What's new in Altair® FluxMotor® 2023.1 ?
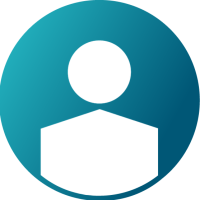

Altair FluxMotor 2023.1
Creating a motor model in FluxMotor and be ready to run multiphysics studies takes only a few clicks and a few minutes. You can also easily create a Flux model for 2D or 3D analysis, speeding up the simulation process. With this new version of FluxMotor, we are extending the possibilities by introducing new machine types. And new ones will also come in the close future.
POLYPHASE SYNCHRONOUS MACHINES
Polyphase machines are used in electrification mostly to ensure better reliability. You can now define synchronous permanent magnet machines, with inner or outer rotors, having more than 3 phases: 5 to 15 (only odd numbers).
The characteristics of the winding architecture can be defined in detailed in the winding area of FluxMotor. Once defined, the machine can be exported to Flux 2D or Flux Skew.
Defining a 7-phase machine in FluxMotor
WOUND FIELD MACHINES
Quite well known in the field of power generation, wound field synchronous machines can also be used for traction. This technology offers good efficiencies and various control scheme options and does not rely on costly rare-earth permanent magnets. You can now define such machines in FluxMotor with a wide library of rotor part templates that will let you consider various types of pole shapes, dampers and field windings. A dedicated interface will help you define the rotor winding architecture, defining the characteristics of the coils, the insulation and the end-winding dimensions.
A wound field synchronous machine easily defined
When the model is ready, it can be exported right away to Flux to perform working point or back-emf analysis.
AUTOMATED CALIBRATION OF THERMAL NETWORKS
When performing thermal computations at pre-design stage, FluxMotor is using 1D thermal networks that are automatically extracted from the motor topology definition. To increase the accuracy of the model, you have the possibility to use X-Factors that will adjust thermal resistances or cooling method inputs. It helps to be consistent with measurement results for instance and will have an impact on the resulting temperatures one gets in steady state or transient simulations. This calibration process can be fully automated with the new version of FluxMotor. You target the temperatures to be obtained and the X-Factors will be determined automatically to reach this goal. You can easily calibrate a model from measurement and then use it to extensively test your machine in various conditions.
Automated calibration of thermal simulation for fast and accurate temperature predictions
3D MODEL GENERATION FOR INDUCTION MACHINES
Have you ever tried to generate a 3D finite element model of an induction machine ? It can get quite time consuming ! Within FluxMotor, you can now do it in a very few steps for induction machines with squirrel cages. You have the option to consider the full machine or take advantage of periodicities and symmetries to reduce the model size. The lengths of the rotor and the stator can be different. Geometry, mesh, winding, circuit are automatically generated. Your model is ready to be solved.
Getting a 3D model ready to be solved in a few minutes
Want to know more about the new version? Get all the details in the Release Notes [Link].
If you want to learn also about Flux and its new features, follow this [Link]
Enjoy the new version !
Fabrice Marion - Senior Program Manager - FluxMotor®
Vincent Leconte - Senior Director - Electrification Solutions