Shaker Post Simulation for a 6x4 Truck in MotionSolve
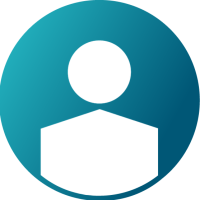

INTRODUCTION
The shaker post test is used in the research phase to test vehicle suspensions and evaluate vehicle durability. Actuators at each wheel simulate road forces and displacements. Tests can be performed by inputting simple displacement wave forms to each actuator or by reproducing the displacements experienced by vehicles on the road. The shaker post test is valuable to suspension engineers for damper tuning, fatigue life analysis, and general suspension characterization. Shaker posts are also used in production to detect squeak and rattle in assembled vehicles.
While shaker post tests can be valuable during the design phase, they require a fully manufactured and assembled suspension system. Engineers can use a computer model of shaker post test earlier in the design process than physical testing in order to characterize the suspension. This reduces the time and cost of performing shaker post tests, leaving physical testing for final validation.
In this example, we will build a shaker post test of a 6x4 truck in Altair MotionSolve. Each post will use a displacement signal to emulate real-world road conditions. By implementing a flexible body truck chassis, stresses on the chassis can be viewed and used for fatigue analysis.
Pre-Requisite:
SOFTWARE REQUIREMENTS
MotionView (2024.1 or newer)
MotionSolve (2024.1 or newer)
MODEL FILES
Truck_6_Post_Test_Archive.zip (See attachments)
Usage/Installation Instructions:
MODEL SETUP & SIMULATION STEPS- Open a new MotionView session.
- Change the wizard library to Heavy Truck under Libraries.
- Under the Vehicle Tools tab, click assembly to create a vehicle. Use the default settings unless specified otherwise.
Page 1: Full truck with driver
Page 2: Default options
Page 3: Front suspension – Solid axle suspension
Rear suspension – Rear dual solid axle suspension
Pages 4-5: Default options
Page 6: Front shocks – Front shock absorber (with inline jts)
Page 7: Default options
Page 8: Two-axle driveline
Page 9: Rear driveshaft 3-piece
Pages 10-11: Default options
Page 12: Click finish - Change the truck chassis body to flex.
- Choose Chassis_Flexible.h3d for the H3D file. The flexible chassis was created using FlexPrep, a MotionView tool which connects to OptiStruct.
- Add an Npost event in the Entity Browser.
- Change the coupling type to tire.
- Under Post Settings, select a data directory that contains the road profile csv file.
- Select the Road_Profile.csv and choose the appropriate channel for each post.
- Change the end time to 40 seconds under Simulation Settings.
- Run the simulation and review the results.
Post-Requisite:
RESULTS
Shaker Post Test Animation
In HyperView, a contour plot of von Mises stress can be created to review the stresses on the truck chassis. The stresses reach approximately 56 MPa which can be used for fatigue analysis.
Frame Von Mises Stress
Vehicle Body Accelerations
CONCLUSIONShaker post tests allow engineers to tune dampers, analyze fatigue life, and characterize a suspension. Implementing simulated tests in software, such as MotionSolve, lets users run informative tests, like a shaker post test, before manufacturing a full suspension system. This can reduce the cost and time invested in physical shaker tests. Integrated post-processing tools make the collection and presentation of results quicker and easier. In addition to shaker post tests, MotionSolve includes kinematics and compliance testing, static load analysis, and tire envelope analysis. These powerful tools allow engineers to evaluate and improve suspension design.
AUTHORSJohn Dagg, Systems Engineering Intern
Christopher Fadanelli, Solution Engineer – Systems Integration
Ananth Kamath Kota, Global Technical Manager – Systems Integration