Contact Settings plastic wheel to aluminium rail
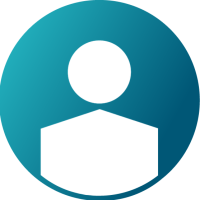
Hello,
I would like to model a contact between wheel (plastic) and rail (aluminum) in Simlab (Optistruct).
Modeled is point contact. By applying a vertical force on the wheel, a pressure ellipse will occur, so that at higher force several elements will come into contact.
Which contact settings should I use to model a realistic contact between the two contact partners?
Many thanks and best regards
Stephan
Answers
-
I'm not sure about the simlab setup, but on Optistruct side, the model should be run with NLPARM, possibly NLPARM(LGDISP) may be necessary
For contact itself, I would use S2S and make sure the search distance (SRCHDIS) set is sufficient that all potential contacting entities are captured, default settings should work fine (i.e. no adjust or clearance specific settings)
0 -
The parameters which Paul suggested can be found in SimLab in the Contact Definition:
NLPARM with Large Displacements can be activated under the Solver Settings:
CI don't know if CNTSTB may help in this case, but if needed, you have also the chance to activate it here.
I would recommend as well to take a look at this tutorial on our Learning Center:
This refers anyway to non linear analysis with pretension, a quite different load case, but it could clarify aspects related to friction-contacts.
Thank you
Alessio Librandi
1 -
Paul Sharp_21301 said:
I'm not sure about the simlab setup, but on Optistruct side, the model should be run with NLPARM, possibly NLPARM(LGDISP) may be necessary
For contact itself, I would use S2S and make sure the search distance (SRCHDIS) set is sufficient that all potential contacting entities are captured, default settings should work fine (i.e. no adjust or clearance specific settings)
Simple Example showing .fem set up attached, this is using standard n2s, s2s wasn't needed
0