a) for A, yes, the solver will use the homogenized modulus to calculate macro scale displacements, then propagate these into the ply level. You could check the homogenized values in HM, by usng the Composite browser, and its tools. Homogenized constants will be lower than the E1 in the fiber direction, so, more flexible results are expected compared to a pure 0 laminate. Just run your model, with all 0 degree, and you should get similar results to your analytical.
Among these tools, you will find and option to calculate the equivalent engineering constants of a given laminate.
b) in terms of stiffness it shouldn't affect much, but for strain/stress, of course, mesh convergence and local refinement should be considered to get accurate results
c) are you running a NL analysis in OptiStruct? If yes, there should be only NLGEOM and/or contacts involved in this case.
Displacements in a laminated traction beam
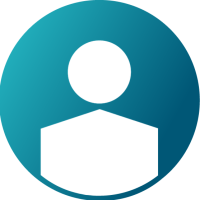
Good morning,
I am simulating a rectangular beam with a length of 500 mm and a width of 100 mm, subjected to a tensile force of 500 N in the longitudinal direction. The beam is fixed at the opposite end, with a boundary condition of zero displacement applied to all grids on that side.
The model is a composite laminate composed of 8 plies, each 1 mm thick, with the following symmetric layup sequence: 0/-45/45/90/90/45/-45/0. My issue is that when I calculate the displacement in the X direction analytically, the values are smaller than the results obtained from my FEM model.
I suspect this discrepancy could be due to one of the following reasons:
a) I am using the elastic modulus E1 in the fiber direction for the analytical calculation. Could it be that OptiStruct uses an equivalent elastic modulus, which is a weighted average of the laminate's plies?
b) My mesh consists of CQUAD elements with a side length of 20 mm. However, since this is a simple loading case, I don't believe the large mesh size significantly affects the accuracy of the results. Am I wrong about this?
c) It could be due to some parameter related to the nonlinear analysis, but I am not exactly sure how or why.
Answers
-
a) for A, yes, the solver will use the homogenized modulus to calculate macro scale displacements, then propagate these into the ply level. You could check the homogenized values in HM, by usng the Composite browser, and its tools. Homogenized constants will be lower than the E1 in the fiber direction, so, more flexible results are expected compared to a pure 0 laminate. Just run your model, with all 0 degree, and you should get similar results to your analytical.
Among these tools, you will find and option to calculate the equivalent engineering constants of a given laminate.
b) in terms of stiffness it shouldn't affect much, but for strain/stress, of course, mesh convergence and local refinement should be considered to get accurate results
c) are you running a NL analysis in OptiStruct? If yes, there should be only NLGEOM and/or contacts involved in this case.
0 -
Thank you, it has ben useful for me to looking out in the model and calculate the Equivalent constants for the laminate, but, unforunately, still not obtain the analytical value of the maximum displacement under bending load.
0 -
bending of a composite is completety affected by the layup/stacking sequence, and it is not possible to capture that with a single property/ply. FE models use Classical Laminate Theory and you should be able to perform the same manually.
0 -
I have the SMEAR option in my STACK card, Maybe is that the reason of false results in my model?
0 -
Which abd matrix are you using in your analytical results? Does this matrix match with what Hypermesh calculates? (not talking about displacements, i am going one step back.
0