Getting high stress in contact interface
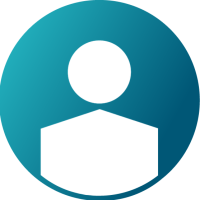
i have simulated a snap fit - By transient nonlinear approach in optistruct, kindly see the attached image. The red colour component engaging with yellow cylinder by rotation at 2.61 rad/s rate .
Rotation about y - axis . only the red colour component was moving and all other components were fixed
im getting higher stress at interface at the time of engaging (approx.at 0.18 s). Simulation run for 0.3 sec( for 45 degree rotation )
Can u tell me why this happening ???
Answers
-
Hi,
Contacts are subjected to some noise depending on your mesh, contact discretization, and so on.
But what exactly do you feel is not consistent? I couldn't see exactly what you think it is too high.
0 -
Hi Adriano ,
The allowable stress of that material in contact is only 70Mpa , But in simulation i get more than 100 Mpa at one or two nodes in interfaces
0 -
Vidyaprakash G S said:
Hi Adriano ,
The allowable stress of that material in contact is only 70Mpa , But in simulation i get more than 100 Mpa at one or two nodes in interfaces
Are you aware that contacts might be very dependent on the mesh discretization that you use, and also the contact parameters applied, right?
The stress value being higher than the allowable could mean:
- design is not good
- model is not good enough
- both are not good
Please check if the mesh discretization is capturing well the contacts, by requesting CONTF. Some times you can have a 'pin effect', where all the force is transfered from one part to the other thorugh a single point, thus the local stresses are high.
And remember, FEA is an approximation. You have to understand what points can give you useful information, and what points can also give you a poor information due to modeling techniques, or discretization.
0