Wing Landing Gear Deployment & Optimization in Inspire Motion
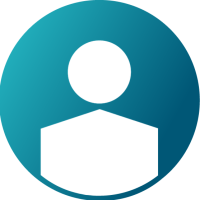

Overview
INTRODUCTION
The landing gear on any aircraft is a critical feature paramount to passenger safety which requires careful and comprehensive design and analysis. The landing gear must survive takeoffs, taxiing, and most importantly landings, with a large margin for safety. It should fold into the aircraft to occupy as little space as possible. Finally, as a component on an airplane, it must also be lightweight and durable. In order to meet all the requirements, simulation, specifically multibody dynamics and finite element analysis, can be used to evaluate system performance and improve design.
Multibody dynamics (MBD) simulation is the study of the dynamics of interconnected rigid or flexible bodies. Using MBD simulation, designers and engineers can analyze the motion, forces, and stresses in a wide range of mechanisms, including landing gears. By implementing simulation early in the design phase, engineers can rapidly test and compare multiple designs to optimize performance. Altair’s Inspire is a unique simulation tool where pre-processing, solving, and post-processing can be done in a single environment. CAD data can be imported or built using a full suite of geometry tools. Then a multibody dynamics simulation can be performed to generate motion after which loads generated during motion can be used to optimize a part to reduce mass.
In this example, we will build a MBD model of a wing fairing landing gear in Altair’s Inspire. We will examine the motion of the landing gear deployment and retraction. Then we will simulate the loads from landing and use the forces extracted from the MBD simulation to optimize a control arm to reduce the weight.
Understanding the Model Definition in Inspire Motion
The model contains a six wheeled landing gear housed in a plane wing fairing. During the simulation, the landing gear begins in the deployed state. The landing gear and door are controlled using actuators with specified displacement over time curves. The landing gear retracts and then redeploys. At the end of the simulation, landing forces are simulated by applying an impulse to bogie which results in visible shock displacement.
Pre-Requisite
SOFTWARE REQUIREMENTS
Altair Inspire (2024 or newer)
MODEL FILES
Wing_Landing_Gear_Model.zip (See attachments)
Usage/Installation Instructions
MODEL SETUP & SIMULATION STEPS
- Open Wing_Landing_Gear_Baseline.stmod in Inspire.
- Analyze the motion for 30 seconds at 50 Hz.
- Review the landing gear motion.
- Analyze the bottom aft brace with a 10 mm mesh size.
- Setup the brace for optimization.
- Isolate the brace and connected parts.
- Partition the brace at each joint using the Partition tool in the Geometry tab.
- Remove the pockets with the Simplify tool.
- Rebuild the joints.
- Designate the brace as a design space.
- Add the partitions and design space to a rigid group.
- Apply a symmetrical constraint in the Structures tab.
- Align one symmetrical plane to the part and disable the other planes.
- Apply a split draw constraint.
- Run a motion analysis with the new design part.
- Optimize the part for stiffness with a target of 40% design volume.
- Use wrap and PolyNURBs tools to smooth the part if desired.
- Analyze the part for stress and compare the results to the baseline brace.
Post-Requisite
RESULTS
Landing Gear Motion
Bottom Aft Brace Stresses Baseline
Bottom Aft Brace Stress Closeup - 70 kg
Optimized Part After Processing - 60.5kg
Optimized Part Stresses - 60.5 kg
CONCLUSION
The landing gear is a critical component in aircraft used for all ground operations. With a plethora of design requirements, the landing gear requires extensive design and analysis. Simulation, including MBD and FEA, can be used to evaluate and improve the design from hardpoint studies to component lightweighting. In this example, we showed how simulation can be used to analyze the motion of the landing gear and minimize the weight of a component. Further simulation can be used to get more detailed and comprehensive results. Altair’s MotionView can be used to prepare a model for fatigue analysis using the loads extracted from a motion analysis. Alternatively, co-simulation with Altair’s Twin Activate could be used to accurately model the workings of the landing gear’s hydraulic actuators. Ultimately, proper utilization of simulation can improve the design process and lead to better end products.
AUTHORS
John Dagg, Systems Engineering Intern
Christopher Fadanelli, Solution Engineer - Systems Integration