Managing Thermal constraints in power converter design
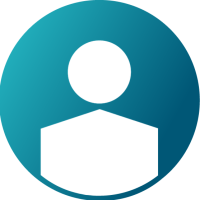

Power converters in electric vehicles, aerospace applications or renewable energy applications need to be able to transfer large amounts of power, while being compact and reliable. In motor drives for traction, this ever growing demand for high power densities also meets a very challenging thermal environment, because of integrated structures, with the inverter very close to the motor.
The thermal loading of power semi-conductor devices needs to be precisely managed and overheating should be avoided, as it is one of the main causes of failures. Selecting the right rating of components is then a critical aspect of the design, as well as an optimal sizing of the cooling systems, not to compromise the lifetime of the converters. High temperature gradients in the structure will also affect global performance of the power conversion and can be the cause of mechanical failures due to differential thermal expansions. The right balance must be found between reliability and performance on one side, versus cost and size on the other side.
In Altair PSIM simulation tool, you are able to consider a full motor drive, including the motor, the converter and its control. It means you can virtually test various conditions it will face. The behavior of each power device can be represented in an accurate way, by using dedicated models able to evaluate the power losses together with their internal temperature. You can then evaluate the impact of design variables on temperatures such as the type of components, the switching speed or the PWM patterns that are used and then predict potential thermal induced failures.
3D temperature distribution in a traction power converter
To complement this 1D view, 3D simulations can be added and combined with it, leading to an even more precise knowledge of the temperature distribution in the converter and the impact on performance. The power loss information of devices that are computed in PSIM and their dependency on temperature can be sent to SimLab -Electronics Thermal, which will perform the 3D analysis, in which the losses coming from the busbars can also be included. The simulation is also including the effect of the cooling system of the converter, using CFD. Such deep insight greatly helps to design the heatsinks and decide on key parameters like the flow rate of the coolant.
1D-3D coupling to get an accurate evaluation of losses and temperature map
This workflow is applicable to any type of power converter multi-kW and larger power converter that requires cooling. If you want to learn more about simulation results on this topic, please join our Accelerate E-NNOVATION webinar series on power electronics here.