Topology optimization of a column
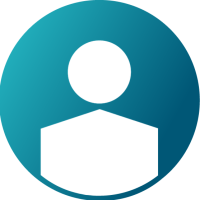

Hi,
I want to do a topology optimization of a column considering the buckling problem. The column has a square cross section (90 x 90 mm) and has 3500 mm in height. Therefor I used shell elements with t=90 because I found out solids do not work for buckling issues in topology optimization. First I ran a simple linear buckling analysis which worked out pretty well. But when it comes to the optimization I dont know how to handle the buckling problem correctly. I used a non-zero base thickness for the shell elements and minimal compliance for the objective. When I set 'buckle' as a dconstraint with a lower boundary of 1.0, the constrains get badly violated. As another dconstrain I used a volumefracion of 0.9.
I dont know if I used the dconstraints correctly ... so does the response 'buckle' stand for the buckling load? I also read about 'LAMA' somewhere and found it in the 'constraint screen' but actually I am not sure how to handle this one properly.
Thanks for your responses in advance!
Regards
Nico
Answers
-
Hi Nico,
Can you share the model file to under stand the problem setup using the file transfer link in my signature below?
0 -
Hi,
Thank you for sharing the file.
You may have to change the formulation for optimization. You can have buckling constraint and minimize volume as objective.
My observations when I ran just analysis is the buckling load factor is of the order 9E+5, this means the applied load is way to less than the critical load and eventually removes all materials violating your volume fraction constraint.
Even with above suggested formultation I think most of the material will be removed. You can give it a try and make a decision on design.
0 -
Hi Prakash,
thanks for your advice. You were right: if I minimize volume as objective most of the material will be removed ... but I found out that maximizing the minimal buckle mode with volumefraction as a constraint works pretty well.
Now my next question: can the thickness of a shell structure actually be seen as its density in toplology optimization? So if I want to have a rho_min of 0,45, I can set my base thickness to t_0 = 0,45 * t (with t being the thickness of the shell)?
0