To find the Torque required to loosen the interference fit
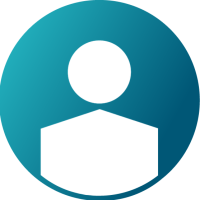
We have done analysis on interference fit with the objective to find out the slip or relative motion between parts under interference fit when subjected to torque . But could not conclude from the results analysed.
would like to interpret the results at what torque the fit will fail or slip?
First step interference is cleared and the first step is given as an input to the second step torque loading using CNTNLSUB
Radial Interference value - 0.014 mm ;Length of interference = 120 mm ; Torque applied = 6000 Nm ; Friction coefficient = 0.2
Answers
-
Hi,
I would suggest you to change a little bit your 2nd loadcase.
Instead of applying a torque directly, i would rather apply a imposed rotation to your shaft (using an RBE2), and request SPCFORCE.
SPCFORCE will give you the Torque needed to rotate your shaft. Request also rotation of the RBE2 node.
Then when you plot this result in HyperGraph (Torque x Rotation), you will see after some point the friction will be not enough.
You would probably see a drop in the torque after some radians of rotation.
Don't forget to enable Large Displacement, and Finete/Continuous Sliding for your contacts, depending on how much your shaft will rotate.
Applying an Imposed Displacement/Rotation is much more stable for implicit analysis, than applying the force/torque directly.
1