached, available in the installation folder.
The “end winding inductance” is normally an input value for a 2D Flux model and it is added as circuit component on the phase branch to force the 2D model to consider this component that is mainly a 3D one and so to be more accurate. Since as you know the inductance value depends normally on the shape of the coils, this value is “characteristic of the motor” and depends also on the winding configuration; so it is normal you obtained different values. For example, as you can see in the document "Induction Motor with Skew Tutorial" (page 91), the formula to compute the end winding reactance considers certain geometrical approximations [P = formula (4) only for concentric winding with non-consequent pole, etc]. From a practical point of view, this means that we have to do some approximation to numerically compute end winding parameters. You can find some methods in literature or simply use FluxMotor that computes these parameters depending on the winding description you entered. You can find the “Resistances” and the “Inductances” tables in Motor Factory -> DESIGN -> STATOR -> WINDING -> Main results section (to the left of the screen). Please make sure you correctly set the topology (motor size and configuration) and the winding description.
Best regards,
Letizia
1