Analysis and design of complex motor drive systems
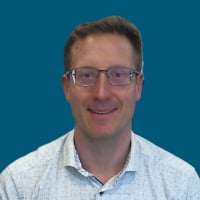

You need powerful tools for motor drive design, simulation, and analysis. Altair provides them. We achieve the fastest and most accurate simulations on the market that will make your work more efficient than ever.
Key challenges that engineers often face in motor drives include:
- Motor performance evaluation
- Controller design of current/speed feedback loops
- Sensored or Sensorless control, FOC/DTC
- Power converter major components dimensioning
- Inverter loss calculation and device comparison
- DC bus sizing and link capacitor sizing
- EMI filter evaluation
With our intuitive user interfaces, easy implementation, and outstanding technical support you’ll be up and running in no time.
Motor Performance Evaluation
You need to evaluate what sort of motor to use and what sort of design parameters it requires. Do you need the accuracy of an FEA tool or will our built-in models work?
PSIM provides the ability to simulated with a model generated by FluxMotor or Flux. You can also simulate with models from JMAG.
If the detail of an FEA model is not required, PSIM both provide a full library of motor models for you to use. Various types of linear and non-linear motor models covering the full spectrum of motors, everything of induction and PMSM through to switched reluctance and DC. Consult the full list of supported machine models here.
Make use of our powerful scripting tools to automate your simulations and analysis to help you work smarter not harder.
Learn More:
Webinar Drive Efficiency and Silence - How to Design High-Efficiency and Less Noisy Motor Drives
Webinar: Motor Drives with High-Frequency Interactions (53:19)
Tutorial: New Motor Models (3:26)
Motor Control Design
Designing controllers of a motor drive can be tricky due to the multi-loop structure and the non-linearity. With the Motor Control Design Suite PSIM will close the current and speed loops and give you a working motor drive simulation for you to work from. Our design suite implements Max Torque Per Amp Control, field weakening, max torque per volt control with proper operating limits for power & torque.
If you want to close the loops yourself or implement your own novel algorithms, PSIM both contain all the needed control library elements. You can even embed c code into the simulation to see how it performs.
You can also define your control structures with Activate or Embed and co-simulate with a PSIM model. If you still use Simulink for control design you can also co-simulate a motor drive in PSIM with the control components in Simulink.
Learn More:
Webinar Drive Efficiency and Silence - How to Design High-Efficiency and Less Noisy Motor Drives
Tutorial: The motor control design suite
Tutorial: Implementing Field Weakening & MTPA Control with PSIM (14:10)
Tutorial: How to Implement Field Oriented Control of PMSM with PSIM & SmartCtrl (18:00)
Tutorial: Co-simulation of Simulink and PSIM with SimCoupler (5:22)
Tutorial: Co-simulation with Activate
Sensorless Control
To help design sensorless control of a motor drive system, PSIM provides convenient tools for users to implement TI’s sensorless control algorithm InstaSPIN quickly. You can simulate the function of the algorithm and also perform embedded code generation for quick and easy hardware implementation.
If you don’t want to use InstaSPIN, all of the necessary library elements are provided, sliding mode observer (SMO), c code in simulation, etc. To allow you to quickly design and simulate your own sensorless algorithm.
Learn More:
Tutorial: InstaSPIN code generation – DRV8305 Quick Start | PMSM control (11:06)
Webinar: Using InstaSPIN for Sensorless PM Motor Drives (57:09)
Webinar: Design of Sensored and Sensorless Motor Drives with PSIM (49:18)
Power Hardware Design
The power stage of a motor drive has several key design decisions that will greatly impact system efficiency, heatsinking, electromagnetic interference (EMI), and the motor drive performance envelope.
Inverter loss calculation and comparison of different devices can be carried out easily. One can calculate the conduction and switching losses, and junction temperatures under different operating conditions and use a thermal equivalent circuit to model heatsinking requirements. This allows you to make critical design decisions like switching from IGBTs to SiC MOSFETS.
Easily compare the various inverter gating methods – such as SVPWM, DPWM, 6-pulse, etc. – for thermal/efficiency performance with motor drive performance.
Electromagnetic interference, EMI, is an extremely important design consideration as motor drives become more connected with other sensitive electronics. Easily evaluate and design filters with our EMI Design Suite.
Quickly and easily understand your DC link specifications like sizing and your DC bus capacitor and its ripple current rating.
Of course, all of these studies and comparisons can be automated with our powerful scripting tools.
Learn More:
Webinar: Virtual front loading for minimal conducted EMI
Webinar Drive Efficiency and Silence - How to Design High-Efficiency and Less Noisy Motor Drives
Webinar: Motor Drives with High-Frequency Interactions (53:19)