I need help with my model. Is it legit?
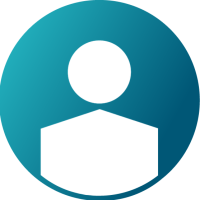
Hi i need to run cfd and extract Cl Cd in diffrerent AoA. I'll attack all files (mesh, log).
This is my volume (chord is 1.56m and span is 0.143m) (aoa 0, vel 108.611 m/s)
Ill now attach the mesh condition specified
+
Now everithing seems fine till i plot Cp/chord. Crazy plts happens also when i plot lift and drag i have some points befor the "zero" of the x axis ??
and this are the data from acusolve cmd prompt
The mesh run took a couple of minutes but the solution run took 2.27 hours... and i got an intel i9 and 64gb of ram.
can u take a look guys and give me some advices, idk if im doing something wrong.
I'm looking foward to learn from u.
thank u all
Answers
-
For some reason the images are not visible to me now - but I think I saw them earlier.
One of the plots was tracking lift/drag as the simulation proceeds through the calculation - so only the last value (at convergence) is of interest for a steady-state simulation. The path to get there is not that relevant.
This also coincides with the output from the command prompt - minimum is through the run - the last is of interest.
You'll need more/finer mesh near the body, and maybe along the body itself - better resolved surface, particularly at the leading edge. You'll also want to capture the wake region with better mesh - and shape that wake still to capture the flow as the angle of attack changes.
Here's a validation case:
0 -
acupro_21778 said:
For some reason the images are not visible to me now - but I think I saw them earlier.
One of the plots was tracking lift/drag as the simulation proceeds through the calculation - so only the last value (at convergence) is of interest for a steady-state simulation. The path to get there is not that relevant.
This also coincides with the output from the command prompt - minimum is through the run - the last is of interest.
You'll need more/finer mesh near the body, and maybe along the body itself - better resolved surface, particularly at the leading edge. You'll also want to capture the wake region with better mesh - and shape that wake still to capture the flow as the angle of attack changes.
Here's a validation case:
thanks for answering.
Near the body i added a refinerment zone of 0.02, the boundary layer is 0.0002 and a volume mesh is 0.1.
should i refine it even more?? can u tell me the values i should put instead of the one that i said to u?
0 -
Francesco C said:
thanks for answering.
Near the body i added a refinerment zone of 0.02, the boundary layer is 0.0002 and a volume mesh is 0.1.
should i refine it even more?? can u tell me the values i should put instead of the one that i said to u?
That's part of the sensitivity studies to run - see how different mesh settings affect the results. It's difficult/impossible to just give you a number and say that will be correct.
Maybe add another refinement zone a little larger than the first, with a mesh size larger than the smaller refinement zone - say 0.035 or similar - to keep the mesh smaller nearer the body before it grows larger farther away.
You may also need smaller surface mesh than what you currently have - again, difficult to predict. It also sounds like you may be limited with computation power so you'll be somewhat limited in mesh node/element count. It's always a tradeoff - accuracy vs runtime.
https://help.altair.com/hwcfdsolvers/acusolve/topics/acusolve/training_manual/mesh_sensitivity_r.htm
0 -
acupro_21778 said:
That's part of the sensitivity studies to run - see how different mesh settings affect the results. It's difficult/impossible to just give you a number and say that will be correct.
Maybe add another refinement zone a little larger than the first, with a mesh size larger than the smaller refinement zone - say 0.035 or similar - to keep the mesh smaller nearer the body before it grows larger farther away.
You may also need smaller surface mesh than what you currently have - again, difficult to predict. It also sounds like you may be limited with computation power so you'll be somewhat limited in mesh node/element count. It's always a tradeoff - accuracy vs runtime.
https://help.altair.com/hwcfdsolvers/acusolve/topics/acusolve/training_manual/mesh_sensitivity_r.htm
I understand what ur saying and ur totally right,
But i have a i9-14000K liquid cooled, 64gb of ram, im running the simulation at 31 cores out of 32, i changed the domain to a "C" shape "inlet", i meshed even finer around the body, in the wake zone and also in the whole volume.
The mesh run took something like 20 min.
I started the acusolve run and is running but in 1 hour and 30 min didnt even finish the first time step, still in "begin time step", is it possible?
If u need i can attach the .hwcfd model and the mesh log / run log.
i really need to figure out what im doing wrong
Thanks for helping it means so much
0 -
Francesco C said:
I understand what ur saying and ur totally right,
But i have a i9-14000K liquid cooled, 64gb of ram, im running the simulation at 31 cores out of 32, i changed the domain to a "C" shape "inlet", i meshed even finer around the body, in the wake zone and also in the whole volume.
The mesh run took something like 20 min.
I started the acusolve run and is running but in 1 hour and 30 min didnt even finish the first time step, still in "begin time step", is it possible?
If u need i can attach the .hwcfd model and the mesh log / run log.
i really need to figure out what im doing wrong
Thanks for helping it means so much
CFD simulations can take a long time - especially as mesh count increases with better mesh resolution.
You could attach the updated/new simulation .Log file with the larger mesh if you like. The RAM is going to limit the model size at some point. You should also disable hyperthreading - use only physical cores. Not sure on the P-Cores versus E-Cores. You could try core count (-np) for only the number of P-Cores, then see if there's a difference when adding the number of E-Cores in addition. But best never to go beyond physical core count. (Seems like it's maybe i9-14900K rather than i9-14000K - and that has 8 P-Cores and 16 E-Cores - so best never to specify more than 24 - and maybe only 8.)
You can try building 2-D meshes (in case you're not) where you use the extrusion meshing to get just one volume element in the 'thickness' direction. This typically gives you ability for higher mesh resolution - but lower mesh count versus having multiple elements in the 'thickness' direction. Good tutorial for this approach:
https://help.altair.com/hwcfdsolvers/acusolve/topics/tutorials/acu/acu_2100_intro_cfd_r.htm0