Landing Gear Dynamics in Inspire Motion
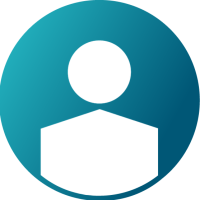

Overview
INTRODUCTION
Multibody dynamics (MBD) simulation is the study of the dynamics of interconnected rigid or flexible bodies. Using MBD simulation, designers and engineers can analyze the motion, forces, and stresses in a wide range of mechanisms. By implementing simulation early in the design phase, engineers can rapidly test and compare multiple designs to optimize performance.
In this example, we build a MBD model of an aircraft landing gear and explore the required actuator force for two different actuator mounting positions. Using the MBD model, we find the optimal actuator mounting position. Then we analyze the stress in the shock housing under the effect of landing forces to evaluate material choices for the shock housing.
Pre-Requisite
SOFTWARE REQUIREMENTS
Altair Inspire (2024 or newer)
MODEL FILES
Landing_Gear_Model.zip (See attachments)
Usage/Installation Instructions
MODEL SETUP & SIMULATION STEPS
- Import Landing_Gear_Geometry.x_b into Inspire.
- Change gravity to point in the negative Y direction.
- Ground the two pins and actuator mount.
- Create rigid groups between the wheel rims and tires.
- Create joints between the parts.
- Lock the hinge joints between the wheels and shock piston to prevent the wheels from spinning.
- Create a spring between the shock housing and piston.
- Change the spring stiffness to 220 N/mm and damping to 22 Ns/mm.
- Change the free length to 490 mm.
- Create an actuator between the actuator mount and the lower mounting point on the intermediate link.
- Change the mount pivot type to spherical.
- Change the actuator to a step profile with a displacement of 750 mm in 4 seconds.
- Run an analysis for 4 seconds and review the motion taking note of the required actuator force.
- Move the actuator mounting point on the intermediate link to the upper mounting point.
- Change the actuation length from 750 mm to 925 mm.
- Rerun the motion analysis and compare the force required to move the landing gear into the stowed position.
- Lock the actuator.
- Create an actuator on the bottom of the shock piston to simulate landing forces.
- Change the type to force.
- Create an impulse profile that exerts 5e4 N for 0.3 seconds.
- Run an analysis for 0.5 seconds and review the results.
- Analyze the shock housing for the 5 peak loads using the analyze part tool.
- Review the stresses on the shock housing.
- A complete model called Landing_Gear_Motion_Example.stmod is available in the attachment Landing_Gear_Model.zip. There are three actuators present in the model to show all cases of interest in one model. Suppress two out of three for a functioning model.
Post-Requisite
RESULTS
The motion of each landing gear configuration is available after analysis. The lower mounting position allows for a greater range of motion and a smaller actuator deployment length at 750 mm. The upper mounting position requires an actuator deployment length of 925 mm.
Landing Gear Motion for the Lower Mounting Option
Landing Gear Motion for the Upper Mounting Option
The lower mounting position allows for a range of motion of 93.5 degrees while requiring half the total force of the upper mounting position. Meanwhile, the upper mounting position limits the range of motion to only 84 degrees. The lower mounting position would be a better option in general because of the larger range of motion, lower actuator deployment, and lower required force.
Comparison of Landing Gear Angular Displacement
Comparison of Required Actuator Force
The shock housing experiences significant stresses during takeoff and greater stresses during a landing. In this model, landing forces are simulated with an impulse of 50,000 N for 0.3 seconds. During this time, the housing reaches a maximum stress of 87 MPa at stress raisers visible in the contour plot. The stress is significantly below the yield strength of aluminum and composites such as carbon fiber making them suitable choices for a shock housing material.
Von Mises Stress on the Shock Housing
CONCLUSION
In this example, we imported the geometry of a landing gear into a MBD software, Altair Inspire. After setting up the model, we compared the forces required to move the landing gear into its stowed position for two mounting options. The lower mounting position required less force and reached the full range of motion required to store the landing gear. We also evaluated the stresses on the shock housing as the landing gear experiences landing forces. The shock housing stresses were below yield for many common aluminums and composites like carbon fiber making them ideal and lightweight choices. Overall, multibody dynamics simulation is a powerful tool used to evaluate the motion, forces, and stresses in a mechanism or assembly while enhancing the design process.
AUTHORS
John Dagg, Systems Engineering Intern
Chris Fadanelli, Solution Engineer - Systems Integration