FluxMotor HyperStudy connector for thermal behaviour in duty cycle
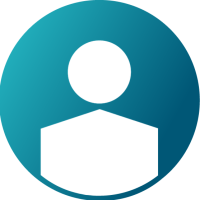
Hello,
I want to perform a DOE of a specific motor design inside HyperStudy. My goal is to get general information of the machine characteristics inside the base and maximum speed point and then perform a transient thermal study for every motor design (e.g. 120 seconds at a specific working point of each machine).
Inside FluxMotor, in the tab "Test --> Performance Mapping --> Since wave" I can define a duty cycle for the machine and see the transient thermal behaviour. My hope was to get the same functionality inside the HyperStudy connector.
My plan was to create a HyperStudy connector from the performance mapping--> sine wave. Unfortunately, the connector is able to extract general machine characteristics but not the thermal transient behaviour.
How can I implement this inside a HyperStudy project? It seems that FluxMotor is able to do so but once I create the HyperStudy connector, I am loosing this functionality.
Best Answer
-
Hello Melih,
HyperStudy is a powerful tool and allows the user to connect several models and solve them in cascade; so you can consider 2 or more models made by different tools in the same HyperStudy project.
In your case you can export the Flux thermal model from FluxMotor and consider it in the HyperStudy project as second model; the losses computed in the FM model can be the thermal loads of the Flux model to obtain at the end of the single run, what you are looking for. If you need help in implementing this workflow you can open a ticket in the support section and we will help you.
Just to clarify, FluxMotor considers an equivalent thermal network in background that unfortunately is not available for the export today, but it will be available in a future version. Flux, as you know, is a FEM tool and needs "user" convection coefficients.
It is also possible to replace the thermal Flux model in HyperStudy with an equivalent thermal circuit of the motor, built in "Twin Activate," "PSIM," or other Altair and non-Altair tools. Also Excel file, Python scripts and Compose scripts can be used.
I hope this will help you.
Best regards,
Letizia
1
Answers
-
Dear Melih Ayyildiz,
Your described workflow is indeed very interesting. I have a suggestion that may not exactly be what you are looking for (as it doesn't involve transient thermal analysis inside Flux) but can provide multiple benefits and another scope in your study.
My suggestion involves integrating your FluxMotor-designed motor into PSIM and then employing HyperStudy to explore motor and even inverter losses across various operational points. This approach allows you to investigate the impact of different factors, such as modulation techniques for PWM, the choice between MOSFETs and IGBTs, and the influence of dead time on motor losses.
For more details on this workflow, please refer to the following link:
Insights into Motor Drive Design: Analyzing Trends and Long-Term Costs with PSIM and HyperStudy
PSIM with FluxMotor & HyperStudy can offer you a cost-effective express lane to insights derived from a multitude of simulations. To be more specific, the Flux and FluxMotor models inside PSIM utilize a simplified model derived from Flux or FluxMotor, thus preserving the FEA tool accuracy. They also enable simulation of custom motor designs. More details about the Flux/FluxMotor models inside PSIM can be found here: Analysis and design of complex motor drive systems.
PSIM allows for a more realistic representation of the motor's input currents, which include harmonics affecting both thermal behavior as well as NVH. The calculated currents can then act as input to Flux in order to perform a more realistic thermal analysis there as a secondary step.
Hope this helps!
Best regards,
Nikos Dimitrakopoulos
0 -
Hello Melih,
HyperStudy is a powerful tool and allows the user to connect several models and solve them in cascade; so you can consider 2 or more models made by different tools in the same HyperStudy project.
In your case you can export the Flux thermal model from FluxMotor and consider it in the HyperStudy project as second model; the losses computed in the FM model can be the thermal loads of the Flux model to obtain at the end of the single run, what you are looking for. If you need help in implementing this workflow you can open a ticket in the support section and we will help you.
Just to clarify, FluxMotor considers an equivalent thermal network in background that unfortunately is not available for the export today, but it will be available in a future version. Flux, as you know, is a FEM tool and needs "user" convection coefficients.
It is also possible to replace the thermal Flux model in HyperStudy with an equivalent thermal circuit of the motor, built in "Twin Activate," "PSIM," or other Altair and non-Altair tools. Also Excel file, Python scripts and Compose scripts can be used.
I hope this will help you.
Best regards,
Letizia
1