Vehicle Rear Wheel Steering Control in MotionSolve
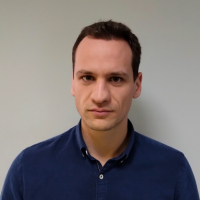

Overview
Brake in Turn Maneuver
Red – Passive System | Blue – Active Rear Wheel Steer
PREFACE
Physical vehicle testing, especially involving automated driver assist systems (ADAS), is expensive and resource intensive. Vehicle modeling and simulation provide an efficient augmentation which can be implemented earlier in the design cycle to understand a vehicle’s dynamics. Multibody dynamics software combined with 1D physics-based modeling, such as Altair MotionSolve and Twin Activate respectively, allows users to set up and analyze a wide range of dynamic systems, including vehicles. Altair’s MotionSolve allows the simulation of a wide selection of vehicle events to analyze vehicle performance parameters. Twin Activate’s block diagram modeling approach allows intuitive representation of control and actuation elements. Results can be used to refine vehicle performance and improve occupant comfort. The model was created by Spyridon Mallios as part of his master’s thesis on vehicle dynamics and rear wheel steering control.
INTRODUCTION
Vehicles can become unstable during emergency maneuvers. Rear wheel steering (RWS) can improve vehicle stability which reduces the risk to occupants and other road users. In this simulation, the performance of a vehicle with rear wheel steering is compared to a vehicle without rear wheel steering during an emergency single lane change maneuver.
The vehicle model without rear wheel steer is created in MotionSolve and simulated to get a baseline for vehicle performance during the lane change maneuver. Meanwhile, the rear wheel steering vehicle model utilizes co-simulation with MotionSolve, Twin Activate, and Compose to accurately capture the vehicle dynamics and control the rear wheel steering system outputs.
Understanding the Model Definition in Compose
To optimize the performance of a rear wheel steer vehicle, a closed-loop controller is necessary. The controller requires real time information about vehicle states, including sideslip angle and yaw rate. Compose, an environment for math calculations, data visualization, and programming, is used to generate a map of vehicle states which can be passed to a controller that adjusts the steering angle.
The co-simulation begins with a reduced order model (ROM) of the vehicle run on Compose as an iterative process. The model uses planar dynamics for handling evaluation and the Magic Formula equations for tire modeling. The model takes in vehicle mass properties and suspension design factors. By varying vehicle speed, steering angle, and sideslip angle independently, the iterative process captures all driving scenarios in a map with yaw rate as the output. The map captures the stable vehicle conditions which serve as a reference for the rear wheel steer controller.
Understanding the Model Definition in MotionView
After the generation of the reference map, work on the MotionView model begins. MotionView is Altair’s multibody dynamics pre-processor. The model consists of a full vehicle model with suspension and steering and is typically developed on top of a default model which is chosen from a library of available suspension, steering, powertrain, brake system types. Altair Driver, which is a set of controllers, “drives” the vehicle to follow the set path at the desired vehicle velocity profile. At each time step, the MotionView model provides information about vehicle velocity and steering angle to the Twin Activate model. Then the Twin Activate controller computes the required steering inputs for each rear wheel, which are independently controlled. This process repeats for each timestep.
Understanding the Model Definition in Twin Activate
Twin Activate contains the rear wheel steering controller and manages the overall simulation. Each time step, the model receives information about the vehicle’s states. The controller compares the vehicle’s actual response with the reference map of stable vehicle conditions. A PD controller is used to compute steer response for each rear wheel while avoiding oscillations. The model’s estimation is improved by computing transient slip angles and cornering stiffness of the axles with the ROM and MF tire solver.
Pre-Requisite
SOFTWARE REQUIREMENTS
Altair MotionView (2023 or newer)
Altair MotionSolve (2023 or newer)
MODEL FILES
RWS_Models.zip (See Attachments)
Usage/Installation Instructions
BASELINE VEHICLE ANALYSIS
MODEL SETUP
- Open the Sedan_Single_Lane_wo_RWS.mdl file in MotionView.
- Select the SingleLaneChange event in the Model Browser.
- Update the single lane change event parameters in the Entity Editor to the desired values. For this example, we will use the default values.
SIMULATION STEPS
The simulation simulates a Sedan driving in a straight line and then performing a rapid lane change. Without rear wheel steering the back end of the vehicle overshoots the desired path.
- Run the analysis. Ensure the single lane change event is selected and select the Results folder for the output directory.
- Open the h3d file in HyperView to analyze the results and view the vehicle’s motion.
REAR STEERING CONTROL ANALYSIS
MODEL SETUP
- Setup the MotionView model.
- Open the Sedan_Single_Lane_with_RWS.mdl file in MotionView.
- Select AltairDriverFile 1 in the Model Browser.
- In the Entity Editor, update the Altair Driver File to the adf file created during the baseline analysis in the Results folder. This will replicate the same path the baseline vehicle followed. The file should have a name similar to Sedan_Single_Lane_wo_ RWS_Run_event_2.adf.
- Prepare the MotionView model for co-simulation with Activate.
- Run the MotionView model with the Results folder selected as the output directory.
- Open the h3d file in HyperView to analyze the results and view the vehicle’s motion.
- Export the solver deck to the Results folder by following File > Export > Solver Deck and hitting export.
- This step is only necessary if you are changing the MotionView model to accommodate a different vehicle. Obtain the input parameters for the Twin Activate rear wheel steering controller.
Mass & Inertia Properties
-
- In the MotionView full vehicle model, under the Geometry tab, select the sigma next to the Bodies icon to open the CG & inertia summary. Retrieve the mass and inertia properties.
- In the MotionView full vehicle model, under the Geometry tab, select the sigma next to the Bodies icon to open the CG & inertia summary. Retrieve the mass and inertia properties.
Roll Rate/Steer Ratio/Steer Camber Gain (Option 1 – Quick Setup)
-
- Create a kinematics and compliance analysis (KnC) in MotionView. In the Entity Browser, follow Vehicle Tools > Events > General.
- Run the KnC analysis with roll analysis and steering analysis selected. Change the maximum steer angle to 180 degrees under vehicle parameters in the Entity Editor.
- Obtain the parameters from the output Suspension Design Factors (SDF) files. The roll rate can be found at any timestep. The camber angle and wheel angle can be taken at 12.5 seconds when the steering wheel angle is 180 degrees. Use chamber angle and wheel angle to compute steer camber gain and steer ratio.
- Create a kinematics and compliance analysis (KnC) in MotionView. In the Entity Browser, follow Vehicle Tools > Events > General.
Roll Rate/Steer Ratio/Steer Camber Gain (Option 2 – Better for debugging)
-
- Create a front half car model in MotionView with the same parameters present in the full car model.
- Perform a roll analysis and steering analysis which are found by clicking Events.
- Obtain the parameters from the output sdf files.
- Create a rear half car model.
- Perform a roll analysis.
- Obtain the parameters from the output sdf file.
- Setup the Twin Activate model.
- Open the Vehicle_Rear_Wheel_Steer_Control.scm file in Twin Activate.
- Double click the Full Vehicle MBD Model block to open the superblock. Double click the MotionSolveSignals block to open the block’s parameters.
- Change the input file name to the .xml created in the Results folder when exporting the solver deck. This connects the MotionView model to the Activate model.
- Hit the save icon next to MRF output filename, name the file, and hit save.
- Steps vi-viii are only necessary if you are changing the MotionView model to accommodate a different vehicle. Otherwise, skip to simulation setup.
- Click the model icon in the top banner to open the Compose initialization script which takes input parameters for the rear wheel steer controller.
- Update the inputs found between line 3-42 in the script.
- Update line 99 with the appropriate .tir file location if you change the tires in the MotionView model.
SIMULATION STEPS
The simulation simulates a Sedan driving in a straight line and then performing a rapid lane change. With rear wheel steering, the rear end of the vehicle does not overshoot the desired path.
- Select run in the Activate model to begin the co-simulation.
- Dialog 1: Enter a 1 to generate the reference map.
- Dialog 2: Leave the default settings and select ok.
- Dialog 3: Leave the default settings or enter a 1 in the first box to select an alternative tire file.
- Navigate to the results folder and view the h3d in HyperView to animate the results.
- The results of the baseline vehicle run can be overlayed by hitting open, selecting the baseline run h3d file, checking overlay, and hitting apply.
Post-Requisite
RESULTS
The vehicle with active rear wheel steering remains stable during the single lane change. However, the passive system significantly overshoots the lane during the lane change, posing risk to the driver and passengers in the vehicle. After the maneuver, the passive system overcorrects putting the passengers in danger again.
Single Lane Change Maneuver
Red – Passive System | Blue – Active Rear Wheel Steer
Single Lane Change Maneuver
Red – Passive System | Blue – Active Rear Wheel Steer
Performing a brake in turn maneuver with both systems yields similar results to the single lane change. The active rear wheel steering system remains stable while the passive system over-corrects and leaves the road. Plots of sideslip angle show the rear wheel steering system reduces sideslip angle allowing the vehicle to remain on the road.
Brake in Turn Maneuver
Red – Passive System | Blue – Active Rear Wheel Steer
Brake in Turn Maneuver
Sideslip Angle & Acceleration
The pattern of greater vehicle stability for the RWS system continues for a double lane change maneuver. The RWS system reduces the sideslip angle and yaw rate.
Double Lane Change Maneuver
Red – Passive System | Blue – Active Rear Wheel Steer
Brake in Turn Maneuver
Sideslip Angle, Yaw Rate, Lateral Acceleration, and Steer Angles
CONCLUSION
In this article, we developed two multibody dynamics models of vehicles. One vehicle utilizes active rear wheel steering while the other does not. To build an accurate simulation with active rear wheel steering, the RWS model used co-simulation with Twin Activate and Compose. Compose generated a reference map of stable conditions, Twin Activate managed the RWS controller, and MotionSolve handled the vehicle physics.
After building the model, post processing was done in HyperView and HyperGraph. Single lane change, brake in turn, and double lane change maneuvers showed the active rear wheel steering system is more stable than the passive system. The RWS system reduces sideslip angle and yaw rate allowing the vehicle to handle emergency maneuvers at higher speeds.
AUTHORS
Spyridon Mallios, Technical Specialist - Model Based Systems
John Dagg, Systems Engineering Intern
Christopher Fadanelli, Solution Engineer - Systems Integration