Error 312 during topology optimization
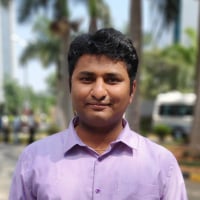

'I am an Hypermesh (Optistruct) user. An error (error 312) does not allow me to do a topology optimization. Where can I find some he lp to solve it?'
Answers
-
The 312 error while topology optimization can be due to a number of causes
• The definition of constraints is not proper
• If the constraints are not applied properly there will be rigid body modes from the analysis.• REexamine your desing constraints make sure there is material left to optimize.
• Rigid body modes due to elements not being connected properly – connectivity issues.
• Loads definition – are all the loads referenced correctly in the loadstep? Are there any unnecessary load collectors
• You may have to reformulate your problem to minimize compliance and put a constraint on volume fraction
• You can check the *.out file for more details regarding the error. the explanation for the error is provided in the *.out file.
0 -
Hi,
I think that the problem is that: 'Rigid body modes due to elements not being connected properly – connectivity issues.'
I have two solids, how can I connect them? I tried using contact surfaces without succes.
0 -
Hi adrian.vich
Can you paste an image of these two components? how are these two components connected in reality?
You can use connectors to connect them, HyperWorks Desktop Applications > HyperMesh > User's Guide:
ConnectorsConnectors are special entities mainly used to define which parts of a model have to be fastened to each other and how the connections have to be performed. Here the connectors can take into account the mechanical and structural conditions of the model.
One approach could be to calculate the weight of the kettle and apply a distributed load in the packaging just as there would be with the kettle. hence not modelling the kettle at all.
If it is weight alone you are concerned about how are you loading your model? are you concerned about more loads than just the packaging supporting the weight of the kettle?
You have to connect the two components. you can connect them by mesh it self i.e. the elements of both the components share nodes at the boundary.
You should be able to do this with contact surfaces, have a look at this tutorial here on how to model contacts in Optistruct, since the blocks are resting one on top of the other it looks quite relevant to your case.
Altair OptiStruct > OptiStruct Tutorials and Examples > Tutorials > Advanced Small Displacement Finite Element Analysis:
OS-1365: NLSTAT Analysis of Solid Blocks in Contact0