How to set the inflow velocity in RADIOSS
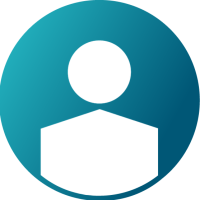
In radioss, we would like to analyze the following model.
I want to give a pulse wave (0.8 m/s) for 0.1 second after the initial inflow velocity (0.2 m/s), but when I run the calculation, this pulse wave is ignored.
Please let me know how to solve this problem.
Answers
-
Hello Motoki,
I have reviewed your model, and it was not able to run to termination time. So, I could not produce results at the time the pulse wave should exist.
The thing is that you had some inaccuracies to your model set-up too and that is why I propose the following changes:
- The /INTER/TYPE2 you use for the contact between blood and vessel is to simulate no-slip wall. In order for this interface to work, properly you have to insert an /ALE/BCS for all the nodes of the interface where the 4,5 and 6 DoFs will be activated.
- Additionally, you can use a slip wall formulation with /INTER/TYPE1 and no need for BCs, instead of the /INTER/TYPE2 you use now.
- The /IMPVEL that you have created for inlet velocity should not only apply to one node, but to every node between inlet and fluid part. This would not produce an error in your simulation, but not represent a physical situation. Be careful, because you have to insert /IMPVEL to the nodes that belong to both inlet and fluid and not the outer ones.
- It is also recommended to use Itype = 2 for inlet and not Itype = 1, but that is also a good practice advice and Itype = 1 should work too.
- In fluid material (/MAT/LAW6) you have to insert an Equation of State (/EOS) in order to produce accurate results. Actually without an /EOS set the model is not properly working for sure.
- Finally, is a good practice to insert more than 2 elements at the solid part, especially if you wait great deformations.
All of the above could have a fatal effect in your model and you should fix them before you procced. If other problems exist after you fixed these feel free to share.
I am also sharing a model similar to yours with a deformable pipe and FSI analysis in order to check it out and better understand the FSI set-up in Radioss.
0 -
Hi Polyvios
I attempted to modify the model based on your advice. To impose a no-slip condition between blood and vessel walls, I kept it as TYPE2 and added ALE/BCS. However, when applying MAT/LAW11 to impose Non-Reflective Frontiers at the outlet, an error related to "Negative Rho" occurs in the blood. I believe this is due to an inappropriate value for l_c (Characteristic Length). How is this value determined?
Additionally, when setting the outlet to have the same material as the entire blood, the calculations proceed without issues, but still, the pulse wave cannot be accurately represented.
Would you have any recommendations for this problem?
Furthermore, if there is an EOS suitable for simulating blood, please provide guidance on that.
0 -
Motoki Koga said:
Hi Polyvios
I attempted to modify the model based on your advice. To impose a no-slip condition between blood and vessel walls, I kept it as TYPE2 and added ALE/BCS. However, when applying MAT/LAW11 to impose Non-Reflective Frontiers at the outlet, an error related to "Negative Rho" occurs in the blood. I believe this is due to an inappropriate value for l_c (Characteristic Length). How is this value determined?
Additionally, when setting the outlet to have the same material as the entire blood, the calculations proceed without issues, but still, the pulse wave cannot be accurately represented.
Would you have any recommendations for this problem?
Furthermore, if there is an EOS suitable for simulating blood, please provide guidance on that.
Hi Motoki,
The reasons the Negative Rho error appear might relate to Non-Reflect Boundary formulation you refer to. To set that properly you have to insert the correct value of characteristic length, which in your case is equal to the length of the vessel (not the diameter or radius). So, in your case should be equal to 0.3.
Additionally, it is mandatory to insert a proper /EOS because this directly affect the calculation of hydrodynamic pressure calculation and also affect the speed of sound you insert. The different equations you may try are /EOS/LINEAR and /EOS/STIFF_GAS. You can find some examples of these in the following Bottle Drop KB article and the Mok Benchmark model I am attaching:
Based on the /EOS a new sound speed should be calculated and also inserted as a parameter to NRF boundary (Outlet).
Also, for the Inlet velocity you now use a uniform profile, is that the case you want or a parabolic profile suits better? Anyway, you might have some bounce back effects that can cause velocity components in vertical directions. You can try to insert a BCS with enabled the DoFs in X and Y directions to be sure that velocity will only exist in Z axis.
Also, for velocity inlet you should select the node that belong to Inlet and Blood interface not the outer nodes.
Finally, something else that can affect your result is the pressure condition in inlet and outlet. You have inserted 1 Pa for both of inlet and outlet. Is that the case? Because if for example for inlet you know only the velocity, pressure stagnation should left blank.
0 -
Polyvios Romanidis said:
Hi Motoki,
The reasons the Negative Rho error appear might relate to Non-Reflect Boundary formulation you refer to. To set that properly you have to insert the correct value of characteristic length, which in your case is equal to the length of the vessel (not the diameter or radius). So, in your case should be equal to 0.3.
Additionally, it is mandatory to insert a proper /EOS because this directly affect the calculation of hydrodynamic pressure calculation and also affect the speed of sound you insert. The different equations you may try are /EOS/LINEAR and /EOS/STIFF_GAS. You can find some examples of these in the following Bottle Drop KB article and the Mok Benchmark model I am attaching:
Based on the /EOS a new sound speed should be calculated and also inserted as a parameter to NRF boundary (Outlet).
Also, for the Inlet velocity you now use a uniform profile, is that the case you want or a parabolic profile suits better? Anyway, you might have some bounce back effects that can cause velocity components in vertical directions. You can try to insert a BCS with enabled the DoFs in X and Y directions to be sure that velocity will only exist in Z axis.
Also, for velocity inlet you should select the node that belong to Inlet and Blood interface not the outer nodes.
Finally, something else that can affect your result is the pressure condition in inlet and outlet. You have inserted 1 Pa for both of inlet and outlet. Is that the case? Because if for example for inlet you know only the velocity, pressure stagnation should left blank.
Thank you for your advice.
Following your guidance, I made the following changes to the model:
- Introduction of EOS_LINEAR (setting parameters to achieve a sound speed C = 20 m/s).
- Leaving the pressure stagnation blank.
- Setting IMPVEL-related sets at the interfaces of INLET and BLOOD.
I executed the calculations using this modified model, but encountered large ERR values. When reviewing the animation file, it appears that the velocity at the inlet does not propagate backward. Additionally, removing the EOS stabilizes the ERR values to smaller magnitudes, although the results remain consistent.
What should I do to address this issue?
0 -
Motoki Koga said:
Hi Polyvios
I attempted to modify the model based on your advice. To impose a no-slip condition between blood and vessel walls, I kept it as TYPE2 and added ALE/BCS. However, when applying MAT/LAW11 to impose Non-Reflective Frontiers at the outlet, an error related to "Negative Rho" occurs in the blood. I believe this is due to an inappropriate value for l_c (Characteristic Length). How is this value determined?
Additionally, when setting the outlet to have the same material as the entire blood, the calculations proceed without issues, but still, the pulse wave cannot be accurately represented.
Would you have any recommendations for this problem?
Furthermore, if there is an EOS suitable for simulating blood, please provide guidance on that.
Hello Motoki,
Without EOS the simulation might not run generally, or if it runs can not calculate the proper results. How do you cross-check that the produced results with and without EOS are the same? I also recommend you check the pressure results, if you haven’t so far, because EOS is used to calculate the pressure.
With Bulk modulus equal to 400000 Pa and density equal to 1000 kg/m^3 the speed of sound should be 20 m/s. Compared with the initial maximum speed, which is equal to 0.8 m/s, a Mach number equal to 0.04 is calculated. This number secures that your simulation is in incompressible region (M<0.3).
Generally, an increasing ENERGY ERROR that reaches ±99% can indicate the simulation has diverged. However, in certain situations a high ENERGY ERROR can be acceptable.
Large ERROR values are expected in simulations like that. This happens because in this system the total energy is not preserved throughout the simulation. We have mass with non-zero velocity entering the system and hence an Energy Error occurs.
Polyvios
0 -
Polyvios Romanidis said:
Hello Motoki,
Without EOS the simulation might not run generally, or if it runs can not calculate the proper results. How do you cross-check that the produced results with and without EOS are the same? I also recommend you check the pressure results, if you haven’t so far, because EOS is used to calculate the pressure.
With Bulk modulus equal to 400000 Pa and density equal to 1000 kg/m^3 the speed of sound should be 20 m/s. Compared with the initial maximum speed, which is equal to 0.8 m/s, a Mach number equal to 0.04 is calculated. This number secures that your simulation is in incompressible region (M<0.3).
Generally, an increasing ENERGY ERROR that reaches ±99% can indicate the simulation has diverged. However, in certain situations a high ENERGY ERROR can be acceptable.
Large ERROR values are expected in simulations like that. This happens because in this system the total energy is not preserved throughout the simulation. We have mass with non-zero velocity entering the system and hence an Energy Error occurs.
Polyvios
Hello Polyvios,
Based on your advice, I inserted the EOS and applied the calculated speed of sound to the inlet and outlet, resulting in a transition to low error values and enabling the calculations.Now, I would like to increase the value of DT for the calculations. Currently, I am using DT/NODA/CST. I adopted DT=5.0e-6 based on "INITIAL ADDED MASS ESTIMATION" in the 0000.out file. However, even after rewriting the 0001.rad file and attempting the calculations, this DT value is not being applied.
In reality, I would like to set a much higher DT (around 1.0e-4). How can I achieve this?
0 -
Motoki Koga said:
Hello Polyvios,
Based on your advice, I inserted the EOS and applied the calculated speed of sound to the inlet and outlet, resulting in a transition to low error values and enabling the calculations.Now, I would like to increase the value of DT for the calculations. Currently, I am using DT/NODA/CST. I adopted DT=5.0e-6 based on "INITIAL ADDED MASS ESTIMATION" in the 0000.out file. However, even after rewriting the 0001.rad file and attempting the calculations, this DT value is not being applied.
In reality, I would like to set a much higher DT (around 1.0e-4). How can I achieve this?
Hi Motoki,
The DT/NODA/CST is affecting only the nodal time step and hence the solid elements in your simulation. In your occasion the minimum time step is based on a fluid element and that is why the command you think you insert is effective.
Unfortunately, you can not impose a specific time step for fluid elements. The only way to change time step is by changing your model. The parameters that effect the fluid elements time step are:
- Fluid Density
- Element size
- Bulk modulus
The fluid density has to be as it is, because otherwise the simulation won't be consistent with the physical system.
The element size can probably change without an effect and be more coarse (less elements), but also that applies up to a specific point.
Finally, the bulk modulus can be decreased to enable a higher time step. Of course, bulk modulus have a straight effect to fluid compressibility and probably change the response of your system. I see that you have applied a really high bulk modulus (10^7) which is the reason for a low time-step.
Bulk modulus should be set in a proper value to simulate the exact response of your fluid. In the next diagram you can see the response of an FSI simulation of a plate inside a tube (the Mok Benchmark I sent you). You can see that Bulk modulus creates a delay in structures response and can lead to weird phenomena (correct response above 5000-10000 value for bulk modulus).
You have to find a proper compromise between the time step you can use and the compressibility you will allow to your fluid.
The diagram I sent you is about a structure submerged in the fluid and hence the compressibility effect have probably greater influence to the structure. In your model that structure is not submergible but works as a boundary to fluid domain, smaller maximum Mach number can lead to better results. I would propose you to start with a bulk modulus equal to 10^5 and with trial and error find the proper value.
If the time step that fluid elements impose become greater than the one calculated for solid elements you can then use /DT/NODA/CST to impose a time step. Of course the imposed time step sound not be greater than the one calculated for fluid, otherwise the later will be used.
Polyvios
0 -
Polyvios Romanidis said:
Hi Motoki,
The DT/NODA/CST is affecting only the nodal time step and hence the solid elements in your simulation. In your occasion the minimum time step is based on a fluid element and that is why the command you think you insert is effective.
Unfortunately, you can not impose a specific time step for fluid elements. The only way to change time step is by changing your model. The parameters that effect the fluid elements time step are:
- Fluid Density
- Element size
- Bulk modulus
The fluid density has to be as it is, because otherwise the simulation won't be consistent with the physical system.
The element size can probably change without an effect and be more coarse (less elements), but also that applies up to a specific point.
Finally, the bulk modulus can be decreased to enable a higher time step. Of course, bulk modulus have a straight effect to fluid compressibility and probably change the response of your system. I see that you have applied a really high bulk modulus (10^7) which is the reason for a low time-step.
Bulk modulus should be set in a proper value to simulate the exact response of your fluid. In the next diagram you can see the response of an FSI simulation of a plate inside a tube (the Mok Benchmark I sent you). You can see that Bulk modulus creates a delay in structures response and can lead to weird phenomena (correct response above 5000-10000 value for bulk modulus).
You have to find a proper compromise between the time step you can use and the compressibility you will allow to your fluid.
The diagram I sent you is about a structure submerged in the fluid and hence the compressibility effect have probably greater influence to the structure. In your model that structure is not submergible but works as a boundary to fluid domain, smaller maximum Mach number can lead to better results. I would propose you to start with a bulk modulus equal to 10^5 and with trial and error find the proper value.
If the time step that fluid elements impose become greater than the one calculated for solid elements you can then use /DT/NODA/CST to impose a time step. Of course the imposed time step sound not be greater than the one calculated for fluid, otherwise the later will be used.
Polyvios
Hi Polyvios,
Thank you for your advice.
I would like to set the bulk modulus to 1.0e5 and then proceed with trial and error.
By the way, I have come across information that recommends against using DT/NODA/CST when using TYPE2. If I don't use DT/NODA/CST, can I simply use DT/ or are there other recommended settings?
0 -
Motoki Koga said:
Hi Polyvios,
Thank you for your advice.
I would like to set the bulk modulus to 1.0e5 and then proceed with trial and error.
By the way, I have come across information that recommends against using DT/NODA/CST when using TYPE2. If I don't use DT/NODA/CST, can I simply use DT/ or are there other recommended settings?
Hi Motoki,
The DT/NODA/CST is generally compatible with the /INTER/TYPE2. The only thing you should be careful with is the Spotflag formulation you use. If a penalty method has been selected then the /DT/NODA/CST is not compatible.
You can check out the different options for Spotflag formulation in the following link.
https://2021.help.altair.com/2021/hwsolvers/rad/topics/solvers/rad/inter_type2_starter_r.htm
I would recommend you to use /DT/NODA/CST/0 because this keyword is used to impose a specific time step. In contrast /DT will not help you to achieve a higher time step, because if the Tmin is reached the solution stops. You can check out the following link too.
https://help.altair.com/hwsolvers/rad/topics/solvers/rad/dt_engine_r.htm?zoom_highlight=/dt
Of course, as I told you in the previous reply, you have to be sure that the time step that controls the simulation comes from a solid element.
Polyvios
0