Hailstone Impact on solar panel with HyperWorks
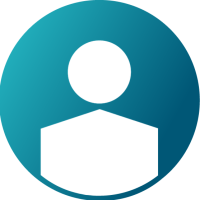
Mathis
Altair Employee

Overview
Outlook:
- HyperMesh meshing workflow using AI, Representations, BatchMesher & Connectors has been used to mesh quickly & efficiently the solar panel.
- Radioss allowed to simulate Hailstone impact on a solar panel. This results can be used to evaluate the structure and improve the design of the panel.
This article includes:
- 1 HyperMesh model with the solar panel, with the librairies to have the different representations
- 1 ready-to-use Altair Radioss model of balistic perforation
- Altair HyperMesh version is V2024.
- Altair Radioss version is V2024.1.
- The Unit System is in g, mm, ms
- Altair HyperWorks session file to allow fast analysis of the simulation
- A report with:
- Hypermesh process to mesh the solar panel using ShapeAI, BatchMesher & Connectors
- Brief overview of Radioss features for glass failure modeling and hailstone impact
- Analysis of simulation results.
Model Setup Process:
1. HyperMesh workflow: Match parts with ShapeAI
- Starting with the initial Inspire geometry, we can see that several parts are identical to each-other (they are just translated & rotated at different locations.
- The Match feature in HyperMesh (Assembly > Match), powered by ShapeAI encoding, is a great way to automatically detect parts that are matching each-other.
- Obviously, some parts are unique and won’t match other parts. In order not to forget them during the meshing process, check the box “Create part set for unmatched parts”.
- Once the match feature is used, all matched parts will be stored together in the same part assembly. Hence, when one part will be meshed, all matched parts will be meshed the same. This will help greatly to mesh parts faster and, in the future, to build for instance a different meshing thanks to part representations.

We will stay in the Part browser during the full meshing process
2. HyperMesh workflow: BatchMesher
- The BatchMesher is a great tool to get quickly and automatically a high-quality mesh. “The Crash 5mm” parameter file is especially good for Radioss crash models.
- We will just make a slight modification by right clicking on the part browser > Representations > Settings > Controls. Select Crash 5mm. In “Quality Correction”, we will uncheck the box “move across free edge”.
- This way, our mesh will respect perfectly the geometry at bounds.
- Then select all parts to be meshed in shell elements in the part browser. Right click > Representations > Create > Crash 5mm. For midsurface method, select “Offset”.
- The BatchMesher will run, and all parts will be meshed automatically according to the specified settings. Only one instance of matched parts will be sent to BatchMesher, the other instances will be synched, when loading the final mesh.
3. HyperMesh workflow: Connectors
- The Connectors allows to quickly define connections between parts like bolts or welding lines.
- The Fastener has been used to define the bolts
- The line has been used to define the welding lines
4. Radioss: Glass modeling
- The 2mm-thick glass is meshed with 2D shell elements. It is considered to be elastic until the failure is reached. The failure is modeled using the Alter failure model.
- This failure model uses a decrease of the (stress rate dependent) fracture stress in the direction of a propagating crack.
- The model was validated in the context of the head impact on windshields within a public founded project.
5. Radioss: HailStone modeling
- Altair delivers a variety of hailstone models, with different sizes, calibrated for aeronautic impacts.
- The model used in this study derivates from the 48mm hailstone.
- A 30m/s initial velocity is applied to the hailstone.
Result Vizualisation with HyperView:
- Radioss allows to visualize the global kinematic of the hailstone.
- Radioss allows to analyze the damage pattern due to the hailstone impact.
- Radioss allows to analyze the stress level on the solar panel components.
- The stress level is much lower than the yield stress. The structural parts are safe. Only the glass panel would need to be change.
Pre-Requisite
HyperMesh 2024 & Radioss 2024.1 are needed.
Usage/Installation Instructions
SOLAR_PANEL_HAIL.hm, Part_library.zip & Subsytem_library.zip can be used to retrieve the model & the different representations (CAD, mesh)
Unzip SOLAR_PANEL_HAIL_IMPACT.zip to retrieve the Radioss model.
1