What's New in EDEM 2024.1 – Release Highlights
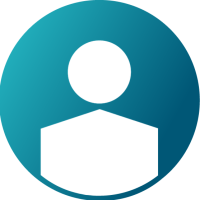

Altair® EDEM™ is available on Altair One and continues to prove its market leadership by setting the industry standard for the Discrete Element Method (DEM). Now more powerful and easier to use than ever - EDEM 2024.1 sees the addition of concave polyhedral particles enabling users to reproduce more complex physics when needed. On top of that, a new particle boundary condition allows for a simplified simulation set up. Finally, EDEM's unique powders database has been expanded by now including 15,000 new material models calibrated against the FT4 rheometer basic flowability energy measurement.
Here are some more details of the key highlights from this latest release!
Simulate All Polyhedral Particle Shapes
EDEM can now simulate all polyhedral particle shapes with the addition of concave polyhedral particles. This is another significant milestone for EDEM with the introduction of full support for concave shapes - all polyhedral particle shapes are fully supported and can be deployed in simulations alongside convex polyhedral, multi-sphere and sphero-cylinder particles. Particle shapes can be imported as CAD or pre-defined meshes (STL, OBJ, etc.) and must form a single closed volume, but no additional steps are required from the user.
![]() | ![]() |
Previously, there were applications where a more complex shape was required to accurately reproduce the interaction behavior with the equipment or process being simulated, and this was limited to only convex polyhedral shapes – now users have the choice to simulate a wider range of shapes on GPU where several advanced simulations can be achieved with complex shapes.
Example: food processing mixer simulating the seasoning of potato chips
Utilizing EDEM’s intra-particle coating analysis capabilities, concave shapes such as “potato chips” can be simulated to optimize the appropriate distribution of the coating seasoning on the surface to improve end-product quality.
The main characteristic of this new capability is the unparalleled performance achieved! As an example of this, a 1 million particle simulation using a mid-range GPU (Nvidia Titan RTX) only requires 8.4GB of memory and less than 8 hours to run.
Simplified Workflow for Particle Kinematics
A new boundary condition (Rigid Link) to assign the velocity from a geometry section to a specified group of particles has been added for a simplified simulation set up. The Rigid Link condition can be applied when the particle is created, on contact with a specific geometry section, or at a pre-defined time.
This capability is ideal for attaching fibers, roots, brushes, etc to a moving or static geometry section. For example, when applying kinematics over particles for fixing brushes to a vehicle and transferring the geometry properties to the particle, like the street sweeper example shown here, or, for example in agriculture, when fixing crops to the ground / grasses to soil beds or fixing an electrode to the material bed for battery calendering.
Example: simulation of a street sweeper collecting material
Assigning kinematics to particles has been difficult and this capability will enable more flexibility when users require to assign movement to particles. Rigid link is not only easier to set-up; it is also cheaper to run.
Expanding the World First Powder Database
![]() | ![]() |
To further expand calibrated options for our unique Powders Database, users can now select from 15,000 AI generated material models, calibrated against the popular FT4 rheometer basic flowability energy measurement (by Freeman Technology Ltd) to gain a better match for their powder calibration and hence solve complex powder processing problems. This capability eliminates manual calibration of powders and leads to a much better understanding of powder characterization and the behavior of powders for advanced applications. |
What else?
Beyond these new capabilities and improvements, this release also brings some other important developments, including:
- Normal and lognormal distributions by Mass Fraction. This feature is designed to improve workflow when defining size distributions by mass. Previously the size distribution would have to be calculated externally to EDEM and then entered as a user-defined distribution, but now the distribution can be defined in the EDEM GUI.
- Export data in Analyst, now includes Variance and Standard Deviation as Queries Types for easier analysis, like mixing, and updated options to remove additional text in columns making easier to read and parse data with python scripts.
- EDEMpy updated to add better support for factories, EDEM API models and the format for setting parameters of physics models has been changed to be more consistent.
To find out more about what’s new in EDEM 2024.1, check out the release notes that are available on Altair Marketplace