Multiphysics Digital Twins at the System Level — How Leonardo Verified and Optimized Product Performance
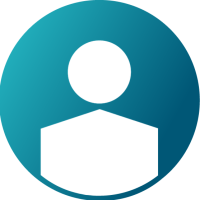
Multiphysics Digital Twins at the System Level — How Leonardo Verified and Optimized Product Performance
“The whole is greater than the sum of its parts.” When Aristotle gave us this wisdom some 2370 years ago, he was not thinking about digital twins for design and development of multiphysics products, most probably. Nonetheless, his idea summarizes in a very good way the challenges companies face when developing today’s smart, efficient, and resultingly complex products. With the goal of ensuring that products consisting of multiple subsystems and components work reliably despite a huge variability of boundary conditions, companies are constantly seeking out the most effective and efficient product optimization methods. Increasingly, the solutions companies are considering involve digital twins, but how are these beneficial?
To answer this question, we can start by defining digital twin as a virtual representation of an asset, bridging multidisciplinary simulation and real-world data to predict and optimize system outcomes. So far, so good. But can we more specifically understand where and how digital twins add value in the product development cycle?
By combining different technologies from physics-based simulation, via data analytics and artificial intelligence (AI), to leveraging high-performance computing (HPC), digital twins significantly reduce the need for physical prototype-based hardware testing through all stages of product design, development, and post-production operational performance optimization.
Next, we’ll have a closer look at an exemplary digital twin for design use-case featuring Leonardo, a global, high-technology company and top player in the aerospace, defense, and security industries.
The Challenge
One of Leonardo’s electronics-products is a mechatronic scan radar system that mounts under a helicopter inside a radome. A challenge with this design is antenna-transmission loss caused by in-flight vibration to the radome. To correct the issue and ensure reliable product performance, Leonardo needed a system-level approach that could identify and assess all contributing factors and conditions related to the transmission loss. Because physically measuring the radome deformation and tracking electromagnetic behavior during flight was impossible, Leonardo looked to a digital twin solution that could predict the antenna behavior and optimize the antenna design to meet mission requirements.
Our Solution
Based on the geometric information and boundary conditions for the antenna, Altair and Leonardo used a multiphysics approach to build a holistic digital twin of the antenna system and optimize the radome design. Covering multiple physical domains and simulation disciplines, the digital twin solution included these components:
- A 3D structural model with a flexible multibody motion system that predicted deformation from vibration impacting the antenna. Leonardo validated the model using test-bench sensor data that captured the antenna’s vibration.
- A 3D high-frequency electromagnetics model fed with deformed-shape data. The simulated model showed the effect of antenna-plate deformation on the radiation pattern.
- A reduced-order model (ROM) generated from a high-fidelity electromagnetic simulation. This AI-powered solution decreased simulation time while maintaining the needed accuracy.
- A 1D system simulation environment calculated key performance indicators of the antenna’s radiation pattern based on electromagnetic results using the antenna plate model’s nominal shape for control design.
- Dedicated 3D design and simulation tools with which engineers predicted material properties, minimized weight and intrusion impact such as bird-strike, and solved highly nonlinear problems involving the dynamic loadings of in-flight conditions.
Helicopter with simulation results of radome and electromagnetic pattern
The Benefits
By deploying Altair’s digital twin solution, Leonardo reduced its development costs significantly by optimizing its radar system antennas without the need for expensive prototypes. This strategy saved time as well as technical resources. By shifting optimization efforts to earlier stages of design development, also known as frontloading, Leonardo was able to shorten its development cycle as well as speed up time-to-market.
Optimized performance at the overall product level and streamlined workflows produced valuable insights into antenna radiation patterns, physics drivers, and best trade-offs among technical requirements early in development cycle where design changes are both easier to realize and less costly.
Last but not least, mitigating information silos slashed turnaround times. Through one unified ecosystem, a major benefit of Altair’s digital twin solution, all engineering teams — structural, electromagnetics, controls and even testing — could access the digital twin and collaborate, thereby enabling better and faster radome and antenna system evaluation and improvement.
To learn more about digital twin applications like this, join us for an upcoming webinar on Wed., July 10, 2024:
The Future
Altair provides the most comprehensive digital twin solutions, comprising best-in-class technologies that can be seamlessly integrated into established workflows. Beyond delivering software, Altair has domain experts at your service to help you achieve your goals more efficiently!
Comments
-
This is a cool example of using the results of a structural simulation in an electromagnetic simulation, and of the creation of a reduced-order model. Those concepts existed before the term Digital Twin was coined. It is not clear to me from this article how the concept "Digital Twin" differs from the modeling and simulation concepts that have been around for a while. What am I overlooking?
0 -
Martin Vogel_22355 said:
This is a cool example of using the results of a structural simulation in an electromagnetic simulation, and of the creation of a reduced-order model. Those concepts existed before the term Digital Twin was coined. It is not clear to me from this article how the concept "Digital Twin" differs from the modeling and simulation concepts that have been around for a while. What am I overlooking?
Thank you for your comment! I agree with you that the term Digital Twin is used more often and more broadly since a while. In our exchanges with customers we experience that a Digital Twin for Design, which might be very close to a multi-physics simulation, is resonating more. Not seldom such simulation-based approaches are a valid starting point on a journey towards more comprehensive and connected Digital Twins incl, bi-directional exchange of data between simulation and real sensors. This is also the case for Leonardo and I will share some more details during the corresponding webinar.
0