Rigid flexible coupling simulation of vehicle
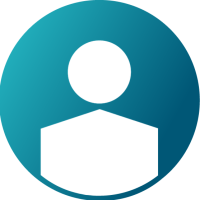
Hi, guys!
I am studying the influence of the bending and torsional stiffness of BIW on the handling. The process is as follows:
(1) Obtain the mnf file of the BIW by HyperMesh (CMS);
At this stage, to simplify the model, I removed the seats, doors and interior. In order not to change the mass center and moment of inertia of the whole vehicle, I used concentrated Conm2 at the mass center of each deleted part, and use rbe3 to connect them with the surrounding elements.
(2)Buliding the rigid multibody dynamic model in Adams/car;
(3) Replace the Chassis Part (rigid) with the mnf file of the BIW to obtain the rigid-flexible coupling multibody dynamic model;
I've verified that it was successful to simulate for the handling. The output curves of the rigid-flexible coupling model were very close to that of the rigid body model. However, there are huge errors when I use the same model to simulate for the ride. I guess that the method of obtaining the mnf file is problematic.
The following is the output result of a ride comfort simulation test under the condition of deceleration belt:
Figure1. seat rail bolt x acceleration
Figure2. seat rail bolt z acceleration
Note: Red-- the rigid-flexible coupling multibody dynamic model;
Blue--the rigid multibody dynamic model;
pink--the test data;
The measuring point is located at the bolt hole connecting the seat and the guide rail. For the ride simulation, the output curves is good in x direction (the direction of the vehicle). But in z direction being vertical to the ground, when the front wheel passes through the deceleration belt, the longitudinal acceleration of the rigid-flexible coupling multi-body dynamic model is too large. And the trend also seems to be wrong.
Please help me! It is appreciated for any reply!
Answers
-
Hello Zaily -
Does the test data also been captured without the seats ? My guess is it is not.
The seat and rails offer additional stiffness to the BIW which is not captured by your flexible body. RBe3 only transfers the forces or compensates for the mass but does not add any stiffness.
You could try by using an RBE2 between the body and the bolt holes.
BTW, same set up can be solved using MotionView/MotionSolve.
Regards
Praful
0