*** ERROR # 153 *** for thermal and nonlinear quasi static analysis combination
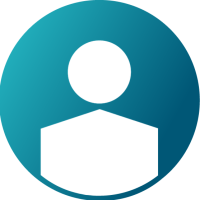
Hello,
In the scenario I created, two plates are torqued with screws. However, the temperatures of these plates are different.
In other words, I want heat transfer to occur during torqueing.
But I am getting the following error. I tried the suggestions but couldn't find a solution. Could you please help? Also, what KCHTC value would you recommend for freeze and slide contacts?
Thank you.
Best Regards,
Ovunc
*** ERROR # 153 ***
Exactly zero pivoting encountered during Numerical Factorization;
the model may have rigid body mode.
Solver error no. = -503
spc set id = -5
index = 1
Possible reasons are:
1) insufficiently constrained model,
2) having rigid body mechanisms within the model,
3) extremely ill-conditioned rigid element sets,
4) extremely thin shells (as used for skinning) that have MID2/MID3,
5) gap elements with extremely high stiffness (KA, especially KT or MU).
6) extremely high Poisson's ratio in hyperelasticity material definition.
Check the model and rerun the problem.
(MECHCHECK may be used to find the rigid body modes. To do so,
change the input to be an eigenvalue analysis and add MECHCHECK.)
(WARNING: results obtained with MECHCHECK cannot be used because
the model is changed internally.) This error was detected in subroutine bcsmtxfct.
==============================
Solver FAILED
optistruct:: Solver run finished.
Best Answer
-
looks like thermal model doesn't like rbe2 elements for conduction.
grid # component : comments
----------------------------------------------------------------------
237891 1 : has no conductivity but is referenced by MPC (*3)
237892 1 : has no conductivity but is referenced by MPC (*3)
----------------------------------------------------------------------
*3 : The d.o.f. belongs to an MPC set only (for your information).I've changed your bolt from 1D to 3D and i've elimated the RBE2, and it looks ok now.
But, i'm wondering if the steady state analysis will not smear the contact effects in your simulation.
Although conduction will be larger in the contact surroundings, i believe that because of the steady state, in a the long run, the temperatures will stabilize at the same level of a fully touching plate.
1
Answers
-
looks like thermal model doesn't like rbe2 elements for conduction.
grid # component : comments
----------------------------------------------------------------------
237891 1 : has no conductivity but is referenced by MPC (*3)
237892 1 : has no conductivity but is referenced by MPC (*3)
----------------------------------------------------------------------
*3 : The d.o.f. belongs to an MPC set only (for your information).I've changed your bolt from 1D to 3D and i've elimated the RBE2, and it looks ok now.
But, i'm wondering if the steady state analysis will not smear the contact effects in your simulation.
Although conduction will be larger in the contact surroundings, i believe that because of the steady state, in a the long run, the temperatures will stabilize at the same level of a fully touching plate.
1 -
Adriano A. Koga_21884 said:
looks like thermal model doesn't like rbe2 elements for conduction.
grid # component : comments
----------------------------------------------------------------------
237891 1 : has no conductivity but is referenced by MPC (*3)
237892 1 : has no conductivity but is referenced by MPC (*3)
----------------------------------------------------------------------
*3 : The d.o.f. belongs to an MPC set only (for your information).I've changed your bolt from 1D to 3D and i've elimated the RBE2, and it looks ok now.
But, i'm wondering if the steady state analysis will not smear the contact effects in your simulation.
Although conduction will be larger in the contact surroundings, i believe that because of the steady state, in a the long run, the temperatures will stabilize at the same level of a fully touching plate.
Hi @Adriano A. Koga ,
Thank you very much.
- All the component seem to be gathered in a single component (misc1). What could this be due to?
- Sorry, I didn't understand what you mean below. Could you please explain a little bit?
- "But, i'm wondering if the steady state analysis will not smear the contact effects in your simulation."
- I have a more complex model normally. But I don't have the data for clearance and pressure based thermal conductance . That's why I can't use TCID and TPID. I decided to use KCHTC. But what should its magnitude be?
- Does the MU1=0,1 value represent the slide contact option that the contact property is not specified? Or, should it be another value?
Thank you.
Best regards,
Ovunc
Ovunc2 said:Hi @Adriano A. Koga ,
Thank you very much.
- All the component seem to be gathered in a single component (misc1). What could this be due to?
- Sorry, I didn't understand what you mean below. Could you please explain a little bit?
- "But, i'm wondering if the steady state analysis will not smear the contact effects in your simulation."
I have a more complex model normally. But I don't have the data for clearance and pressure based thermal conductance . That's why I can't use TCID and TPID. I decided to use KCHTC. But what should its magnitude be? Does the MU1=0,1 value represent the slide contact option that the contact property is not specified? Or, should it be another value? Thank you.
Best regards,
Ovunc
I have no clue on why there's this misc component in your HW.
Concerning the steady state, what i meant is that becasue steady state is the result of "an infinite/long time heat trasnfer" it might mask the differences between a small conductance area due to contact, or a large area. Maybe i'm wrong. I was just wondering.
KCHTC i understand that is realted to the direct conductive coefficient of your materials. Maybe because you might have different materials it might be some average, i assume.
Sorry, i missed the MU part. As long as I know it is only relevant to your "mechanical" contact. I didn't change this, as far as I remember.
Adriano A. Koga_21884 said:I have no clue on why there's this misc component in your HW.
Concerning the steady state, what i meant is that becasue steady state is the result of "an infinite/long time heat trasnfer" it might mask the differences between a small conductance area due to contact, or a large area. Maybe i'm wrong. I was just wondering.
KCHTC i understand that is realted to the direct conductive coefficient of your materials. Maybe because you might have different materials it might be some average, i assume.
Sorry, i missed the MU part. As long as I know it is only relevant to your "mechanical" contact. I didn't change this, as far as I remember.
Hi Adriano,
Thank you for your comments. It is very useful for me.
It is true that you did not change the MU part. While I was examining the model, it came to my mind and I was curious about your opinion.
Thank you very much.
Best Regards,
Ovunc