Why the result of free size optimization become like this?
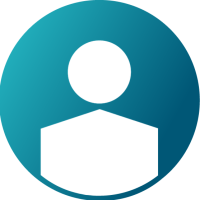
I am doing the free size optimization with sandwich structure in order to minimize mass of the structure.
And the way I create the sandwich structure is create the ply first and then use the STACK to create the laminate and use Symmetric option to define Sandwich structure. When I create the ply, the parameter that I need to put is the thickness and I understand that the value of thickness that I put, It'll be the upper limit of thickness that ply can be during optimization process
As the picture below I set the constraint which is 7 constraints. And It took a while to run this problem. After finish the run It shows the message "OPTIMIZATION HAS CONVERGED. FEASIBLE DESIGN (ALL CONSTRAINTS SATISFIED)."
But when I check the result in each subcase, it does not pass the constraint as it said. Why it happen like this? Is it because of me forgot something?
I will attach the model and result file in case of you would like to see my model further.
https://drive.google.com/file/d/1fvjos54CZ6kpF5YuPpFrfZ4i7k8NBbIj/view?usp=sharing
Best Answer
-
How far do they miss by? They would be allowed to go to (-)1.83214 with the default constraint tolerance of 1% if the summary in your out file shows those nodes as 'A' (active') with a value higher/lower than 1.814 that means they are in that 1% band and the optimisation will consider them as 'ok'.
If it is just that 1% and nothing further wrong, the results are acceptable, you can set a lower value for 'CONTOL' in DOPTPRM to get closer, or set your constraints slightly lower to ensure nothing goes over your requirement of 1.814 if it is absolutely essential.
(Be careful though, In analysis phase you are looking for design direction especially at freesize phase where there will be subsequent design iteration changes on plies etc and manufacturing constraints will likely remove structural performance too, and 1% is likely smaller than the disparity between analysis and reality in any case, so if your requirements are 1.814 in the real world, you should probably build in a bigger safety factor anyway at this stage.)
NB: I noticed, your 'upperbeam' component isn't joined together in the middle, connecting that should help your torsional stiffness
1
Answers
-
And now I try to do the free size optimization again to check what's wrong with my model by reduce the number of constraint function to make it run faster. And I found that the result from the last iteration pass only last constraint function.
As you can see the displacement from node id 77987 has the displacement in y axis equal to -1.088 mm which pass the constraint function in only id 3. So, I guess that the program will run and try to satisfied in each constraint but when we change to another load case, the one that passed before it will be not pass. And the constraint that pass for sure will be the last id of constraint function.
How can I deal with this problems, are there any cards in Optimization module to control this problems?
Thank you in advance.
0 -
So far as I can see, that node (77987) doesn't have any displacement constraint on it in any of your loadcases?
The only nodes with displacement constraints are shown here:
0 -
Paul Sharp_21301 said:
So far as I can see, that node (77987) doesn't have any displacement constraint on it in any of your loadcases?
The only nodes with displacement constraints are shown here:
Sorry, I wrote the wrong number of node id It is 77952 that pass the constraint id 3 (pure torsion2).
More information, And when I check the node id 5889 that actually need to pass the constraint number 2 that define the upper bound is 1.814 mm, but it did not pass.
How can I deal with this problems, are there any cards in Optimization module to control this problems?
Thank you in advance.
0 -
How far do they miss by? They would be allowed to go to (-)1.83214 with the default constraint tolerance of 1% if the summary in your out file shows those nodes as 'A' (active') with a value higher/lower than 1.814 that means they are in that 1% band and the optimisation will consider them as 'ok'.
If it is just that 1% and nothing further wrong, the results are acceptable, you can set a lower value for 'CONTOL' in DOPTPRM to get closer, or set your constraints slightly lower to ensure nothing goes over your requirement of 1.814 if it is absolutely essential.
(Be careful though, In analysis phase you are looking for design direction especially at freesize phase where there will be subsequent design iteration changes on plies etc and manufacturing constraints will likely remove structural performance too, and 1% is likely smaller than the disparity between analysis and reality in any case, so if your requirements are 1.814 in the real world, you should probably build in a bigger safety factor anyway at this stage.)
NB: I noticed, your 'upperbeam' component isn't joined together in the middle, connecting that should help your torsional stiffness
1 -
Paul Sharp_21301 said:
How far do they miss by? They would be allowed to go to (-)1.83214 with the default constraint tolerance of 1% if the summary in your out file shows those nodes as 'A' (active') with a value higher/lower than 1.814 that means they are in that 1% band and the optimisation will consider them as 'ok'.
If it is just that 1% and nothing further wrong, the results are acceptable, you can set a lower value for 'CONTOL' in DOPTPRM to get closer, or set your constraints slightly lower to ensure nothing goes over your requirement of 1.814 if it is absolutely essential.
(Be careful though, In analysis phase you are looking for design direction especially at freesize phase where there will be subsequent design iteration changes on plies etc and manufacturing constraints will likely remove structural performance too, and 1% is likely smaller than the disparity between analysis and reality in any case, so if your requirements are 1.814 in the real world, you should probably build in a bigger safety factor anyway at this stage.)
NB: I noticed, your 'upperbeam' component isn't joined together in the middle, connecting that should help your torsional stiffness
Thank you so much, sir. The thing that you noticed me about upper beam, it really helps me. I've edit the model and then set the value of CONTOL lower to make it close to the value that I set as a constraint more when it converged.
0