Leaf Spring SAE J510 Test Rig in MotionSolve
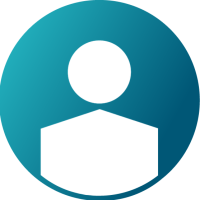

Overview
PREFACE
Leaf springs are crucial to automotive suspension systems for their ability to distribute weight and absorb road shocks. Found commonly in trucks and heavy-duty vehicles, leaf springs consist of multiple layers of tempered steel connected at their ends by clips or bolts, forming an arch. Despite advancements in suspension technology, like coil springs and air suspensions, leaf springs remain essential in off-road vehicles and utility trucks where load-carrying capability is paramount.
INTRODUCTION
Automotive engineers designing vehicle suspensions face many challenges when designing leaf springs. Load capacity, stiffness, geometry, and mass are just a few coupled parameters that require careful consideration and analysis. Further considerations include stress, fatigue, corrosion, power hopping, leaf failure modes, and more. Computer simulation makes implementation of leaf springs in modern vehicles possible by allowing users to predict the performance of leaf springs under a wide range of scenarios. MotionSolve, a multi-body dynamics tool developed by Altair, is one such tool used to analyze vehicle performance and handling. Leaf springs can be built and added into a full vehicle model for kinematics and compliance testing or road event simulation. The software also features standard tests like the SAE J510 and a leaf spring and shackle test. The SAE J510 test is used to calculate the leaf spring’s stiffness curve and validate that manufactured parts match the original design. A loading block pushes the leaf spring from the free position to the curb position, then the design position, and lastly the metal-to-metal position.
In this example, we will build a leaf spring model in MotionSolve with the leaf spring builder. The leaf spring builder includes standard leaf spring design options including those for leaf types, leaf ends, leaf geometry, clips, the shackle, and axle mounting. After building a leaf spring, we will perform an SAE J510 test to predict the stiffness curve of the leaf spring. Then we will add the leaf spring model to a rear half-car model and perform a kinematics & compliance test to determine the vertical stiffness and rates.
Pre-Requisite
SOFTWARE REQUIREMENTS
MotionView (2024 or newer)
MotionSolve (2024 or newer)
MODEL FILES
Leaf_Spring.zip (See attachments)
Usage/Installation Instructions
MODEL SETUP & SIMULATION STEPS
- Start a new session in MotionView.
- Open the leaf spring builder.
- If you want to skip the spring building, open the leafSpringSystem.lpf by opening the menu icon in the top right corner. Proceed to step 14.
- Select “Free” for the data shape condition under “General”. This creates the leaves as an assembled stack but with no external loading.
- Add leaves until there are 6 total leaves.
- Import the shape profile for each leaf found in the attached zip file.
- Change leaves 2-4 to graduated leaves and leaves 5-6 to auxiliary under details.
- Add 5 evenly spaced contacts for leaves 2-6.
- Specify the leaf end types, radius, and position.
- Under “Clip Details,” add 2 clips and specify the location.
- Modify the clip properties.
- Change the axle type to over slung and change the inactive lengths to 65 mm and preload to 800 N.
- Under “Build,” select “Assemble leaves and apply preload” and hit build to generate the leaf spring model.
- Under “Test,” select the SAE J510 test type. Specify a curb position of 110 mm.
- Select run test rig to run the analysis.
- In a new MotionView session, create a half car model with a leaf spring suspension.
- Delete the default leaf springs.
- Import the leaf spring model definition (mdl) files. Right click on the “Rear Leaf Spring” system, select import, and import the leaf spring system mdl file.
- Update the leaf spring system attachments for the leaf spring systems and travel lock systems.
- Create a KnC event.
- Run the analysis.
The half-car models are available in the attached zip folder. Open the mdl file and run the analysis to review the results.
Post-Requisite
RESULTS
After running the leaf spring test rig, the results can be found in the folder selected on the test rig setup dialog. Opening the .mdl file will show the multibody dynamics model created in MotionView. The model uses beam elements to model the leaf spring leaves. Bushing elements are created between joints to connect the leaf spring to ground body for component tests.
Model of a Leaf Spring in MotionView
Opening the .h3d file will show an animation of the test performed. The vector plot option can be used to show the joint and contact forces developed during the test.
Animation of the SAE J510 Test Rig
Contact and Joint Forces in the Leaf Spring
After running the test, the leaf spring builder automatically plots force vs displacement and stiffness vs displacement curves. These curves can be compared to bench testing to validate manufactured leaf springs.
Force vs Displacement Plot
Stiffness vs Displacement Plot
After completing the Kinematics & Compliance test, a report can be generated in MotionView which contains plots of the suspension design factors including vertical stiffness and lateral stiffness. A suspension design factor (sdf) file is also generated in the results directory which can be opened to view suspension design factors at each timestep of the analysis. At the end of the report, users can view an animation of the system level model undergoing the K&C test.
Kinematics and Compliance Test Animation
Adjusting the model allows users to quickly test design changes and evaluate performance. For example, changing the leaf spring width from 60 mm to 80 mm results in an increase in vertical stiffness from 170.94 N/mm to 225.54 N/mm.
CONCLUSION
In this example, we built a leaf spring using MotionView’s leaf spring builder. Then we ran a SAE J510 test, a simple component level test used to validate that the spring stiffness of manufactured springs matches the design value. The test automatically generates force vs displacement and stiffness vs displacement curves. The software can also perform a Kinematics and Compliance test, an industry-standard used to evaluate suspension design factors. The analysis generates a text file and plots with the suspension design factors. In addition to the above tests, MotionSolve includes an Npost test, static load analysis, and tire envelope analysis which can aid designers and engineers in the process of developing a vehicle suspension.
Automotive engineers can also leverage MotionSolve’s vehicle tools to build full-car models and perform vehicle events ranging from lane changes to custom road courses. Powerful post-processing tools allow users to extract and plot key performance indicators to make informed design decisions.
AUTHORS
John Dagg, Systems Engineering Intern
Christopher Fadanelli, Solution Engineer – Systems Integration