Baja and FSAE Library Overview in MotionSolve
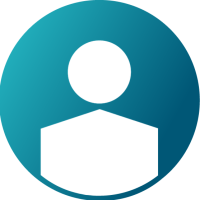

Overview
CHALLENGE
Assessing Formula and Baja performance under real world scenarios.
PREFACE
As an engineering student participating in BAJA and FSAE competitions, you face significant challenges in learning on the job designing, testing, and refining a complete competition vehicle. This often means countless late nights spent troubleshooting and overcoming unexpected issues that inevitably happen with a new design. Key concerns include optimizing vehicle performance, balancing weight distribution, ensuring safety, and meeting competition regulations. Good simulation software can help ease some of these concerns by allowing designs to be vetted carefully in a low-cost, no-risk virtual environment- resulting in an optimized, competitive design the first-time metal is cut and assembled!
Altair MotionSolve, a multibody dynamics (MBD) software toolset, provides a comprehensive vehicle library that simplifies the design process and allows for advanced simulation of vehicle dynamics. MBD offers a deeper analysis of kinematics & compliance and allows 3D calculation of internal loads between moving parts under real operating conditions. This includes capturing dynamic effects, which kinematics tools like Optimum G may not fully account for. While a lumped parameter 1D tool like Carsim is good for vehicle dynamics, 3D MBD tools like MotionSolve offer the ultimate advantage in ending up with a competitive and weight-optimized of FSAE/Baja chassis using a streamlined set of models.
INTRODUCTION
Since 2017, we’ve maintained a dedicated library for Baja and FSAE vehicles. Enhancements have been introduced to the software since then. Now we offer an updated library compatible with software versions 2023 and above. With this library, users can create and enhance their Baja and FSAE vehicles with ease.
At the half-vehicle level, users can verify the kinematics and loading of the suspension with a detailed report before assembling the full vehicle. This verification process is crucial for several reasons, which are outlined below along with the types of analyses that can be performed:
Ensuring Safety and Reliability:
Verifying the suspension kinematics ensures that the vehicle will handle correctly under various driving conditions. Any flaws or weaknesses in the suspension system can be identified and corrected before they pose a risk to the safety and reliability of the vehicle.
Optimizing Performance:
Properly analyzing and optimizing the suspension kinematics at the half-vehicle level allows for adjustments that can enhance the overall performance of the vehicle. This includes improving handling, stability, and ride comfort.
Cost Efficiency:
Identifying and addressing potential issues in the suspension system early in the design process can save significant time and resources. Making changes at the full vehicle level can be more complex and costly.
Integration with Full Vehicle’s:
Validating the suspension system before integration to a full vehicle model ensures no errors will be present. This utilizes the Crawl – Walk- Run method, by reducing and validating the vehicle in smaller portions helps prevent unforeseen interactions when the systems are converged to the full vehicle model.
Educational Value:
For students, this process provides practical experience in vehicle dynamics and suspension design. It helps them understand the importance of each component and how it contributes to overall vehicle performance.
The types of analyses that can be used for the half-vehicle model includes:
- Kinematics and Compliance
- Static Ride
- Static Roll
- Single Wheel
- Steering
- Static Load
- Trim Height Analysis
- Tire Envelope
Once the front and rear suspensions have been verified, the systems can be imported into a full vehicle model. This allows for comprehensive testing where the full vehicle can undergo ride and handling events. The types of events include:
Ride Quality Tests:
- Bump and Pothole Tests: Evaluating the vehicle's ability to absorb road imperfections and provide a smooth ride.
- Rough Road Testing: Assessing the suspension’s performance on uneven or unpaved roads.
Handling Tests:
- Slalom Course: Measuring the vehicle’s agility and responsiveness in a series of tight turns.
- Lane Change Maneuvers: Evaluating stability and control during sudden lane changes.
Braking Tests:
- Emergency Braking: Testing the vehicle’s stopping distance and stability under hard braking conditions.
Steering Response:
- On-Center Feel: Evaluating steering precision and feedback during straight-line driving.
- Cornering: Assessing steering accuracy and effort required during turns.
NVH (Noise, Vibration, and Harshness):
- Interior Noise Levels: Measuring sound levels within the cabin during different driving conditions.
- Vibration Analysis: Evaluating the transmission of vibrations through the vehicle’s structure.
Dynamic Load Transfer:
- Acceleration and Braking Loads: Assessing how weight transfer affects vehicle stability during acceleration and deceleration.
- Cornering Loads: Evaluating lateral load transfer during turns
The type of events available in MotionView are listed below.
- Straight Line Acceleration
- Straight Line Braking
- Constant Radius
- Double Lane Change
- Single Lane Change
- Brake and Turn
- JTurn Steering
- Pulse Steering
- Road Course Drive
- Sinusoidal Steer
- Slalom Course
- Step Steering
- Swept Sine Steering
- Swept Steering
- Power Off Straight Line
- Throttle Off Corner
- Throttle Off Turn In
Pre-Requisite
SOFTWARE REQUIREMENTS:
-
- Operating System: Windows
- MotionView (2023 or newer)
- MotionSolve (2023 or newer)
- Workable knowledge of MotionView and Vehicle Modeling preferred.
Usage/Installation Instructions
Library Definition
- Baja_FSAELibraries Zip File (refer to attachments).
Post-Requisite
Modeling Steps:
- Enable vehicle tools in extensions. File -> Extensions -> Vehicle Tools
- In the Vehicle Tools menu, select Libraries.
- Alter the Wizard Library to “User/Custom library”.
- Update each input to refer to the Baja_FASE_Libraires folder.
-
- Assembly Wizard file: “<directory>/Baja_FSAELibraies/compLib_model_wizard.wzd”.
- Task Wizard File: “<directory>/Baja_FSAELibraies/compLib_task_wizard.wzd”.
- MDL standard include file: “<directory>/Baja_FSAELibraies/ std_inc.mdl”.
- Wizard library directory: “<directory>/Baja_FSAELibraies”.
- Report log file: Default.
-
- Utilize the Assembly Wizard to construct desired competition vehicle.
- Update the suspension model to prototype specifics.
- Analyze and verify each Half Car model with events from the Task Wizard (refer to Vehicle Modeling training).
- Once verified, construct the full vehicle.
- Export/Import suspension systems from the half Car model into the Full vehicle model.
- If FSAE is selected, verify the “Vehicle Body CG” point is set to (1500,0,300) for default analysis.
- If BAJA is selected, verify the “Vehicle Body CG” point is set to (1200,0,500) for default analysis.
- Use the Entity Browser to import Full vehicle events into the model.
- Update event to desired run parameters.
- Run model and extract results.
RESULTS
Each vehicle can undergo a comprehensive range of evaluation tests, from half-car simulations to full-vehicle assessments. Detailed reports are accessible through the "Analyze" or "Vehicle Tools" menus. Additionally, further results can be visualized and plotted using HyperGraph for detailed analysis.
CONCLUSION
With the Baja and FSAE Library, student engineers can focus on learning how changes in component layout and properties affect system and vehicle level performance attributes. Loads due to real operating environment can be easily extracted as an input to finite element analysis. Full vehicle dynamics can be simulated, and critical control systems can be modeled as well. As a result, teams can make data-driven decisions to refine their designs, improve vehicle dynamics, and gain a competitive edge.