Verification Of Baja and FSAE Kinematics and Compliance Using MotionSolve
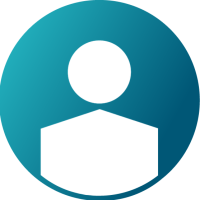

Overview
CHALLENGE
Assessing Kinematic and Compliance of Baja and FSAE Vehicles.
PREFACE
As an engineering student participating in BAJA and FSAE competitions, you face significant challenges in learning on the job designing, testing, and refining a complete competition vehicle. This often means countless late nights spent troubleshooting and overcoming unexpected issues that inevitably happen with a new design. Key concerns include optimizing vehicle performance, balancing weight distribution, ensuring safety, and meeting competition regulations. Good simulation software can help ease some of these concerns by allowing designs to be vetted carefully in a low-cost, no-risk virtual environment- resulting in an optimized, competitive design the first-time metal is cut and assembled!
Altair MotionSolve, a multibody dynamics (MBD) software toolset, provides a comprehensive vehicle library that simplifies the design process and allows for advanced simulation of vehicle dynamics. MBD offers a deeper analysis of kinematics & compliance and allows 3D calculation of internal loads between moving parts under real operating conditions. This includes capturing dynamic effects, which kinematics tools like Optimum G may not fully account for. While a lumped parameter 1D tool like Carsim is good for vehicle dynamics, 3D MBD tools like MotionSolve offer the ultimate advantage in ending up with a competitive and weight-optimized of FSAE/Baja chassis using a streamlined set of models.
INTRODUCTION
Vehicle suspension design can rapidly change due to various factors. These changes can be driven by packaging constraints, the availability and compatibility of components, and the need to meet specific kinematic requirements. Kinematic requirements include verifying the Camber, Wheel Rate, Ground Reaction Force, Motion Ratio, Ackerman, Roll and Ride steer.
Additionally, considerations such as ride comfort, handling performance and weight distribution can also significantly influence suspension design choices.
At the half-vehicle level, users can verify the kinematics of the suspension with a detailed report before assembling the full vehicle. This verification process is crucial for several reasons, which are outlined below along with the types of analyses that can be performed:
Ensuring Safety and Reliability:
Verifying the suspension kinematics ensures that the vehicle will handle correctly under various driving conditions. Any flaws or weaknesses in the suspension system can be identified and corrected before they pose a risk to the safety and reliability of the vehicle.
Optimizing Performance:
Properly analyzing and optimizing the suspension kinematics at the half-vehicle level allows for adjustments that can enhance the overall performance of the vehicle. This includes improving handling, stability, and ride comfort.
Educational Value:
For students, this process provides practical experience in vehicle dynamics and suspension design. It helps them understand the importance of each component and how it contributes to overall vehicle performance. An additional test that can performed is verifying the loading encountered on the components through a Static Load Analysis.
In this example, the model will be updated to alter several key attributes:
- Ride Steer
- Ride Camber Rate
- Ground Reaction Force
- Wheel Rate
- Motion Ratio
- Roll Steer
- Ackerman Steering
An Excel spreadsheet named KnC Results.xlsx is dedicated to recording and analyzing these attributes. The Spring Rate, which defaults to 150 N/mm, can be recorded from the stiffness rate input of the suspension's coil spring. Orange rows in the spreadsheet indicate the pages in the generated report where these values should be recorded. The Ackerman steering data can be found in the .sdf file generated by MotionSolve.
For the Ride Steer Analysis, jounce and rebound data should be recorded, ideally at approximately 25 mm of travel. This data will be used for the rest of the analysis documented under the Ride Test section.
Pre-Requisite
SOFTWARE REQUIREMENTS:
-
- Operating System: Windows
- MotionView (2023 or newer)
- MotionSolve (2023 or newer)
- Workable knowledge of MotionView and Vehicle Modeling preferred.
- Access to Baja FSAE Library
Model Definition
- Front_FSAE Zip File (refer to attachments).
Usage/Installation Instructions
Modeling Steps: Analyzing Default Kinematics and Compliance Analysis
- Load in the Front_FSAE_Default.mdl
- With the Baja_FSAE_Library loaded in (refer to KB0124791), access the event wizard and load a Kinematics and Compliance Analysis into the model.
- Accept all defaults for the analysis from the pop-up windows.
- Run the model to undergo the full analysis.
- Once the analysis is complete. Access the Reports tool to load in the SDF based report generated from the recent Kinematic and Compliance run.
- With the report generated, refer to KnC Results.xlsx and input the required data based on the dedicated page.
- To record the “Steering Test: SDF Output at 82.5000 seconds”. In your file browser, navigate to the output directory and open the .sdf file (in any notepad editor) generated from MotionSolve.
- In the notepad editor, search for 82.5000. This is when the steering wheel is at full lock. In the data generated for that timestep, record the first set of Ackerman results.
RESULTS
Running the default model without any modifications yields the following results:
- Ride Test:
- Ride Steer: 0.00687 degrees per millimeter (deg/mm)
- Ride Camber Rate: 0.05986 degrees per millimeter (deg/mm)
- Stationary Ground Reaction Force: 606 Newtons (N) on each tire
- Wheel Rate: 37.44 Newtons per millimeter (N/mm)
- Motion Ratio: 50%
- Roll Test:
- Roll Steer Gradient: 0.084 degrees per degree (deg/deg)
- Steering Test:
- Turning Capability: The vehicle can handle a turn with a diameter of 12.49 meters with the inner outer wheel angles being 21.54 and 37.71 degrees respectively.
These results provide a comprehensive baseline for the vehicle's suspension and handling characteristics, offering insights into its ride comfort, stability, and steering performance under standard conditions.
In the next steps, the vehicle’s shock positioning will be altered to review the changes in the wheel loading.
Modeling Steps: Alter Wheel Loading.
- Navigate to Push rod outer point.
- Shorten the push road by updating the Y value to -500 mm.
- Run full analysis.
- Navigate to the reports icon and overlay the newly generated report over the default report.
- Record the new results in the excel spreadsheet.
RESULTS
Running the model with the push rod modification yields the following results:
- Ride Test:
- Ride Steer: 0.00769 degrees per millimeter (deg/mm)
- Ride Camber Rate: 0.05986 degrees per millimeter (deg/mm)
- Stationary Ground Reaction Force: 568.5 Newtons (N) on each tire
- Wheel Rate: 28.37 Newtons per millimeter (N/mm)
- Motion Ratio: 43.5%
- Roll Test:
- Roll Steer Gradient: 0.093 degrees per degree (deg/deg)
- Steering Test:
- Turning Capability: The vehicle can handle a turn with a diameter of 12.46 meters with the inner outer wheel angles being 21.55 and 37.86 degrees respectively.
By altering the push rod location, several key suspension characteristics were negatively impacted. The ride and roll steer increased, leading to degraded handling capabilities. Specifically, the ground reaction force, wheel rate, and motion ratio all decreased, resulting in a less stable and responsive vehicle. These changes collectively worsened both the handling and ride quality, making the vehicle more difficult to control and less comfortable to drive.
Next, the upper control arms bushing’s locations are calibrated to reduce the camber effect.
Modeling Steps: Alter Ride Camber Rate.
- Navigate to UCA frnt bush point.
- Shorten the control arm by updating the Y value to -310 mm. Increase the height of the Z value to 300 mm.
- Update the UCA rear bush point with the same values from the previous step.
- Run full analysis.
- Navigate to the reports icon and overlay the newly generated report over the previous reports.
- Record the new results in the excel spreadsheet.
RESULTS
Running the model with the relocating the upper control arm bushings yields the following results.
- Ride Test:
- Ride Steer: 0.00561 degrees per millimeter (deg/mm)
- Ride Camber Rate: 0.05702 degrees per millimeter (deg/mm)
- Stationary Ground Reaction Force: 569.3 Newtons (N) on each tire
- Wheel Rate: 27.42 Newtons per millimeter (N/mm)
- Motion Ratio: 42.8%
- Roll Test:
- Roll Steer Gradient: 0.069 degrees per degree (deg/deg)
- Steering Test:
- Turning Capability: The vehicle can handle a turn with a diameter of 12.46 meters with the inner outer wheel angles being 21.55 and 37.86 degrees respectively.
By updating the upper control arm points, improvements were observed in the suspension characteristics. The camber, ride steer, and roll steer all showed notable enhancements compared to the previous modifications, leading to better ride quality and handling performance. These adjustments resulted in a more stable and responsive vehicle. The remaining outputs, such as ground reaction force, wheel rate, and motion ratio, experienced negligible changes, indicating that the primary benefits were concentrated in the improved steering and camber dynamics.
The last step is to modify the tierod positioning to change the Ackerman Steering.
Modeling Steps: Alter Ackerman Steering.
- Navigate to Otr tierod ball jt point.
- Shorten the tie rod by updating the X and Y value to 540 and -560 mm respectively.
- Run full analysis.
- Navigate to the reports icon and overlay the newly generated report over the previous reports.
- Record the new results in the excel spreadsheet.
RESULTS
Running the model by shortening the tie rod yields the following results.
- Ride Test:
- Ride Steer: 0.00303 degrees per millimeter (deg/mm)
- Ride Camber Rate: 0.05658 degrees per millimeter (deg/mm)
- Stationary Ground Reaction Force: 569.3 Newtons (N) on each tire
- Wheel Rate: 27.42 Newtons per millimeter (N/mm)
- Motion Ratio: 42.8%
- Roll Test:
- Roll Steer Gradient: 0.021 degrees per degree (deg/deg) for left wheel and 0.033 degrees per degree (deg/deg) for the right wheel
- Steering Test:
- Turning Capability: The vehicle can handle a turn with a diameter of 23.12 meters with the inner outer wheel angles being 16.43 and 13.26 degrees respectively.
By shortening the tie rod length and adjusting its angle, the suspension characteristics showed significant improvements. Camber, ride steer, and roll steer all exhibited notable enhancements compared to the previous modifications, resulting in better ride quality and handling performance. However, this modification came at a cost: the Ackerman steering turn diameter nearly doubled, and the wheel angles decreased to almost half of their original value. Consequently, the vehicle now requires wider turns, which is not ideal for competitive performance.
Post-Requisite
CONCLUSION
Designing suspension components can turn into an iterative process to satisfy vehicle requirements. For instance, altering the push rod, which affects the shock loading, can impact the ground reaction force, wheel rate, and motion ratio. Additionally, updating the upper control arm bushing locations can influence the camber of the vehicle. Similarly, changes to the tie rod position, length, and angle from the rack to the knuckle will affect the ride, roll, and Ackermann steering attributes. Each adjustment necessitates careful consideration and testing to ensure optimal performance and vehicle dynamics. Further analysis of the vehicle can be applied to verify the loading in the vehicles components after encountering various loading scenarios.