Excavator Dynamic Response and Load Estimation for Fatigue Analysis in MotionSolve, Twin Activate, and EDEM
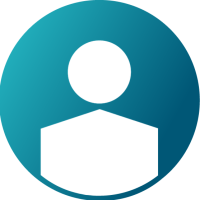

Overview
INTRODUCTION
The excavator is a staple of construction equipment seen on construction sites around the world. The simulation of heavy machinery, like the excavator, is crucial for optimizing design and improving performance. Utilizing multibody dynamics (MBD) software, engineers can analyze the mechanical systems to understand excavator stability, component stresses, and more. When combined with hydraulics simulation, engineers can test lifting capacity and operation speed to understand overall system performance. Tweaking and testing pump sizes, fluid properties, valve settings, and geometry changes is made quick and easy with simulation, saving time and cutting costs.
In this example, we will build a multibody dynamics model from excavator CAD data in Altair MotionSolve. The MBD model will provide insight into component stresses and the excavator’s dynamic response during scooping and dumping operations. The excavator will operate on iron ore and coal modeled using EDEM, a bulk material model built using the discrete element method (DEM). A hydraulics model built in Altair Twin Activate, an intuitive 1D physics-based block modeling software, will control the hydraulic actuators for the boom, arm, and bucket. The hydraulics model will provide data on the force required to achieve scooping and dumping operations. Data from the hydraulics model can be used to size hydraulic cylinders for the excavator. Combined, the multibody dynamics, hydraulics, and bulk material simulations will provide a comprehensive analysis of the excavator’s dynamics allowing loads to be extracted for fatigue analysis.
Understanding the Model Definition in MotionSolve
The multibody dynamics model is built from CAD data in MotionView.
- Bodies are created for each component.
- Bodies use CAD geometry and material properties to accurately calculate the mass and inertial properties. Alternatively, users can input mass and inertial properties.
- Rigid joints are created between components to mathematically represent real-world joints.
- The turret follows a displacement motion profile.
- The actuators are prepared for hydraulics simulation with a Twin Activate functional mock-up unit (FMU).
- The MBD model outputs a reference actuator displacement profile and actual actuator displacement to the FMU.
- The MBD model receives a force from the FMU which is what drives the actuator’s motion.
- A DEM or discrete element method system is created to prepare the model for co-simulation with EDEM.
- Each body the discrete element model interacts with is added as an attachment to the system.
- The excavator boom and arm are replaced with flexible bodies.
- Flexible bodies are prepared in OptiStruct with the FlexPrep tool available in MotionView.
- Flexible bodies account for the deformation of components and allow users to review contour plots of stresses and displacements.
- Outputs are created to monitor component displacements, velocities, and joint forces.
Understanding the Model Definition in Twin Activate
A Twin Activate model is built to simulate the hydraulics system.
- The actual and reference actuator displacement act as inputs into the model.
- A proportional PID controller uses the error in the displacement to provide a response to the valve controlling the hydraulic actuator.
- The valve is a mathematical representation of a 4-way valve which follows a second order response to the input signal.
- The valve is connected to the pump and tank which are constant sources of pressure.
- The valve is also connected to the double-acting actuator modeled as a piston cylinder device with HLP 46 as the working fluid.
- Relief valves between the tank and actuator ports prevent excessive pressure build up.
- The piston cylinder uses the Stribeck model of friction and accounts for volumetric losses to provide an accurate model of a hydraulic cylinder.
- After calculating the actuator force, the force is sent back to the multibody dynamics model.
- The whole system, built in Twin Activate, is exported as a functional mock-up unit which can be implemented for each hydraulic cylinder in the multibody dynamics model.
Understanding the Model Definition in EDEM
Two bulk material models are built in Altair EDEM. One model uses a coal bulk material and the second uses an iron ore bulk material.
- Geometry that interacts with the bulk material is imported into EDEM by creating the DEM system in MotionView.
- A factory is created to produce 60,000 particles.
- Material properties are specified for the equipment and environment.
- Density
- Young’s Modulus/Shear Modulus
- Poisson’s Ratio
- Coefficient of restitution
- Coefficient of static friction
- Coefficient of rolling friction
- Material properties listed below are specified for the bulk material. However, a material wizard and database, GEMM, can simplify the material definition process by requiring the identification of a few key, often easy to find material properties.
- Bulk density
- Young’s Modulus/Shear Modulus
- Poisson’s Ratio
- Coefficient of restitution
- Coefficient of static friction
- Coefficient of rolling friction
- Particle shape
- Particle size and size distribution
- A Hertz-Mindlin contact model accurately and efficiently calculates the forces between particles.
Pre-Requisite
SOFTWARE REQUIREMENTS
All software must be from 2024 or newer.
MotionView – Multibody Dynamics Pre-Processor
MotionSolve – Multibody Dynamics Solver
Twin Activate – Hydraulics Model
EDEM – Bulk Material Model
MODEL FILES
Excavator.zip (See Attachments)
Usage/Installation Instructions
MODEL SETUP & SIMULATION STEPS
- Open Excavator.mdl in MotionView.
- Open EDEM_IronOre.dem or EDEM_Coal.dem in EDEM.
- Change the model length units to mm. Tools > Setting > Units
- Turn on the coupling server in EDEM.
- Run the analysis in MotionView to begin the co-simulation.
- Analyzing the results.
- Open a HyperView client in HyperWorks.
- Open the h3d created in the output directory to review the MBD model results.
- Load in and overlay the dem results to show the particle interactions with the MBD model.
Post-Requisite
RESULTS
The excavator performs a full scoop and dump cycle in two bulk materials: coal and iron ore. Coal has a low bulk density while iron ore has a high bulk density which increases the stresses when excavating and carrying the ore. The stresses increase significantly from 320 MPa to 500 MPa for a tripling in bulk density. Forces can be extracted to perform fatigue analysis on the excavator components in FEA software such as HyperMesh.
Excavator Scoop & Dump Cycle with Coal
Excavator Scoop & Dump Cycle with Iron Ore
Excavator Stresses Scooping Coal
Excavator Stresses Scooping Iron Ore
Excavator Arm Stress Hotspots
The forces produced by the hydraulic functional mock-up unit can be exported to HyperGraph. The hydraulics require up to 800 kN of force to produce the motion seen in the animation while excavating iron ore. Coal decreases the force requirement to under 600 kN. As expected, the actuators require the most force during the scooping operation with the arm actuator requiring the greatest increase in force.
ANALYSIS WITHOUT EDEM
One drawback of using EDEM for accurate excavation forces is long run times. A model with enough particles for an excavator to scoop and dump can increase runtimes by up to two orders of magnitude. To avoid this, it can be beneficial to directly apply forces to the bucket to represent forces created by digging and carrying the bulk material. Forces can be estimated with hand calculations, measured from a test with a physical excavator, or collected from a previous analysis using EDEM. Using forces from hand calculations or past test data can be particularly effective for early model development or design exploration. The results for the rest of the system will closely match an analysis using EDEM. Hydraulic actuator forces and boom arm stresses will be as accurate as the forces applied to the bucket.
As an example, we will use the forces from the above analysis with EDEM. Prior to running the EDEM model, we created a force output on the bucket body. After running the analysis with EDEM, we plotted the forces and moments in HyperView and exported the curves to a csv file. In MotionView, we created curve entities for each component of the force and moment on the bucket. We imported the csv data for each curve. Then we created a force with both translational and rotational components, and we applied the curves to their respective directions. Running the analysis produces results that closely match those from a simulation with EDEM. EDEM can be an extremely valuable tool for predicting excavation forces, however, a simpler approach can save time while producing accurate results.
CONCLUSION
In this example, we built a model of an excavator to understand the system’s dynamic response and required hydraulic forces. The co-simulation utilized an MBD model, functional mock-up unit for hydraulic calculations, and a bulk material model. The digital twin of the excavator can be used to test design changes or validate the current design before beginning manufacturing to save time and cut costs.
AUTHORS
John Dagg, Systems Engineering Intern
Christopher Fadanelli, Solutions Engineer – Systems Integration
Ananth Kamath Kota, Global Technical Manager – Systems Integration