Hi Pablo. Do you see any clues in the out file? If you don't, maybe sharing it might help, somebody might use those clues to understand if there is something ill-defined.
Problem with Second Phase of composite optimization (Sizing)
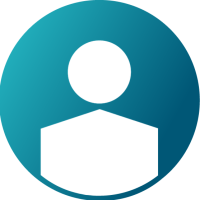
Good afternoon, I’d like to share my problem: Starting with a laminate [0/45/-45/90/90/45/-45/0] with 1.5 mm thickness per layer, I carried out a free-size optimization to reduce the mass while imposing a Tsai-Hill constraint with an upper bound of 0.1. This configuration for the free-size phase has been the most effective among the ones I’ve tried, as the solver reduces the laminate’s mass from 0.83 kg to 0.04 kg while meeting the constraint. Thus, the total thickness of the laminate in the free-size phase ends up being 10.8 mm.
However, when I proceed to the SIZE (PARAMETER) optimization phase, and in the DCOMP card, I introduce a minimum laminate thickness constraint of 10 mm (so that it doesn’t reduce excessively and continues to meet the Tsai-Hill constraint), and reintroduce the mass of the structure as the objective function to minimize it further, I also slightly modify the Tsai-Hill constraint to ensure it’s still met after further mass reduction.
My issue arises when I run the optimization: No matter how many simulations I run, it never satisfies the minimum laminate thickness constraint I set in the DCOMP card, always leaving it at 1.9 mm thickness. This results in ridiculously high Tsai-Hill values. I’ve also tried using compliance as the objective function, but I still get the same strange results. What could I do?
Best Regards, Pablo
Answers
-
Hi Pablo. Do you see any clues in the out file? If you don't, maybe sharing it might help, somebody might use those clues to understand if there is something ill-defined.
0 -
Hello, my problem seems to be fixed, i run again the sizing optimization, and the results look good; but i have another question: When i run free-size optimization, i obviously play it with the SMEAR option in the STACK card, as we are in a concept design level; but when passing to the second fase (sizing optimization of each ply bundle created), i saw that, for a simple load case (canteliver beam with small thickness), the failure response is snaller if i delete the SMEAR option than if i maintain it, so, i think that this is because os the fact that, althought matrix B is set to 0 with the SMEAR option, matrix D is set to [A]*T^2/12, so it reduces the flexural stiffness of the symetric laminate. In order to play the sizing optimization, i do not know if go on with the SMEAR option selected, or delete it and take the sequency into account in the sizing optimization phase.
0 -
I think that Altair typically recommends staying with it, but I also believe that Optistruct will not error out if you don't.
0 -
But, doing size (parameter) optimization wouldn't be more accurate starting from realistic results, meaning with the SMEAR option deleted from STACK card?
0 -
The good thing about optimization is that the process is as good as the improvement in your design is. You can try both approaches and stay with the best design.
If you remove the smear, a disadvantage is that you are effectively fixing/freezing the stacking sequence and you still don't know if that sequence / order is the best one. Smear gets you an "averaged" behaviour.
0 -
I saw that, no matter if i select smear or not; optistruct offers me the same result after the size optimization (2nd Phase), in terms of tsai-hill failure criteria. I think, that is is because, the optimal design, is the same always for the sizing phase, no matter the model you start with.
1