MAT LAW 2 (PLAS_JOHNS) RADIOSS-calculated a, b, n parameters to plot plastic region curve
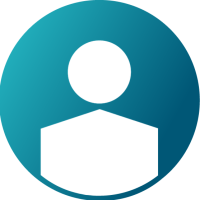
Hello,
I have been trying to select an appropriate material card for a material with the following properties:
E = 42.576 x 10^6 Pa
nu = 0.3
rho = 2650 kg/m^3
yield strength = 221 x 10^6 Pa
The material fails at an engineering stress of 418.9 x 10^6 Pa and an engineering strain of 0.00391.
I had originally tried using MAT LAW 2 (PLAS_JOHNS) with Iflag =1 for inputs of yield stress, UTS (engineering), and strain at UTS, but when I plot the function "stress = a + b*strain^n" (from RADIOSS reference guide 2020, p446) using the a, b, & n values calculated by RADIOSS, I don't get the expected stress-strain curve in the plastic region (first photo attached; a = yield, b = 276260135, n = 0.0779; orange line elastic region, blue line plastic region, solid black lines used for marking key points in material deformation behavior (yield and failure)).
I'm then just looking for some help answering the following:
(a) Why wouldn't the a, b, n values given create a plastic region curve that lines up with the end of the elastic region (expected curve is green sketch line in second attached photo)? Perhaps I've entered a value incorrectly?
(b) Since this material has distinct elastic and plastic regions, but fails before an actual reduction in stress on an engineering stress-strain curve (i.e UTS is the same as failure stress), is there a better material card to be using that would work with solid/brick elements and the known material parameters that I have? (I thought maybe MAT LAW 27, but this only work with shells)
Thanks in advance. Please let me know if I can provide any clarification to help with an answer to my questions/confusion.
Answers
-
Hi
The ultimate strength is the maximum stress achieved on the material. it is not the rupture stress.
Regards
0 -
Rogerio Nakano_21179 said:
Hi
The ultimate strength is the maximum stress achieved on the material. it is not the rupture stress.
Regards
Correct, and for this material, the maximum stress achieved is the same as the failure stress (i.e. there is no peak stress followed by a decline in stress prior to failure (on engineering stress-strain curve)). This value - the maximum stress - is what I've input in the material card for RADIOSS to calculate the given a, b, and n parameter values.
I am then still confused about why the a, b, and n values calculated by RADIOSS don't result in a plastic region curve that lines up with the end of the elastic region (photos attached in original question).
Is there a better material card to be using for a brick/solid element that undergoes elastic-plastic deformation, but does not have a peak in stress followed by a decline prior to fracture (when looking at the engineering stress-strain plot, not a true stress-strain plot)?
0 -
is the Young modulus 42.576MPa (seems too low, lower than yield strength) or 42,576.00MPa?
Regards
0 -
Rogerio Nakano_21179 said:
is the Young modulus 42.576MPa (seems too low, lower than yield strength) or 42,576.00MPa?
Regards
This is a typo in my original post, but the Young's modulus is correct in the HyperMesh/RADIOSS files: E = 42.576 x 10^9 Pa (i.e. 42,576.00 MPa)
0 -
Hi,
The strain in "stress = a + b*strain^n" is true plastic strain. So the curve starts at 0.0 true plastic strain and the yield true stress. But the plot of the elastic region of the material is true stress versus total true strain.
The example, RD-E: 1100 Tensile Test, RD-E: 1101 Elasto-plastic Material Law Characterization, gives some more details.
MAT LAW 2 (PLAS_JOHNS) with Iflag =1 is a good way to approximate a stress strain curve when you only have some basic properties of the material. This is good for an initial analysis but for better results it is recommended to get tensile test data for the material.
Thanks,
Andy
1 -
Hi
Also, based on the input values of your material, I found the values
b=208.85E06
n=0.00822
that are the values calculated on the Starter run, using LAW2 and Iflag=1.
If you need to do hand calculation, you can use the attached information.
Regards
2 -
Hi,
This law represents an isotropic elastoplastic material using the Johnson-cook Material model. This model expresses material stress as a function of strain, strain rate, and temperature. A built-in failure criterion based on the maximum plastic strain is available.
The material constants are A, B, n, C and m.
A is the yield stress of the material under referance conditions, B is the strain hardening constant, N is the strain hardening coefficent, C is the strenghthing coeffient of strain rate, and M is the thermal softening coefficent.Regards,
Dhanasharee Jadhav
0