What’s new in Altair OptiStruct 2021 and 2021.1?
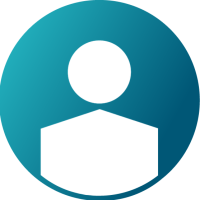

Continuing to build on more than 25 years of innovation, Altair OptiStruct™ is used globally by industry-leading companies to drive design with optimization and validate structural performance.
The latest release of Altair OptiStruct™ - Altair's optimization-enabled structural analysis tool - now offers extensive capabilities for aeroelasticity, adds more linear and nonlinear solutions for heat transfer, and expands on its nonlinear dynamic analysis (implicit and explicit solution) for composites and isotropic materials.
In this post we are highlighting aeroelasticity, heat transfer and composite capabilities.
OptiStruct in a nutshell
OptiStruct solves both linear and nonlinear problems across static and dynamic, vibrations, acoustics, fatigue, heat transfer, and multiphysics disciplines. With its topology optimization driving lightweight, structurally efficient product design today, OptiStruct also offers many other structural optimization methods, along with a broad range of essential manufacturing constraints for traditional processes, composites, and additive manufacturing.
New to OptiStruct? Find out more here: https://www.altair.com/optistruct-applications/
Join the OptiStruct Community https://community.altair.com/community?sys_id=0204add61b9d0c50a028542d1e4bcb9a&view=sp&id=community_topic&table=sn_communities_topic#products
Aeroelasticity
Why is understanding aeroelasticity important?
Whether you are on land or in the air, getting it wrong leads to a bumpy ride at best and an expensive catastrophic failure at worst!
From bridges, buildings, chimneys, and powerlines to control surfaces on high-performance vehicles, and anything that flies, any structure that sits in a moving airflow needs to be assessed for aeroelastic effects.
The drive to minimize weight means that aircraft are becoming more flexible and susceptible to aeroelastic phenomena like “flutter” and “divergence” and “trim”, and control reversal. Given the importance of getting it wrong, starting at the concept stage a significant effort is placed on aeroelastic analysis throughout design-development, into post-design and aircraft certification.
Developed in response to our aerospace customer needs, OptiStruct now offers the aero industry a standard aeroelasticity solution by integrating a NASTRAN-compatible approach and input data. In doing so, Altair provides a complete solution within Altair Simulation with pre- and post-processing wrapped around OptiStruct a single, powerful optimization solver having multiphysics capabilities. This now means that in-house customer-developed optimization codes, regularly used to augment NASTRAN, are no longer needed, and avoids incompatibilities or coding errors.
Interfaced with HyperWorks, aeroelasticity problems can be set-up and explored using the User Guide and tutorials.
- Static aeroelasticity, assumes a new equilibrium is reached immediately. Quasi-steady state aerodynamics deals with aerodynamic load distributions, structural deformations and loads, effectiveness of control, surfaces, elastic aerodynamic coefficients, divergence (stability).
Trim analysis, OptiStruct computes the position of the control surfaces to meet the given constraints, along with all the displacements and other results supported by static structural analysis.
- Dynamic aeroelasticity, where unsteady aerodynamics where aerodynamic loads build with time: Gust response, like an OptiStruct modal-FRF with additional aeroelastic loads and the excitation (gust); Flutter, a system instability comprising a self-excited vibration that leads to the structure extracting energy for the airstream. Flutter analyses usually track modal damping and frequency, against velocity (vg plots).
An aeroelastic model comprises the aerodynamic model, structural model, and the spline (interpretation between models), with each subcase defining the flight, maneuver, and gust conditions. The same model is used for computing trim, stability, flutter, dynamic loads…
A current status of OptiStruct aeroelastic capabilities can be summed up as:
- Aerodynamic module: computation of aerodynamic matrices needed for all the solution sequences.
- Spline module: computation of the matrix for mesh interpolation for all the solution sequences.
- Static solver and divergence: static aeroelastic analysis (SOL144)
- Flutter: flutter analysis (SOL145)
- Static aeroelasticity, for wind tunnel and clamped models.
- Static aeroelasticity, trim for aircraft in flight
- Define control surfaces
- Define engine meshes
- Flutter, K and KE methods; PK and PKNL methods
Heat transfer
In all aspects of our daily lives, we benefit from the heat transfer mechanisms – conduction, convection, and radiation. It helps heat our homes, cools our drinks, and cooks our food. For product design, understanding thermo-structural performance enables optimal design of cooling systems to guarantee product reliability. It assures our vehicle’s engine does not seize, our brakes don’t fade, and our EV vehicle batteries or laptops don’t overheat and fail.
OptiStruct now supports conduction, free convection, forced convection (linear steady-state) and radiation. Material thermal properties are added to material cards for isotropic, anisotropic, and temperature-dependent materials (nonlinear problems). In real-life parts, thermal contacts between mixed materials are common and their understanding are key to accurate simulations. For thermal loading, heat flux either general or directional, and a volumetric heat generation are supported, along with boundary conditions of imposed temperature, free convection via a surface, and radiation.
Heat transfer solutions include:
- Steady state heat transfer, where the temperature difference driving the heat transfer is constant with time.
- Transient heat transfer, where heat transfer occurs within in time period. Temperature field change over time to a new equilibrium and new thermal conditions.
- Transient loadings, where time dependent loadings and boundary conditions can be combined and used in a load step.
- Nonlinear thermal analysis, comprising both nonlinear steady state and transient, where nonlinearities maybe material properties, radiation (always nonlinear), or user-defined terms. From 2021, the MUMPS solver is now default.
- Sequentially coupled thermal structural solutions, where the temperature result from heat transfer is applied on the subsequent structural analysis as a load. This is an automated coupling in the solver for steady state or transient with a multi-step temperature history.
- Contact based thermo-structural analysis, a fully coupled solution, which currently supports steady state heat transfer and nonlinear small displacements analysis, to understand changes in contacting surfaces.
- User defined heat transfer subroutines
- Thermal Fluid Structural Interactions (TFSI), using fully integrated OptiStruct, handling transient heat transfer in structure domain, with AcuSolve for transient fluid heat transfer in fluid domain.
- Thermal optimization, supported for linear steady state heat transfer by conduction and convection providing thermal compliance and temperatures for all optimizations methods (topology, topography, size, shape, free shape ...) and OSTTS structural optimization with loadings from heat transfer. SimLab mapping function for temperature inputs to OptiStruct.
- Forced convection (Darcy flow), supported for linear steady state heat transfer analysis; topology optimization with convection cooling in conjunction with structural steady-state heat transfer.
Composites
Transverse shear stress distribution
When modeling a multi-layer laminate having a single element in the thickness direction, the transverse shear stress distribution can be derived from transverse shear forces and membrane strains. There is also a similar approach as for shells for shear stresses (using the ply coordinate system) for the material system for shells whereas shear stresses vanish at surfaces.
Interlaminar shear failure check
The interface shear stress allowable is compared to both out-of-plane shear stress components in the ply system and the more critical direction to determine the Interlaminar Shear Failure Index.
At ply level, the 3D stress criterion basically does the same thing but makes it possible to use different values in different directions (a recommended approach).
Thermal bending & distortion
When it comes to composites processing, temperature changes during the manufacturing cycle can have a significant effect on the residual stress distribution within the material without considering thermal bending and extension-bending coupling with constant through the thickness ΔT.
Note: This approach is applicable in conjunction with HyperSizer, which operates with matrices and related thermal coefficients.
Failure criteria
Building on the 8 failure criteria already available in OptiStruct, the latest release includes:
- TSAI failure criteria: coupling coefficients need to meet certain criteria and can be defined directly or computed or set to zero.
- Coupling coefficients.
- Maximum Stress criterion: supported for shell elements, where the ratios of the actual stresses to the failure stresses are compared in the ply principal coordinate system.
- PUCK3D: now consistent with Altair ESAComp theory for matrix failure calculation and in the fiber direction. Resulting in failure index for fiber tension/compression, matrix tension/compression and failure angle.
Explicit dynamic analysis
Today, all aspects of the transport industry, aiming to lightweight with composites to hit stringent targets, rely on efficient modelling and simulation tools to predict the correct energy absorption under impact, crash, and collision. Here, critical energy absorption occurs in a very short time, and exhibit very complex deformation responses, so accurate simulations use explicit dynamic finite element solvers. Of particular interest are discontinuities in strain to determine accurate stress and intralaminar damage predictions, along with discontinuities in displacements to understand delamination crack growth
OptiStruct Explicit is a solver for short, millisecond-type duration dynamic analyses. An important feature is that the input data for explicit solution is the same as for implicit solution. Also, the output data structure is the same. It supports composite properties: composite strains and stresses; parabolic out-of-plane shear stress, along with SMP and MPI (DDM) parallelization.
Recent enhanced and new capabilities for the explicit dynamic analysis of composites include:
- Drape table: to define scaling factors and rotation angles for elements of a ply.
- Out-of-plane shear stress: now provides different options for shell element (constant; parabolic for nonlinear explicit).
- Strength ratio: a measure of the margin to onset of failure, includes: composite strength (ply or bond failure); ply-based TSAI; envelope of criteria.
These capabilities are expanding to include failure onset and progressive damage.
Some examples of use cases include the response of a structure due to low velocity impacts assuming linear elastic material behavior. Various dynamic stability analyses for thin-walled structures. Geometric non-linearity is automatically included.
The analysis type and termination time are specified in the Load Step. Time step is automatically determined and can be reduced if severe element distortion occurs.
View release notes and download from Altair One https://marketplace.altairone.com/Marketplace?app=OptiStruct