Non-Linear static analysis
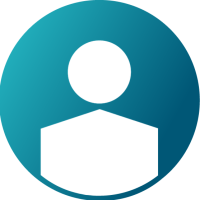
I am doing a NL-Static analysis of an assembly (check the image). I have following questions:
1. A cabinet is fastened at the 4 locations (in the front) and it is rested on the 2 wedges below. The force induced by the cabinet is 1500N.
- The question is, should I consider RBE2 at only 4 locations where the cabinet is fastened? or should I consider the 2 wedges below along with the 4 holes to define the RBE2 (like in the Image) ?
2. While meshing the holes, should I create washersplit?
3. After creating washersplits, should I consider them for defining RBEs ? or would it be fine if I just considered the holes?
- both in 2D and 3D simulations.
4. While defining RBE2, Should i let the solver compute the independent node location? or can i define the location of the independent node?
5. I converted the above assembly into a 2D Shell elements (all the components have a uniform thickness of 2mm) for the ease of calculation.
- Here, I used midsurface tool to generate the 2D Shell elements. In the properties, I considered 2mm as the shell thickness and ran the simulation but the results were different (the stresses and displacenents) in comparision to the 3D results. What could be the reason?
Answers
-
1. The question is, should I consider RBE2 at only 4 locations where the cabinet is fastened? or should I consider the 2 wedges below along with the 4 holes to define the RBE2 (like in the Image) ?
RBE2 will add numerical stiffness to your model, meaning that there will be no relative displacement regarding the connected parts. If the cabinet will hold some really rigid equipment, it is not so bad. But if your equipment is "flexible", then you should use RBE3 to distribute the load, without addding too much stiffness into your model.
Considering using the wedges or not, you have to consider what are the main load distribution regions of your real part. If the wedges are relevant on supporting the equipment, then, yes, you should also include the wedges;
2. While meshing the holes, should I create washersplit?It is always nice to have a washer represented, specially if you use RBE2 to connect the holes. the RBE2 will add artificial stiffness to your hole, and stresses will be zero where the RBE2 is connected, but a really high gradient will be present at the surrounding area. Usually we tend to disregard the first layer of elements, thus the washer would make it easier to isolate this singularities generated byu the RBE2.
3. After creating washersplits, should I consider them for defining RBEs ? or would it be fine if I just considered the holes?
- both in 2D and 3D simulations.It depends on your modeling procedure. The most important thing is to understand that the nodes connected via RBE2 elements and the first layer of elements will not have accurate stress values.
4. While defining RBE2, Should i let the solver compute the independent node location? or can i define the location of the independent node?If your mesh is quite uniform at the washer, leaving HyperMesh calculate the center node would be ok. If your mesh around the hole is not so uniform, then, it would be better to define yourself.
5. - Here, I used midsurface tool to generate the 2D Shell elements. In the properties, I considered 2mm as the shell thickness and ran the simulation but the results were different (the stresses and displacenents) in comparision to the 3D results. What could be the reason?
There are plenty of reasons. Type and refinement of the 3D model would be one of them. If you used tetra elements, the model is expected to be stiffer, and stress values not so accurate. You should really perform a mesh sensitivity/convergence study to get good results. (suggestion> run SimSolid directly on your CAD model to have a comparison). For a solid model of such a thin plate, you would need to have a really refined mesh to capture stress values, considering at least 3 elements along the thickness.
For stiffness, run a modal analysis first to compare both models.
Additionally, where are you computing stress values? at singularities? you should take care with stress values close to RBE2. Also, is your mesh refined enough at the hot spot areas?
0