Rover Design & Analysis using Altair Inspire
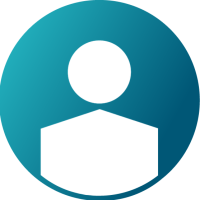

Preface
Engineering students designing rovers for competition face challenges in designing lightweight, efficient, and effective vehicles, whether part of NASA’s Lunabotics, the University Rover Challenge, the International Rover Design Challenge, or another challenge. One of the most significant problems student often face is minimizing the mass of the vehicle while maintaining strength and stiffness. The cost of sending a rover to the moon can be as expensive as $1.2 million per kilogram as is the case with the Peregrine Lander. Due to the astronomical expense of sending equipment to another planet, rovers must be as lightweight and compact as possible, demanding teams spend time optimizing geometry to maximize performance and minimize mass. Simulation, particularly topology optimization, is a key tool for engineering students to achieve their mass requirements.
Altair Inspire is one great option for analysis and optimization. Inspire makes setup easy with a simple user interface and automated tools which expedite the model building process, all while leveraging industry standard solvers to handle complex models. One advantage of using Inspire is the integration of different solvers. Engineers can build a multibody dynamics (MBD) model with Inspire Motion, use the loads developed from motion to perform finite element analysis (FEA), and then analyze manufacturability for 3D printing, casting, or forming, all in one environment. Inspire also makes topology optimization easy and approachable while utilizing the powerful OptiStruct solver to generate strong, stiff, and lightweight parts.
Introduction
Every year, the Michigan Tech Astro-Huskies compete in NASA’s Lunabotics challenge. Lunabotics challenges team to design, manufacture, and test a lunar rover while following the systems engineering process. This year, teams must construct berms from lunar regolith, which would be useful for protecting lunar infrastructure from lunar launches and landings. Teams compete in a simulated lunar environment with rocks and craters. Teams are scored on the volume of berms constructed, rover mass, energy usage, dust tolerance, data usage, and autonomy.
Previous rovers the Astro-Huskies designed utilized four-wheel drive and a skid-steer steering system. This year, the mobility team took on the challenge of developing a four-wheel drive, independent four-wheel steer system. Independent steering will allow the rover to perform new maneuvers such as strafing with crab drive, turning about instant centers with Ackermann steering, and tight turn radius maneuvers with zero-turn radius capabilities. The ability to perform these new maneuvers will benefit the team in the rock and crater-filled test arenas, while lowering torque and energy requirements from the original skid-steer system. However, this new system comes at the cost of increased mass. To hit NASA’s mass requirements, the team used topology optimization and analysis to lightweight most components on the rover making an independent steering system possible.
Mobility Design Workflow
The mobility team roughly followed the workflow below which used SolidWorks and Inspire to design the mobility system. The team iterated through the steps many times to refine the design for the best results.
- Design steering system hardpoints in a SolidWorks sketch.
- Select an actuator based on required force, speed, stroke length, and packaging space.
- Refine hardpoints based on chosen actuator to maximize mechanical advantage and meet steering range of motion requirements.
- Design rough geometry of key components in SolidWorks to connect hardpoints & test steering articulations to ensure clearance.
- Perform topology optimization in Inspire to generate optimal geometry which connects key hardpoints.
- Define a design space
- Define load cases
- Select optimization constraints
- Analyze optimized geometry performance using FEA in Inspire.
- Refine optimization until performance meets requirements.
- Use the optimized geometry to inspire the component design in SolidWorks, balancing the lightweight optimized geometry and manufacturability for a selected manufacturing method.
- Perform finite element analysis in Inspire to validate that part performance meets requirements for strength, stiffness, and mass.
Optimization Results
Early Rear Bracket Design Exploration (Left) | Final Rear Bracket Design (Right)
Manufactured Rear Brackets (195 g)
Front Upper Bracket Design Exploration (Left) | Final Front Upper Bracket Design (Right)
Manufactured Front Upper Brackets (226 g)
Front Lower Bracket Design Exploration (Left) | Final Front Lower Bracket Design (Right)
Manufactured Front Lower Brackets (235 g)
Front Steering Knuckle Design Exploration (Left) | Final Front Steering Knuckle Design (Right)
Early Wheel Design Exploration (Left) | Final Wheel Design (Right)
Manufactured Wheel
Validation with FEA
Once individual part designs were complete, the team performed FEA on the mobility system under a near comprehensive list of load cases. These encompass loads applied due to the vehicle weight, drive torques, steering forces, and additional loading scenarios. The loads assume stall of the drive motors and steering linear actuators. However, loads could be collected from a multibody dynamics (MBD) model in conjunction with EDEM.
Below, a select few results are shown for Von Mises stress and deflection.
Von Mises Stress Scaled to Yield for Combined Vehicle Weight, Steering Forces, and Drive Torque Load Case
Front Steering Knuckle Deflection Under Vehicle Weight
Von Mises Stress Scaled to Yield for Combined Vehicle Weight, Steering Forces, and Drive Torque Load Case
Rear Steering Knuckle Deflection Under Vehicle Weight
Rover Assembly
The team is in the process of finishing manufacturing and assembly for the rover. The rover will soon be wired and the testing phase will begin.
Author
John Dagg, Systems Engineering Intern & Astro-Huskies Mobility Lead