Reading the reaction force from the independent node for an RBE2 / RBODY element
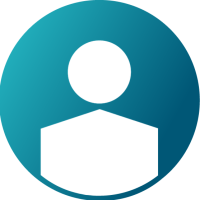
Hi,
I want to rotate a simple geometry around the axis passing through the center of gravity and calculate the required moment. I also compare the value I calculate analytically with the value I calculate numerically. For this, I used x and y elements and read the moments of reaction from the independent node of these elements. But in the scenarios below, I got different results.
In all scenarios, the coordinate of the independent node of the rigid element is (0,0,0). The rigid element’ s degree of freedom is limited only in ZZ (only number 6 has a tick).
- Scenario
All nodes on component were selected as independent nodes. In this case, no solution took place.
- Scenario
All but one node on the component are selected as independent nodes. RBE2 element used. In this case, the energy error was -99,9 %. So I didn’t expect it to give an accurate result. However, oscillation in the graph of reaction moment was quite low.
- Scenario
16 random nodes were selected as independent nodes. RBE2 element used. In this case, the energy error was -6,6% . I’ve observed quite a lot of oscillation. The mean value of graph was close to the analytical solution.
- Scenario
All but one node on the component are selected as independent nodes. RBODY element used. In this case, the energy error was 0,0%. Oscillation in the graph of reaction moment was quite low. But when I looked at the mean value of the results, I could not get a value close to the analytical results. I don’ t know if it was by chance, but it was about half the analytical value.
- Scenario
16 random nodes were selected as independent nodes. RBODY element used. In this case, the energy error was 0,0%. I’ve observed quite a lot of oscillation and the mean value of graph was close to Scenario 4.
When I move the piece linearly, I could get the numerical values and the analytical values the same for the reaction force. Also, when I use shell element, I can get the same result. Why is the problem I mentioned above? I want to get the solution as close to analytical value as possible, with minimal oscillation and energy error.
I added model and the table with the summary of the scenarios . I request your helps.
Thank you.
Best regards,
Best Answer
-
Hi, there are a few things going on here, small test models are often the most complex when you start looking in detail!
For the 'fully rigid' runs, the reason you didn't get a result is that the timestep is then very large, the natural timestep is bigger than your runtime, hence no result.. the job finished before it started .so you need to use /DTIX to force it down to get a solution.
RBE2 won't give sensible answers since it just rigidises the node group, the inertias are not converted from the slave nodes considering the nodal locations (XX,YY,ZZ will be equal, so no good for your use case), so use RBODY.
Having some of your 'wheel' deformable will always result in oscillation since then the 'non' rigid nodes are in an elastic system where they are being accelerated by the neighbouring elements.
You won't get a 'sensible' value by extracting the REACZZ from the node where you are applying the imposed velocity, the REAC outputs only work where the node in question is constrained in a /BCS against that DOF, (e.g. X,Y,Z for a grounded node) in this case the node where you are doing the extraction is the one where you are applying the rotation.
In the attached, I have modified your model in following ways:
RBODY expanded to cover all nodes
DTIX set to 1e-6
Extra node is added to the RBODY in the axis of the axis of rotation
To that extra slave is attached a stiff spring acting as a transducer to measure the applied torque (damping and inertia set for spring to maintain sensible timestep while bringing it to equilibrium relatively quickly while not themselves influencing the moment too much)
The IMPVEL is moved to the other end of the spring (i.e. the impvel is applied to the wheel via this spring beam)
TH request for MOMENTX for the spring (MOMENTX rather than MOMENTZ since it is in spring system, X being along the axis)
The output of the spring is below, after some initial oscillation it settles out at a steady 14701.5Nmm
2
Answers
-
Hi, there are a few things going on here, small test models are often the most complex when you start looking in detail!
For the 'fully rigid' runs, the reason you didn't get a result is that the timestep is then very large, the natural timestep is bigger than your runtime, hence no result.. the job finished before it started .so you need to use /DTIX to force it down to get a solution.
RBE2 won't give sensible answers since it just rigidises the node group, the inertias are not converted from the slave nodes considering the nodal locations (XX,YY,ZZ will be equal, so no good for your use case), so use RBODY.
Having some of your 'wheel' deformable will always result in oscillation since then the 'non' rigid nodes are in an elastic system where they are being accelerated by the neighbouring elements.
You won't get a 'sensible' value by extracting the REACZZ from the node where you are applying the imposed velocity, the REAC outputs only work where the node in question is constrained in a /BCS against that DOF, (e.g. X,Y,Z for a grounded node) in this case the node where you are doing the extraction is the one where you are applying the rotation.
In the attached, I have modified your model in following ways:
RBODY expanded to cover all nodes
DTIX set to 1e-6
Extra node is added to the RBODY in the axis of the axis of rotation
To that extra slave is attached a stiff spring acting as a transducer to measure the applied torque (damping and inertia set for spring to maintain sensible timestep while bringing it to equilibrium relatively quickly while not themselves influencing the moment too much)
The IMPVEL is moved to the other end of the spring (i.e. the impvel is applied to the wheel via this spring beam)
TH request for MOMENTX for the spring (MOMENTX rather than MOMENTZ since it is in spring system, X being along the axis)
The output of the spring is below, after some initial oscillation it settles out at a steady 14701.5Nmm
2 -
Paul Sharp_21301 said:
Hi, there are a few things going on here, small test models are often the most complex when you start looking in detail!
For the 'fully rigid' runs, the reason you didn't get a result is that the timestep is then very large, the natural timestep is bigger than your runtime, hence no result.. the job finished before it started .so you need to use /DTIX to force it down to get a solution.
RBE2 won't give sensible answers since it just rigidises the node group, the inertias are not converted from the slave nodes considering the nodal locations (XX,YY,ZZ will be equal, so no good for your use case), so use RBODY.
Having some of your 'wheel' deformable will always result in oscillation since then the 'non' rigid nodes are in an elastic system where they are being accelerated by the neighbouring elements.
You won't get a 'sensible' value by extracting the REACZZ from the node where you are applying the imposed velocity, the REAC outputs only work where the node in question is constrained in a /BCS against that DOF, (e.g. X,Y,Z for a grounded node) in this case the node where you are doing the extraction is the one where you are applying the rotation.
In the attached, I have modified your model in following ways:
RBODY expanded to cover all nodes
DTIX set to 1e-6
Extra node is added to the RBODY in the axis of the axis of rotation
To that extra slave is attached a stiff spring acting as a transducer to measure the applied torque (damping and inertia set for spring to maintain sensible timestep while bringing it to equilibrium relatively quickly while not themselves influencing the moment too much)
The IMPVEL is moved to the other end of the spring (i.e. the impvel is applied to the wheel via this spring beam)
TH request for MOMENTX for the spring (MOMENTX rather than MOMENTZ since it is in spring system, X being along the axis)
The output of the spring is below, after some initial oscillation it settles out at a steady 14701.5Nmm
Hi @Paul Sharp,
You provided valuable and useful informations.
Thank you so much.
Best Regards,
0