reducing energy error and deformation artefacts
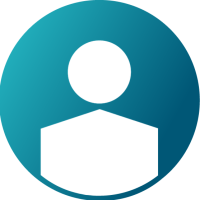
I'm trying to understand what causes the energy error in my main model and herefore created a dummy file.
The collision in the attached model results in an energy error of -34% and one corner node "flying away", stretching the element far more than the failure plastic strain should allow.
so I wonder if I:
- modeled the contact correctly
- correctly applied material parameters (material "GG-30" from the altair one online library)
- should use a failure model (but in my recent tests a "FAIL/JOHNSON" led to similar results)
Looking forward to learn something!
Best Answer
-
Paul Sharp_21301 said:
There are some things I would change, if you want to erode the solid elements you do need to use /FAIL card (and remove the EPSP limit in the material itself) but my first question is: what units you are trying to use and how you set up the material?
The values you have used don't seem to correspond to a common units system, (e.g. if Kg/mm/ms, your density is 10x too small, and your b and n are odd too, it looks like you have used Fatigue cyclic values from the properties card? Should be parameters for non linearity in plastic region of the material) You said you got the data from Altair One, if so, you can download the input for your required unit system directly (no need to 'interpret' the data by hand... below is kg/mm/ms for GG-30 from Altair Material Data Centre on Altair One, (you can ask for the solver input direct from the database) e.g:
Attached has material properties per the mat database for kg mm ms, /FAIL/JOHNSON is added to erode elements at 0.5% plastic strain, contact surface is modified to /SURF/ALL (so all surfaces of solids are in contact even after eroding elements) gapmin set on contact of 0.1mm
Model attached is per your original mesh, I also ran with 2mm nominal tetra size (upper model) comparison of energies on right shows 'error' lower (TTE should be 'flat') with smaller elements but think it is ok as it is due to the deletion of elements
1
Answers
-
There are some things I would change, if you want to erode the solid elements you do need to use /FAIL card (and remove the EPSP limit in the material itself) but my first question is: what units you are trying to use and how you set up the material?
The values you have used don't seem to correspond to a common units system, (e.g. if Kg/mm/ms, your density is 10x too small, and your b and n are odd too, it looks like you have used Fatigue cyclic values from the properties card? Should be parameters for non linearity in plastic region of the material) You said you got the data from Altair One, if so, you can download the input for your required unit system directly (no need to 'interpret' the data by hand... below is kg/mm/ms for GG-30 from Altair Material Data Centre on Altair One, (you can ask for the solver input direct from the database) e.g:
1 -
Paul Sharp_21301 said:
There are some things I would change, if you want to erode the solid elements you do need to use /FAIL card (and remove the EPSP limit in the material itself) but my first question is: what units you are trying to use and how you set up the material?
The values you have used don't seem to correspond to a common units system, (e.g. if Kg/mm/ms, your density is 10x too small, and your b and n are odd too, it looks like you have used Fatigue cyclic values from the properties card? Should be parameters for non linearity in plastic region of the material) You said you got the data from Altair One, if so, you can download the input for your required unit system directly (no need to 'interpret' the data by hand... below is kg/mm/ms for GG-30 from Altair Material Data Centre on Altair One, (you can ask for the solver input direct from the database) e.g:
Attached has material properties per the mat database for kg mm ms, /FAIL/JOHNSON is added to erode elements at 0.5% plastic strain, contact surface is modified to /SURF/ALL (so all surfaces of solids are in contact even after eroding elements) gapmin set on contact of 0.1mm
Model attached is per your original mesh, I also ran with 2mm nominal tetra size (upper model) comparison of energies on right shows 'error' lower (TTE should be 'flat') with smaller elements but think it is ok as it is due to the deletion of elements
1 -
Paul Sharp_21301 said:
There are some things I would change, if you want to erode the solid elements you do need to use /FAIL card (and remove the EPSP limit in the material itself) but my first question is: what units you are trying to use and how you set up the material?
The values you have used don't seem to correspond to a common units system, (e.g. if Kg/mm/ms, your density is 10x too small, and your b and n are odd too, it looks like you have used Fatigue cyclic values from the properties card? Should be parameters for non linearity in plastic region of the material) You said you got the data from Altair One, if so, you can download the input for your required unit system directly (no need to 'interpret' the data by hand... below is kg/mm/ms for GG-30 from Altair Material Data Centre on Altair One, (you can ask for the solver input direct from the database) e.g:
First of all thanks for the in-depth response!
I intended to use the units kg/mm/ms and the previous density was incorrect.
About the data: I didn't find the values I was looking for in the AltairOne. Maybe it's because I use the free version (why I couldn't ask for the solver input) but this is all the information that was shown to me:
Are the Law2-values located somewhere else?
0 -
Simon Birnbickel said:
First of all thanks for the in-depth response!
I intended to use the units kg/mm/ms and the previous density was incorrect.
About the data: I didn't find the values I was looking for in the AltairOne. Maybe it's because I use the free version (why I couldn't ask for the solver input) but this is all the information that was shown to me:
Are the Law2-values located somewhere else?
It should be under the CAE model tab for the material, you can see it in your screenshot
0 -
Simon Birnbickel said:
First of all thanks for the in-depth response!
I intended to use the units kg/mm/ms and the previous density was incorrect.
About the data: I didn't find the values I was looking for in the AltairOne. Maybe it's because I use the free version (why I couldn't ask for the solver input) but this is all the information that was shown to me:
Are the Law2-values located somewhere else?
Thanks, but you should note, your revised one, has corrected the material values, but you have no failure values defined on the /FAIL/Johnson card, gapmin is set 0.0 for the contact (so arbitrary value will be used), and the contact still uses /SURF/EXT for the contact definition so any erosion will result in holes in contact.
1 -
Paul Sharp_21301 said:
Thanks, but you should note, your revised one, has corrected the material values, but you have no failure values defined on the /FAIL/Johnson card, gapmin is set 0.0 for the contact (so arbitrary value will be used), and the contact still uses /SURF/EXT for the contact definition so any erosion will result in holes in contact.
Indeed, I had overlooked your second message. And since you uploaded your .rad file as well, there would have been no need to upload mine.
What I'm still wondering is:
How did you arrive at a gap_min value of 0.1? In the Radioss Course we were only showed recommendations for shell elements.
0 -
Paul Sharp_21301 said:
It should be under the CAE model tab for the material, you can see it in your screenshot
unfortunately the CAE-Model export is not available for free users. I was hoping I could still find the relevant parameters in the properties section.
But using the simplified input parameters for Law2 I should still be able to achieve similar results, right?
0 -
Simon Birnbickel said:
Indeed, I had overlooked your second message. And since you uploaded your .rad file as well, there would have been no need to upload mine.
What I'm still wondering is:
How did you arrive at a gap_min value of 0.1? In the Radioss Course we were only showed recommendations for shell elements.
0.1mm is just a pragmatic value chosen to minimise the 'offset' from the actual solid element surfaces while allowing a gap to calculate the penalty stiffness, if gapmin is set 0 or blank and all segments/surfaces are on solids, the default for gapmin is used:
This would 'work' but would lead to a bigger (and somewhat arbitrary) gap that is larger than 0.1
Entering the LAW2 params by hand is identical to downloading them from MDC if they are the same, ('a' is yield, 'b' and 'n' describe the shape of the plasticity curve), if you are entering manually, it may be easier to use 'IFLAG = 1' this allows you to enter UTS and strain at UTS instead of b and n (b and n are calculated internally), so you could enter 310MPa directly and failure strain directly, For failure strain, we were assuming 0.5%, but it is not clear to me that is the failure strain necessarily, (I'm not sure what the meaning of the elongation 5x diameter thing is!)
0