I'm carrying out a rollover analysis where body is supposed to freefall just after coming in contact and rolling about its axis,
Only load on model is gravity, but as soon as the body the model come in contact the energy shoots to e+17
17500 0.1312 0.7500E-05 SHELL 226493 -2.3% 0.7811E+05 0.1039E+07 0.2618E+05 0.1169E+07 0.000
17600 0.1320 0.7500E-05 SHELL 226151 -2.5% 0.7547E+05 0.1050E+07 0.2665E+05 0.1181E+07 0.000
17700 0.1327 0.7500E-05 SHELL 392114 -2.7% 0.7298E+05 0.1062E+07 0.2717E+05 0.1194E+07 0.000
17800 0.1335 0.7500E-05 SHELL 392259 -2.9% 0.7066E+05 0.1072E+07 0.2775E+05 0.1206E+07 0.000
17900 0.1342 0.7500E-05 SHELL 222229 -3.2% 0.6848E+05 0.1083E+07 0.2839E+05 0.1219E+07 0.000
18000 0.1350 0.7500E-05 SHELL 456836 -3.5% 0.6644E+05 0.1092E+07 0.2908E+05 0.1231E+07 0.000
18100 0.1357 0.7500E-05 SHELL 441033 -3.8% 0.6458E+05 0.1102E+07 0.2984E+05 0.1244E+07 0.000
18200 0.1365 0.7500E-05 SHELL 456836 -4.1% 0.6306E+05 0.1111E+07 0.3073E+05 0.1256E+07 0.000
18300 0.1372 0.7500E-05 SHELL 197222 -4.4% 0.6201E+05 0.1118E+07 0.3180E+05 0.1268E+07 0.000
18400 0.1380 0.7500E-05 SHELL 451688 -4.7% 0.6153E+05 0.1126E+07 0.3309E+05 0.1281E+07 0.000
18500 0.1387 0.7500E-05 SHELL 451943 -5.0% 0.6162E+05 0.1132E+07 0.3461E+05 0.1293E+07 0.000
18600 0.1395 0.7500E-05 SHELL 439923 -5.2% 0.6224E+05 0.1138E+07 0.3633E+05 0.1305E+07 0.000
18700 0.1402 0.7500E-05 SHELL 933070 -5.4% 0.6322E+05 0.1145E+07 0.3822E+05 0.1317E+07 0.000
18800 0.1410 0.7500E-05 SHELL 436857 -5.5% 0.6439E+05 0.1151E+07 0.4018E+05 0.1328E+07 0.000
18900 0.1417 0.7500E-05 SHELL 439923 -5.6% 0.6561E+05 0.1157E+07 0.4219E+05 0.1340E+07 0.000
19000 0.1425 0.7500E-05 SHELL 440756 -5.6% 0.6672E+05 0.1164E+07 0.4431E+05 0.1351E+07 0.000
19100 0.1432 0.7500E-05 SHELL 433969 -5.6% 0.6767E+05 0.1171E+07 0.4661E+05 0.1361E+07 0.000
19200 0.1440 0.7500E-05 SHELL 433370 -5.6% 0.6847E+05 0.1177E+07 0.4911E+05 0.1372E+07 0.000
19300 0.1447 0.7500E-05 SHELL 457253 -6.0% 0.6909E+05 0.1178E+07 0.5181E+05 0.1382E+07 0.000
19400 0.1455 0.7500E-05 SHELL 1585650 -7.1% 0.6940E+05 0.1169E+07 0.5469E+05 0.1392E+07 0.000
WARNING INTERFACE NB 2
GAP= 3.15000000000000 PENE= 3.14999999971815
LINE 1740244 1740245 DE-ACTIVATED FROMINTERFACE
19500 0.1459 0.4113E-11 SH_3N 1904067 99.9% 0.6939E+05 0.1143E+07 0.4126E+17 0.1397E+07 0.000
19600 0.1459 0.5668E-07 SHELL 197222 99.9% 0.6939E+05 0.1143E+07 0.4126E+17 0.1397E+07 0.000
19700 0.1462 0.7429E-09 INTER 2 99.9% 0.6974E+05 0.9476E+11 0.4126E+17 0.1402E+07 0.000
WARNING INTERFACE NB 2
GAP= 3.15000000000000 PENE= 3.14999999973051
LINE 1740245 1740246 DE-ACTIVATED FROMINTERFACE
19800 0.1462 0.1753E-08 INTER 2 99.9% 0.6974E+05 0.1105E+07 0.4450E+17 0.1402E+07 0.000
WARNING INTERFACE NB 2
GAP= 3.15000000000000 PENE= 3.14999999971615
LINE 1740245 1740627 DE-ACTIVATED FROMINTERFACE
i've done component wise energy plot for rotational energy but no such relevant data was found and their rotational energy was limited to e+3. i've checked for penetration of interface in 000.out but there isn't any . i am attaching graphs for ref
<?xml version="1.0" encoding="UTF-8"?>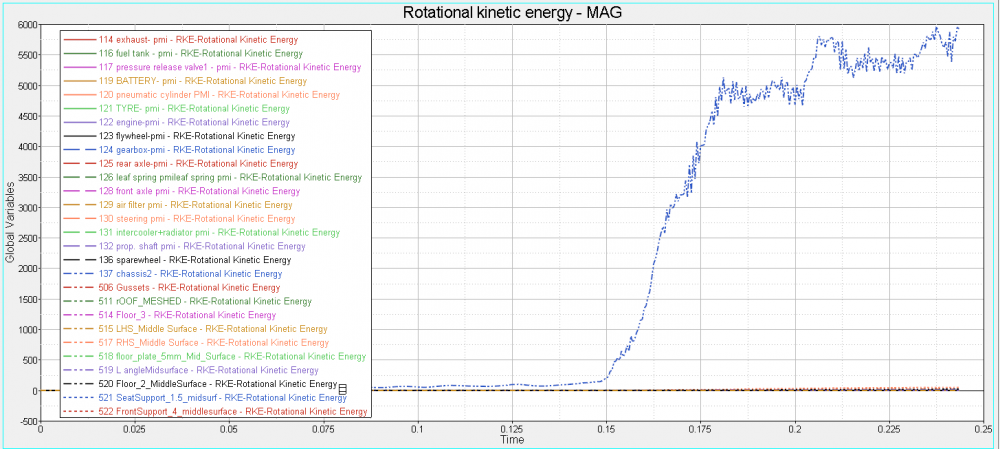
<?xml version="1.0" encoding="UTF-8"?>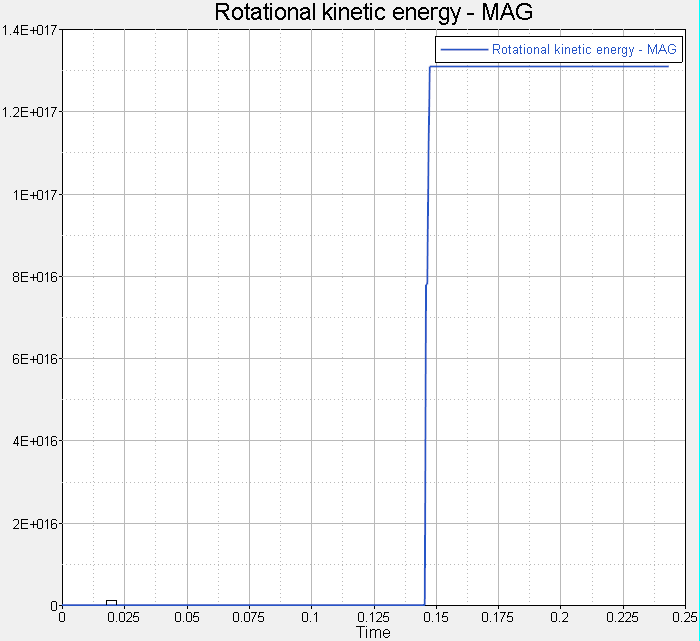