Adaptive mesh technique for the simulation of a forming metal sheet component.
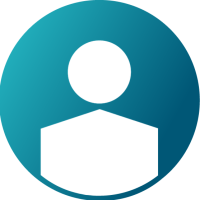
The provided model showcases the forming of a metal sheet component. Adaptive meshing technique is used to improve the results of the simulation, while minimizing the number of elements and, hence, the cost of simulation. Altair® HyperForm® has been used in order to set this model up. The model overview is displayed in Figure 1.
Figure 1: Model overview.
To set up the adaptive mesh technique a specific Card (/ADMESH/GLOBAL) and a Set (/ADMESH/SET) must be defined.
The /ADMESH/GLOBAL Card definition is shown in Figure 2.
Figure 2: /ADMESH/GLOBAL Card definition.
The next selections have been made for this Card:
- LevelMax = 2 Maximum level of element subdivision. Each element can be divided in 4 and then each of the 4 subelements again to 4.
- Iadmrule = 1 Ensures that the level difference between 2 neighboring elements is not exceeding 1.
- Idt = 0 The cycle time step is calculated based on the current refined mesh. This option can be activated to use the initial mesh for the time step calculation in order to avoid low time steps and large simulation times.
The /ADMESH/SET definition is shown in Figure 3.
Figure 3: /ADMESH/SET definition.
The ADMESH/SET is used to define which elements will be remeshed and the criteria applied to remeshing decision.
- Sheet component is selected in Entities
- Angle-criterion = 5 Neighboring elements with angle greater than 5 degrees will subdivided.
- Inivel = 0 Initial level of refinement. In this case the initial mesh will be remained equal to the one created in HyperMesh without subdivision.
- Thkerr = <blank> Thickness error criterion (here not applied). This value defines the limit of thickness error, above of which the elements will divided.
The model simulation is displayed in Figure 4.
The remeshing process of the sheet metal is displayed in Figure 5.
Figure 5: Sheet metal remeshing process.