Meshing recommendations for elements reaching zero or negative volume during simulation
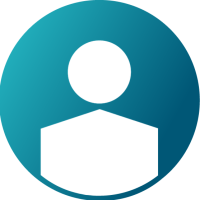
Hello everyone, I'm attempting to complete a crash simulation of a bicycle helmet strapped to a rigid dummy head hitting a rigid wall with Radioss 2021. Shortly after initial contact, the foam liner apparently gets compressed too much so that a number of elements reach zero or negative volume as stated in the output file, after which the solver aborts the run. The foam liner is meshed with 3mm linear tetrahedra, whereas the shell is meshed with 3mm linear trias. For initial testing purposes, the foam is represented by a LAW36 tabulated plastic material law and the shell by an elastic LAW2 model. The property settings are mostly according to the recommendations from the Radioss introductory training documents. Please advise on meshing strategies such that their shape remains fit for calculation even under large compression. Would, for example, a size increase in the radial direction lead to convergence? I aim to retry the model with second order tetras, but haven't gotten a chance to do so yet. Unfortunately, I cannot share the model or images of it due to an NDA.
Answers
-
Hi,
Sometimes with soft material, solid elements can be deformed severely that their nodes go through the opposite side and cause a negative volume.
'ZERO OR NEGATIVE VOLUME' warning happens when solid elements are very deformed and their characteristic length goes to 0. For large strain formulation, the time step of an element goes to 0 when the element is compressed.
In RADIOSS Starter input file (Runname_0000.rad), use Ismstr =2 in the solid property, and in RADIOSS Engine file (Runname_0001.rad) use the option/DT/BRICK/CST which will set the time step value tmin at which the solid elements will switch to small strain. (/DT/BRICK/CST option is used to control the time step of the analysis. The time step becomes constant after reaching Tmin specified by the user )
It is recommended to use IHKT = 2 with HEPH and Lagrange type total strain, Ismstr = 10 for foam or rubber materials (laws 38, 42, 69, and 82).
For more details refer to Free eBook: Introduction to Explicit Analysis with Altair RADIOSS, where I also covered this topic:
https://altairuniversity.com/free-ebooks/free-ebook-crash-analysis-with-radioss-a-study-guide/
1 -
Simon Križnik said:
Hi,
Sometimes with soft material, solid elements can be deformed severely that their nodes go through the opposite side and cause a negative volume.
'ZERO OR NEGATIVE VOLUME' warning happens when solid elements are very deformed and their characteristic length goes to 0. For large strain formulation, the time step of an element goes to 0 when the element is compressed.
In RADIOSS Starter input file (Runname_0000.rad), use Ismstr =2 in the solid property, and in RADIOSS Engine file (Runname_0001.rad) use the option/DT/BRICK/CST which will set the time step value tmin at which the solid elements will switch to small strain. (/DT/BRICK/CST option is used to control the time step of the analysis. The time step becomes constant after reaching Tmin specified by the user )
It is recommended to use IHKT = 2 with HEPH and Lagrange type total strain, Ismstr = 10 for foam or rubber materials (laws 38, 42, 69, and 82).
For more details refer to Free eBook: Introduction to Explicit Analysis with Altair RADIOSS, where I also covered this topic:
https://altairuniversity.com/free-ebooks/free-ebook-crash-analysis-with-radioss-a-study-guide/
Thank you for the pointers, I'll be sure to review everything.
0