What's new in Altair® FluxMotor® 2022.3?
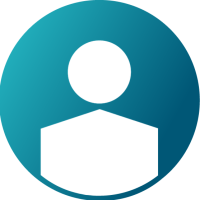

Altair® FluxMotor® 2022.3
When you need to efficiently characterize the performance of an electric machine, FluxMotor is the tool of choice ! Always more modeling capabilities are brought in this version, with the best compromise between accuracy and computation speed, in an easy to use interface. The connection with other tools has also been improved, making sure FluxMotor is well integrated into the global electric motor design and optimization workflow.
FAST AND PRECISE CHARACTERIZATION OF INDUCTION MACHINES WITH SQUIRREL CAGE
For system engineers who need accurate curves to characterize the behavior of the induction machine with squirrel cage in function of a set of Line-Line voltage (U) and a set of power supply frequency (f) a new test “Characterization – Model – Motor – Scalar” is now available in FluxMotor.
Hence, data are ready to be used in system simulation software like, Activate or PSIM. Indeed, from results obtained in this test, a scalar drive and control can be applied.
Those computations are based on the identification and the solving of a non-linear model considering the cross saturation and the eddy current effects. All the main electromagnetic quantities are computed and displayed as curves in function of speed for a given power supply frequency and a set of Line-Line voltages.
The results of this test give an overview of the electromagnetic behavior of the machine considering its topology. For a set of Line-Line voltages (U) and a set of power supply frequencies (f), the general parameters of the machine like, mechanical torque, currents, power factor and power balance are computed and displayed as curves.
Characterization – Model – Motor – Scalar - Illustration
GETTING INDUCTION MACHINE EFFICIENCY MAPS IN A VERY EFFICIENT WAY
It is now possible to characterize the behavior of induction machine with squirrel cage in the "Torque-Speed" area and get efficiency maps considering scalar control command. It is available with input parameters like “the maximum Line-Line voltage, the rated power supply frequency, the maximum line current and the maximum speed”.
In the results, the performance of the machine at the base point (base speed point) and at the maximum speed (maximum speed point), set by the user are presented.
A set of curves (like Torque-Speed curve) and maps are computed and displayed.
Performance mapping – Sine wave – Motor - Efficiency map - Illustration
The computations are based on the identification and the solving of a non-linear model which is built with maps. It considers the cross saturation and the eddy current effects in the squirrel cage.
The identification of the model (1st harmonic) is operated with the steady state AC application of Flux® (Finite Elements).
All this allows getting a good compromise between accuracy of results and computation time.
EXPLORE HAIRPIN WINDING TECHNOLOGY WITH FLUXMOTOR
In a search for high power density, hairpin windings are now often used. If they bring technological advantages, they are also not so easy to design and to model. In a dedicated interface to define them in a very easy way, FluxMotor is bringing now full capabilities in standard mode to test the performance they bring. In addition, all the provided tests are available for optimization studies in HyperStudy® through the corresponding connectors.
Should you need to explore further the performance of the machine, you can also export your models to Flux in 2D.
This technology can be applied to all the machines available in FluxMotor: Synchronous Machine with Permanent Magnets, Reluctance Synchronous Machine, Induction Machine with Squirrel cage.
WINDING design area – Area dedicated to Hairpin winding topology – In standard mode
Optimisation of machines with hairpin winding topology is possible – Motor Factory – EXPORT area
IMPROVING THE MAPS FOR SYNCHRONOUS MACHINES AND THE CONNECTION TO SYSTEM SIMULATION
The test “Characterization - Model - Motor - Maps” gives 2D maps in Jd-Jq plane for characterizing the 3-Phase synchronous machines with permanent magnets.
These maps allow predicting the behavior of the electrical rotating machine at system level.
With the new version, the operating quadrants can be selected : “2nd and 3rd “, “1st and 2nd “and “all”.
This allows defining the quadrants in the Jd-Jq plane, where the test will be carried out.
Characterization / Model / Maps for SMPM - New user’s inputs to select the operating quadrants
D-Axis flux linkage, D-Axis dynamic inductance, Iron losses, … in the Jd-Jq area
Note: Export / System LUT (Altair® Activate® or Altair® PSIM®) has been updated for exporting data based on 1, 2 or 4 quadrants
Thanks to that, engineers will find a system integrator and / or control-command tool adapted to their needs and able to provide accurate maps ready to be used in system simulation software like Activate or PSIM.
Performance of the machine in steady state can be deduced from the results obtained in this test in association with the drive and control mode to be considered.
Export / System LUT (Activate or PSIM) has been updated for exporting data based on 1, 2 or 4 quadrants
NEW EXPORT FROM FLUXMOTOR TO FLUX E-MACHINE TOOLBOX
One great ability of FluxMotor is to allow users to compute and display efficiency maps in a very reduced time. To get this solving speed possible, some assumptions are made, especially in the way losses are computed. To get the most precise evaluation of efficiency maps, the FeMT (Flux e-Machine Toolbox) has been developed in Flux. It is based on full transient simulations.
There is now a seamless connection between the two tools, to allow you to go from one modeling level to the other easily. A new button in FluxMotor will launch directly FeMT and will create automatically the transient model it needs to run.
Export a project from FluxMotor to Flux e-Machine Toolbox (FeMT) – Motor Factory – EXPORT area
AND ALSO:
DIRECT CONNECTION TO HYPERSTUDY: FULLY READY TO OPTIMIZE
With the new version, the user gets an even more seamless connection with HyperStudy. Optimization is now just a click away from FluxMotor.
Indeed, in Motor Factory / Export environment / HyperStudy, once the test is selected and configured, the test data chosen, and the export information set, a button (1) allows to directly and automatically launch HyperStudy, build and load the connector to perform the optimization.
A new button (1) allows to directly and automatically launch HyperStudy,
with the connector ready to be used for optimization
The studies can be initialized and run immediately in HyperStudy. The input variables as well as the output responses that have been selected in FluxMotor are automatically identified and uploaded.
HyperStudy is opened with the input variables and the output responses ready to be defined
TWISTED WIRES INSIDE THE CONDUCTOR OF COILS
The modelling of the twisted wires is considered in FluxMotor as well as in Flux 2D (or Skew) while exporting the project.
In case of twisted wires, the wires change position between the forward (IN) and return side (OUT) of the coil.
The model periodicity is automatically considered with the right conditions (cyclic or anti-cyclic).
In each conductor, the color gradient illustrates the change in position.
in this example, the periodicity is based on a half of the geometry with cyclic conditions
SOLID CONDUCTORS WITH SKEWED MACHINE TOPOLOGIES
The wires can now be considered as solid conductors when the stator or the rotor are skewed. The solid conductors will be taken into account while exporting projects from FluxMotor to Flux Skew as well as in the back end of Motor Factory for computing the machine performance.
Exporting a machine with a skewed stator in Flux Skew is possible with represented coil conductors
(One phase or All phases) and the resulting model in Flux Skew
There’s a lot in this version ! Get all the details in the Release Notes.
If you want to know also about Flux and its new features, follow this Link
Enjoy the new version !
Fabrice Marion - Senior Program Manager FluxMotor®
Vincent Leconte - Senior Director of Global Business Development, Electromechanical Solutions