Beginner with Optistruct: Questions about "big models"
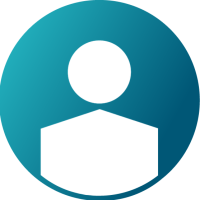
Hello,
I have been using FEA software for ten years and just switched to Design optimisation a year ago through reading the few intern procedures we have and Altair online help. I only have a basic understanding of its purpose, but let alone everything related to equations.
I have been using Inspire V2020 the whole time and managed to do everything I needed by then, working on relatively small solid parts like lower arm, knuckles, etc.
I recently learned how to use Optistruct directly with written input files, as we had some automation scripts I could use to learn about it. I use ANSA for setting up the model as I always used it until now.
I could have used Inspire for this whole study, but the last version wasn't ready at the moment and we couldn't use the server as it was going to be ready for the last version, so that wasn't an option.
I have some studies to do about large parts (vehicule subframe).
The goal is to see the best global shape for the part using stiffness constraints and some real load cases. I have a volume of about 600kg of steel to reduce to only 20kg and I learn that I cannot go too low on the mass fraction of an optimisation calculation as the solver could be unstable.
=> Is there really no means to have such a optimisation done in one calculation only ?
=> Does that mean that min mass calculations when you have a too big volume will necessary fail ?
=> Is there a way to obtain a design suited for steel sheet parts without relying on a very fine mesh and stamping process ? I know that double draw can be used to force for closed hollow sections in simple case, but it seems hard to apply here considering the size of the part.
If there's no solution in one go, that means that I need to do successive iterations:
Volume1 gotten from design team -> Optimise Volume1 -> Ossmooth of Volume1 -> Remesh it to obtain "Volume2" => Optimise Volume2 ->…
Though I'm not familiar with HyperMesh, I could use the Ossmooth to smooth the results from the first optimisation. The problem is, I always get a mesh which isn't of good quality, even when I try to improve its quality automatically through ANSA. I don't want my only option to be CHECKEL=NO.
=> Is there a mean to make sure that my FEM reanalysis Ossmooth can pass the solver mesh quality expectations without have to hand correct every corner of the model ?
=> Is there a way to smooth the mesh without having very fine mesh done by the Ossmooth ? I tried to adjust some 2D and 3D criteria on HyperMesh but I couldn't see any impact on the mesh.
I tried to output a geometry instead to remesh it in ANSA, but I couldn't get the whole part and ended up just having the smooth surface… partly.
=> Is there a mean to have the whole assembly as geometry as an Ossmooth result ? It could be much easier for me to work with this and also that would be usable for the designer team. (To surface in ANSA to obtain geometry from FE is not that great…)
Thank you in advance for your time,
Florian G.
Answers
-
Hi Florian,
Looks like you have done quite a bit of exploration in Optimization. So now you must be knowing there are different optimization processes available like for Concept design you can go for Topology, Topography and Free size and for Fine tuning you can opt for Shape, Size and Free shape.
As you have asked about mass constraint, you can give the desired mass value in constraint field. When you are using volume fraction as constraint we suggest having an upper bound of 0.3. I am not sure why you are telling with big volumes, while doing min mass calculation it will fail. Did you come across any failure while doing the study?
Regarding mesh quality, when you are doing topology and topography it is suggested to have Tria/Tet mesh. You can also do reanalysis in Ossmooth where you have the option for splitting into tria and remeshing the parts with desired size.
OSsmooth is the tool used to create geometry after optimization. Lot of parameters are available to fine tune this. If still you are not getting good geometry you can try your hand with Altair Inspire. The polynurb options are really good to get better quality CAD.
Thanks
Rajashri
0 -
Hello Rajashri,
Thank you for your time and sorry for the late answer, as the site migration and vacations delayed it.
I managed to update my models and got to the point where my final model could reach the mass target, but I had to do three consecutive Max stiffness optimizations with mass fraction of 0.3 (~24 kg in the final model, as the starting model was of ~600kg). Tuning a bit the MEMBSIZ down through each step helped a bit.
I also managed to have a Min mass model working that gave similar results to the first max stiffness, not sure anymore why it wasn't working before though.
I found some options to help with the mesh quality directly in ANSA, but I still had to use the CHECK_EL=NO parameter to perform the optimizations. Since I got my hands on the last version of Inspire, I probably won't have to disable the CHECK_EL anymore, as the POLYNURBS usually works fine.
Regards,
Florian G.
0