Type7 Contact
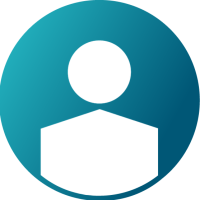
Hello Guys,
i want to know actually in my model, Tied contact is working with Error showing 0 % but when i am creating Type7 Contact starts showing me error 30 % which is very high. Can you please tell where can be the problem in the model as i am new to crash modeling so cannot find out that.
Its a side Impact Pendulum problem where hammer is crashing down the Tank with Input energy of 0.5 kj. Tank is connected with frame and fixation.
Answers
-
Hi Ashish,
The energy error percentage is the parameter that checks the energy conservation during each numerical cycle and it is computed by RADIOSS is a percentage. If the energy error is negative it means that some energy has been dissipated. If the error is positive there is an energy creation. If the positive energy error is high, the source of this energy has to be identified. Incompatible kinematic conditions can lead to such a situation. Normally, the energy error must be negative and decreasing (except for the first cycle ). Normally, the error should be less than 15% at the end of computation but if the model undergoes high plastic deformation the energy error can increase. It seems like when you use Type 7 interface sliding occurs between parts which contribute for this energy error.
If you can share the model we can review the same.
0 -
Hi George,
Thanks for your fast reply !
Actually i am sorry that i cant share model because it is confidential. But i can explain the problem.
Fuel Tank is quite complex geometry with lot of curves i have meshed it with quad shell mesh. Tria is around 5 % only and Pipes connected the tank is with quad mesh.
One Problem is solved that the error % is not very high because i have inputed wrong input velocity to the impactor now its showing around 2 % which is quite good but still my model didnt run for the Target time Step it stopped due 'Mass Scaling ' and it shows message that Run time Killed Mass Error Limit Reached. In the end it increases heavily Error like 99% and simulation Stopped.
What can be the problem here ? where should i check in the model ?
0 -
Its Showing so many Incompatible Kinematic Conditions ? where can be the problem in this case ?
0 -
Hi Ashish,
Please check the interfaces for any penetrations. Clear if any are there.
If the target time step provided is high it could result in run termination with Mass Error Limit Reached message. Penetrations can lead to such situations.
As nodal constraints are based on kinematic conditions applied on nodal DOF, therefore it is not allowed to apply two nodal constraints to the same set of nodes. RADIOSS Starter will show the incompatible kinematic confition warning each time two nodal constraints are applied to the same set of nodes. This is an undesired warning in a model. It is of very important to take all warnings about incompatible kinematic conditions into account. True incompatible kinematic conditions can generate energy and local instability.
Please recheck the BC's and loads in the model. Always try running the model checker before exporting the model, which will display the modelling errors.
Please share the engine out (_0001.out) file.
0 -
This is the Out File.
0 -
Can be this problem of Screws Material ? becasue i need to use it hard Rubber Mat and i have chosen Elast_Mat1 but i should choose another material card bec its elasto plastic mat ... MAT_36 can be used ??
it can be the Kinematic Problem ?
0 -
-
-
Hi Ashish,
Use the recommended contact parameters are as below for interface Type 7:
Istf=4
Igap=2
Fscale_Gap=0.8
INACTI=6
Gap_min=
Fric = 0.1
Iform=2.
Assign these parameters and please check for penetrations in this interface.The below post shows clearing interface penetrations in HyperMesh.
0 -
-
Hi Ashish,
As recommended before please clear the penetrations in the interface and try running the model. This error is happening due to the penetrations in the interface.
If you can share the model through the secure dropbox we can review.
0 -
Hi Ashish,
You can fix the penetrations either automatically or manually. I'm attaching a tutorial which shows fixing penetration in HyperMesh.
Please follow those steps to fix the same.
0