Design of Electric Motor Using Coupled Electromagnetic and Structural Analysis and Optimization
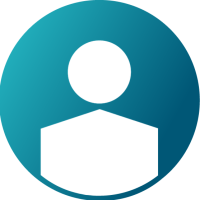

Today, vehicle architectures are changing continuously due to the need for increasing vehicle electrification. Electric motors have helped sustain this requirement. Traditional internal combustion engines are being replaced or coupled with traction motors or in-wheel motor systems in full-electric or hybrid-electric vehicles. With the use of electric motor in a vehicle, the number of parts can be reduced. This leads to reduced packaging size and complexity. Also, CO2 emissions are reduced, and overall efficiency is increased. But the task of designing an electric motor which is assembled in a vehicle could be quite complex. The design of an electric motor can affect the durability, and noise and vibration characteristic of the vehicle structure to which it is connected. The design of the vehicle structure to which the motor attaches should be able to sustain the magnetic torque generated by the motor. Electromagnetic forces generated on the stator of an electric motor affect the vibration characteristic of the motor casings and structure to which it connects. In an internal combustion powered vehicle, engines contribute the maximum to the noise in a vehicle. When internal combustion engine is replaced by an electric motor, then noise emitted in the vehicle is drastically reduced. But still the electric motor could be the main source of noise contribution.
This paper deals with coupling electromagnetics and structural mechanics in order to design electric motors and the vehicle structure to which it connects. An electromagnetic analysis is performed on the electric motor and the vibration loads from this analysis are used in the structural analysis. This process is used for optimization of magnetic torque and to reduce the noise radiated by the motor. CAD parametric optimization which couples electromagnetic analysis and structural analysis is performed using the global response surface method algorithm in this process.