Ah, America’s Cup – getting under the skin!
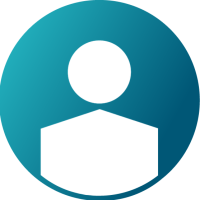

An interview with Julien Chaussée who takes a look at using Altair simulation tools to get under the skin of the new AC75 monohulls for America's Cup 36.
By day Julien is Senior Application Specialist for Altair Simulation solutions at Altair Engineering Canada, but out-of-hours shares a passion with many of his colleagues around the world for the symbiosis of cutting-edge engineering design and human intuition that together is the America’s Cup.
Q: What is the America’s Cup?
Without giving you a history lesson, it’s the oldest international sporting trophy that first came about when, in 1851, an American schooner won a race around the Isle of Wight, off the south coast of Great Britain. The prize was the “Royal Yacht Squadron. £100 Cup” that was renamed to “America’s Cup” after the winning vessel and remains the cup contested at the international competition in perpetuity.
Image: Oswald W. Brierly (published by Ackermann & Co. - National Maritime Museum, Greenwich)
Over the years the America’s Cup vessels have changed beyond all recognition. We’ve gone from monohulls to multihulls, catamarans and, for the latest challenge, back to a monohull which was initially a bit of a disappointment for me.
Q: What does the America’s Cup mean to you?
For me, the it is the ultimate blend of sport, engineering, and innovation. It’s not just about the fastest boat. It’s about the best compromise between raw performance, stability, maneuverability, harnessing the sailors’ ability, best crew work, etc. It’s a fantastic challenge! It’s always a very long cycle (about 4 years) between cups so you have to wait a long time to see some on the water action. And with Covid 19 it’s been extra-long! Until then it’s always lots of speculations who is the best and who is behind… But it’s finally happening, in Auckland. The Prada Cup Final is starting tomorrow, and I’ll be glued to my screen.
Q: Talk me through the new AC75 monohulls for America's Cup 36?
As I mentioned, I was very disappointed when I first heard newly crowned Emirates Team New Zealand (ETNZ) and their Challenger of Record, Luna Rossa Prada Pirelli wanted to go back to monohulls for the next cup. We had gone through a few really innovative cycles and the perspective of going back to the slow drag of the IACC I didn’t find enthralling to say the least. That was discounting Dan Bernasconi and his team of wizards. So, as it’s turned out: monohull yes... conventional, absolutely not!
The new AC75 boats are awesomely innovative and extreme (maybe too much for some?) although the concept is fairly simple: a 75ft monohull, flying above the water, balanced on a main hydrofoil and a T-foil Rudder while the windward foil is raised up to act as a counterweight and increase righting moment. The result, see below, has the potential of mighty speeds expected to top around 50+ knots.
The AC75 monohull concept
Q: How have the different teams responded to the AC75 challenge?
That’s one of the highlights from this latest cup. Each team has come up with very different solutions. So, from the development side, I’ve been fascinated following the 3 challenger teams (Luna Rossa Prada Pirelli, NYYC American Magic, and INEOS Team UK) and the defender (ETNZ) develop their boats. With the second generation of boats, it’s really interesting to see how they have converged in some areas but are still far apart in others. You can see some great illustrations of these in Francois Chevalier and Jacques Taglang’s blog.
From the first races at Christmas time to the early part of the Prada Cup, the relative performance of each team has changed drastically. Now, we are in the elimination rounds, we are going to quickly find out who was sandbagging and who just needed more time on the water to perfect their gear and procedures.
Q: What gave you the idea to look under the skin?
By the time the Prada Challenger Series started on January 15th, every expert was freely chipping in with their analysis. Most of the discussions focused on hydrofoil development, boat layout, and the efficiency of control systems or crew organization. Not surprising, as this is where most of the performance were to be gained with no time for re-designs. In all the coverage, I wasn’t seeing much about the structural aspects and what's hiding under the skin of these mighty beasts. Don’t get me wrong, I am very interested by the combination of aero- and hydro-performance. I love to get my head around how the different compromises play out. At the same time, I’m a composites structures guy by trade, so I've been very intrigued by that side too. Things like the new foil configuration, the speeds involved (American Magic topped at 53+kts in the races so far), and the new double-skin soft sails are sure to drive the loads through the roof so getting a strong, stiff but light design would be paramount to achieve the potential shown by the VPPs (Velocity Prediction Programs).
So, while I was waiting for the on-the-water-action to start, I started some exploration of my own and playing around with some concepts. I figured this is no different to a lot of the problems I face during my day job at Altair, so I should be able to apply the same techniques to the AC75s to get some ideas. I won’t claim to be a naval architect, but I’ve been lucky enough to be involved in three “Little Cup C-Class” campaigns, so I’ve picked up a thing or two along the way. And it also gave me the perfect excuse to test drive some of Altair’s latest tools and methodologies.
Q: Can you describe your various project steps?
I started with an end goal to use topology optimization at concept level. I am not looking for detailed structural design, laminate schedule or detailed stresses. Instead, I want to identify main load paths and understand how the different load inputs and components interact with each other. In practice this would then be used to define the internal structure and would be refined and optimized further at the next stages of development.
Not much has been published on architecture-level work, so I was starting pretty much from scratch. Although we've seen some use of topology and composite optimization on racing yachts in the past, most of them focused on component level design: ABStructures worked on a Bulkhead for the Volvo Ocean Race back in 2009 and more recently Alex Thompson Racing showed how they developed the canopy for the Hugo Boss Imoca 60, in collaboration with Altair Product Development (PD) team back in 2011. I also did some cross-beam composite optimization for the ETS C-Class catamaran back in 2015 as well as helping the students with the laminate development for the hydrofoils.
Creating a hull shape
My first step was coming up with a hull shape to use as reference. This was hugely helped by the latest release of Altair Inspire™, part of which is Studio, our new solution for industrial design and rapid design ideation. I was inspired (pun intended) by my colleagues' video on the rapid styling of a vehicle and decided to use the same technique to reproduce the hull of the first ETNZ boat, “Te Aihe”.
I used a lot of photos and information found online to shape the hull as closely as I could to the original. This project was my first real test of Studio and I admit I was really impressed because it was surprisingly easy to learn. PolyNURBs are borderline addictive! It took only a couple of hours or so to get a good shape, as you can see below.
Creating a hull shape with Altair Inspire Studio
Creating a model
For model setup, I turned to Altair Simulation solutions, in particular Altair HyperWorks which now brings all the applications under one common user experience. Along with its more intuitive interface, comes many innovative tools to make the simulation and optimization processes more efficient, easier, and faster. Among them is our “Design Space Management” (DSM) tool which helps to quickly generate a meshed design volume, specifically for the type of studies we are looking at here. It works from the initial shape and leverages a voxel mesher to keep the element count lower. It not only speeds up the meshing but also the analysis. When working at this level, getting an exact shape is not important since most of the material will be removed anyway. The tool has a simple selection of design/non-design volumes, which is easily updated.
For my project, I added to the hull shape some no-go volumes for the foil control system and the crew cockpit areas.
Exploring two concepts
With the DSM, we can rapidly produce different versions of the design space, moving the various volumes around and regenerating the mesh, which takes less than 5 minutes each time. I took advantage of that to explore 2 different configurations:
- A split port/starboard cockpit with the central section integral to the hull structure,
- A full width cockpit, i.e., assuming the center section seen on “Te Aihe” is a non-structural fairing.
Initial design volumes and no-go areas from Altair Inspire Studio
Meshed Configuration 1
Completing the rest of the yacht
Remembering that the key focus here is the hull architecture, the rest of the boat is simplified with beam models. Mast, foils arms, foil actuators, rudder and rigging are generated once and can be reattached to each new hull concept.
While the real hulls are made of carbon fiber composites with fairly tailored laminates, the material used here is isotropic having a stiffness representative of typical CFRP laminates. This might be counter-intuitive but since the main goal is to understand load paths and general structural arrangement, it gives more freedom to the optimization. In practice, the main laminate 0-axis is aligned with these load paths anyway.
Completed Configuration 1 (Left) and 2 (Right)
Loading conditions
My biggest sticking point was defining some loading conditions to optimize the structure around. When it comes to that, any sailboat can be complex because they are subjected to a mix of unsteady aero- and hydro-dynamic loads that are hard to measure or calculate. Then, a new racing class concept like the AC75 takes this to another level altogether.
For conceptual purposes, we can narrow this down a bit. Typical yachts are designed based on a mix of "global" loads which mostly result from rigging tension bending and twisting the hull, and "local" loads which drive local detailed design (e.g., main load inputs such as foils, mast, slamming loads, etc.). Larsson and Eliasson give a good overview of the process in their book “Principle of Yacht Design”. While it is important to consider all these loads, we are only interested in main loading directions and rough orders of magnitude. Precise loading or detailed local aspects such as slamming loads are not important. They mostly affect laminate design or stiffening at very local levels. Considering the AC75 will spend a lot of its time out of the water, supported by its foils, our job is a little simpler. The class rules give some hint at the target mass, distribution, and sail plan. This is enough to estimate righting moment and main load input points. To save time, I used Altair Compose® to do some quick sums and derive some balanced loading scenarios. A few assumptions are needed here:
- The loads are only estimated with the boat up on its foils.
- The main foil provides most of the lift and all of the side force.
- The rudder foil is used to balance the forward pitching moment.
- Overall L/D of the boat is estimated based on knowledge from other foiling boats. This is needed to estimate apparent wind angle.
- Foils L/D is also estimated based on available data. This is used to estimate the drag force on the main and rudder foils. The total drag is split between the two foils based on the relative amount of lift they generate.
- Two sail configurations are considered: small head sail + main and code-zero + main. This just moves the center of pressure and therefore the relative lift generated by each sail. Attachment points for each sail is also different so it adds a bit more details.
- Rigging pre-tension is estimated so all the rigging always stays in tension at any time. The windward backstay is omitted as it is generally loose.
Getting set-up for topology optimization
With loads and assumptions in place, all that was left to do was to bring all this together into an Altair OptiStruct™ model and prepare the topology optimization. I used a very conventional set-up here: minimizing compliance (maximize stiffness) with a constraint on the hull volume fraction. It took a couple of initial runs to refine the set-up, but the first results looked very promising straight away. Contrary to typical topology cases, I used a low volume fraction around 10% to 12% because these early runs show there was a lot of excess material with more conventional values. Each configuration has a hull volume fraction calculated so the final volume is the same and the comparison is fair.
Q: What did you learn from optimization of the different configurations?
Well, we probably should start with some pictures. I’m showing below a global overview of the results for both configurations in the form of a 60% density iso-surface. The first obvious conclusion is the bone-like organic structure does not really look like a sailboat hull, but that's what was expected.
Topology Results for Configurations 1 and 2 (60% density iso-surface plot)
If we look in more depth, there are some very interesting observations we can make. The first thing that struck me was the influence of the cockpit layout. It makes a lot of sense and might seem obvious to some. But it’s how deep that influence runs that I found interesting.
Let’s take a look at Configuration 1, with some of the details shown in the image below. Its split cockpit leads to a large proportion of the material concentrating longitudinally around the centerline, to form a kind of spine from which the rest of the structure hangs. The bow is built as a narrow I-beam with a truss web, almost all the way to the mast base while the back end is more of a box structure linking the midship structure to the transom area, where the rudder is attached. This makes sense because, with the loading condition I used, the bow is pretty much in pure bending, but the aft portion sees some torsion due to the asymmetrical loading from the backstay and mainsail traveler. The foils and mast sidestays are linked to the central backbone via secondary set of trusses forming a kind of bulkhead with a fore-aft brace.
Configuration 1 Detailed Results
Looking at Configuration 2, with its full width cockpit results in a different structure. The truss forms a kind of transverse box in the midship region, just aft of the foil attachments giving a stiff platform for the main loading points (sidestay attachments, foils pintles and mast step). As shown in the image, the main structural nodes serve to connect the rest of the structure, fore and aft. The narrow beam from the bow quickly transition to a triangular structure that connects to them. In the aft region, the material is arranged mostly on the outer perimeter. The deck is very minimalistic with only a few internal members stiffening key areas like around the rudder attachment.
Configuration 2 Detailed Results
A quick look at overall compliance/stiffness results shows Configuration 1 to be the stiffest, though only by about 6%. This is predominantly driven by the global longitudinal rigidity of the structure. A closer look at the foil and mast area shows Configuration 2 to be better in those regions. I don’t have all the details to hand, but instinctively I would expect this to be very important. Achieving a very rigid midship section would be critical to foils, sails and systems performance: stiff foil attachment means better control on angle of attack and more reactive systems. This region would also see a lot of dynamic loads with those big moving foil arms hanging outboard and moving constantly. So, if you add this to the integration with the cockpit and the rest of the aft section, I’d intuitively drive the design towards Configuration 2.
Q: So where do you go from here?
Having got this far, without adding a more complete load set, it’s difficult to assess the different designs much further. I am sure there are many other aspects to be considered. For this reason, it does not make sense to push the design to the next phase where we would be building the structure inside the hull skin and optimize the overall laminate.
Instead of diving deeper into detailed design, the launch of the second-generation AC75s gave me an opportunity to revisit the results and see how hull shape affects the structural concept. This is where the radical design of “Te Rehutai”, ETNZ’s second boat, piqued my curiosity because its extreme design showed some clear intent. Also, the narrow bow, expanding to max beam in the foil region and the cockpits pushed as far outboard as possible, leaving a kind of empty channel in the center, are particularly well-suited to my preferable second configuration.
Q: Was it easy to adapt the hull design?
Yes, very easy actually! It was a real test of turnaround time for my process, in terms of design changes. I took my “Te Aihe” design, and using pictures of “Te Rehutai”, it was really quick for me to reproduce the new shape with Inspire Studio. I kept the foil system, no-go volumes and replaced the cockpit to match “Te Rehutai”. All was left was remeshing the hull, integrating it in the previous model and updating the loads.
My approximation of “Te Rehutai” Hull Shape in Inspire Studio
Completed Configuration 3 using the “Te Rehutai” Shape
Only a few hours later, I was looking at some results that were beyond my expectation. These show a clear relationship between this topology and the previous one. If anything, this new design shows a direct evolution of those early designs, taking the best of both worlds. It leverages the narrow underside of the hull to build a backbone on which to grow the rest of the structure. But instead of concentrating all the material on that center plane, it takes advantage of the full width of the bow to build a stiff structure. It also retains the stiff arrangement aft of the foil mounting and around the mast. Finally, the better integration in the aft section shows some promising ideas.
Topology Optimization Results for Configuration 3
Q: What were the main take-aways from your dive into 2021 America’s Cup?
Although I can’t tell you for sure what's under the skin of the different AC75s, only the race results show how well their designers solved the immense structural challenges of this new class of racing yachts. The kind of conceptual level topology optimization I did is only one element of the whole process that needs a lot more information and detailed work to push these designs to full maturity and get some more answers.
I’m a way off setting sail in my own designed vessel but the exercise proved worthwhile and good fun. Although it takes a bit of squinting and imagination to see hull shapes and structure or even meaning through the organic bone-like structures we obtained, once you are past that, some real interesting aspects come to light.
One of the most positive parts of the experience for me was it gave me the opportunity to get to grips and apply a wider set of Altair tools than I tend to use in my day-to-day job. I am biased obviously, but I was impressed by how easy it was to put all these elements together and make it all work. What used to take days to set-up and run, now only takes hours so I could explore a bit further. Prior to this my experience of topology optimization at conceptual/architectural level was limited but this experience really brought home to me its true potential.
Comments
-
Nice job Julien!
0