Windshield Wiper Kinematics & Loads in Inspire Motion
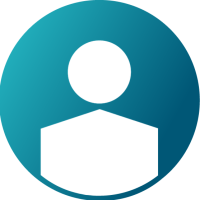

Overview
INTRODUCTION
Windshield wipers clear rain or snow from a vehicle’s windshield for thousands of cycles. Wipers must, under all environmental conditions, clear the appropriate area of the windshield to ensure the driver’s vision is unobscured, and have several other performance requirements such as cost, styling integration, NVH, power consumption, and of course, durability. Multi-body dynamics simulation software (termed MBD or MBS) such as Altair MotionSolve or MSC ADAMS can help with quantifying all these requirements using an intuitive 3D geometry-based approach. When a simple kinematics model is developed enough to capture the physics of the wiper-windshield contact, it then becomes possible to evaluate system and component durability. Analyzing the forces and stresses on the wipers with MBD software is one way to do that.
In this model, CAD geometry of a wiper mechanism is imported into Altair Inspire. Inspire is an integrated simulation environment that enables faster decision making by design engineers and CAE analysts. Foregoing the traditional “pre-process - solve - post-process” cycle prevalent in traditional CAE software, it can perform all 3 functions in a single environment. Inspire’s CAD integration, semi-automated MBD model build, and structural solver integration helps considerably flatten the learning curve. A design engineer or non-CAE expert may thus take direct advantage of Altair’s high-performance CAE solvers. The wiper blades are defined as flexbodies allowing flexibility to be correctly represented. Dynamic forces on the blades are examined throughout the wiper’s range of motion. Geometry of the mechanism in terms of hard-points for the linkages defines the kinematics.
Pre-Requisite
SOFTWARE REQUIREMENTS
Altair’s Inspire (2024 or newer)
MODEL FILES
Windshield_Wiper_Model.zip (See attachments)
Usage/Installation Instructions
MODEL SETUP
- Import Wiper_Geometry.x_b in Inspire.
- Ground the windshield and wiper frame.
- Create rigid groups for each wiper but exclude the blade.
- Create joints for the mechanism.
- Make the pins between the wiper supports and wiper arms rigid.
- Make locked translational joints between the wiper and blades.
- Create contacts between the wiper blades and windshield.
- Create a motor that drives the motor crank at 60 rpm and is supported by the wiper frame.
- Create torsion springs on the pins connecting the wiper arms to the supports.
- Change the stiffness to 50 N*mm/rad.
- Change the free angle to 25 degrees towards the windshield with the installed angle at 0 degrees.
- Enable the flexible for motion option for both wiper blades.
- Enable the computation of stress and strain.
- Wiper_Motion_Ready.stmod is an example of a setup model which is ready for simulation. By default, the wipers will not be flexible. In the property editor uncheck ignore flexibility under the Motion Flexible Body section.
SIMULATION STEPS
- Run the simulation for 2 seconds with an output rate of 300 Hz.
- Turn on active contact iteration and flex contact + under contacts in the run motion analysis dialog.
- Review the motion of the wipers after the analysis is finished.
- Contact forces can be plotted using the plot tool.
- The flexible body option can be used to review the stress and strain in the wiper blades.
Post-Requisite
RESULTS
The wipers sweep out an angle of roughly 75 degrees. Throughout the wiper’s motion, torsion springs push the wiper blades into the windshield causing the blades to slide across the windshield.
Wiper Motion
The windshield wipers experience cyclic forces as the wipers slide across the windshield. The forces can be plotted in Inspire to show the trend of the forces while the wipers move. Notably, as the wipers approach the vertical position they begin to chatter on the windshield. This is seen in the force-over-time plot where the force drops to zero as the wiper blades lift off the windshield. Then the force spikes as the wiper blades impact the windshield.
Wiper Reaction and Friction Forces
Wiper Normal Forces over Time
Adding Flexbodies allows the windshield wipers to deform and better conform to the shape of the windshield. Due to friction between the wipers and the windshield, the wipers bend as they move across the windshield. The original wiper shape is shown with a line of dots or tracers. The contour plot shows displacement with a maximum of 11 millimeters.
Displacement Contour Plot with Flexible Wipers
Maximum Displacement of 11 mm
The stresses on the windshield wipers can be reviewed with the flexible body tool in the review section of the banner. This provides a quick solution to view stresses without exporting loads for further analysis in a different software. The maximum stresses of approximately 5 MPa are around the attachment point between the wiper blades and wiper arm.
CONCLUSION
In the article, we demonstrated how Altair Inspire can be used to model a windshield wiper system. Although we choose to show a simple load-case, the engineering requirements are much more complex, taking into account high-speed operation, winter weather effects, debris impact, stall/overload, etc. Multibody models are a useful addition to the design and analysis process and augments detailed finite element analysis. In addition, for force and stress calculations, geometry changes could be tested to understand kinematics, namely the effects on the area swept out by the windshield wipers. All these scenarios can be modeled either directly or using surrogate methodologies within the same basic model that has been demonstrated here.
AUTHORS
John Dagg, Systems Engineering Intern
Christopher Fadanelli, Solution Engineer - Systems Integration
Ananth Kamath Kota, Global Technical Manager - Systems Integration