Supports of the suspension in the monocoque doesn't work like they're supposed to
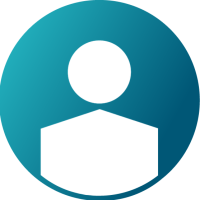
Hi,
I need your opinion and experience to solve a problem. I’m making a composite optimization on a monocoque, and I’m having some problems modeling the suspension. We have some supports that make the connection between the A-arms of the suspension and the monocoque (I’ll attach one photo). We have problems because we simulate the support with a RBE2 (independent node on the A-arm, dependent nodes in the monocoque; I’ll attach one print-screen), and this gives infinite stiffness on the laminate, so in the results of the optimizations there are almost zero stresses on the elements that have nodes on the rigid. This affects our optimization a lot, so the area off the supports are one of the most weak points on our stucture (some of them even started to break on our last monocoque). We even thought about using RBE3, because it doesn’t give additional stiffness, but the way that it works seems to not make sense in our case. What do you suggest to do in order to simulate this in a more proximity to what really happens?
Thank you
Answers
-
Hi @Pedro Neves
Do see displacement on the dependent nodes?
Not sure what is causing the problem. Is it possible to share the model files?
Please use the file transfer link in my signature to share the model file
0 -
Hi Pedro Neves,
the most accurate load introduction is to model the A-arm mounting brackets. Simplifying with RBE2 or RBE3 elements can lead to stress concentrations and non-physical stiffening.
0 -
Altair Forum User said:
Hi Pedro Neves,
the most accurate load introduction is to model the A-arm mounting brackets. Simplifying with RBE2 or RBE3 elements can lead to stress concentrations and non-physical stiffening.
Agree. but with some assumptions, it can be simplified with Rigid elements. But according to Pedro, the stiffness is way too much. This could be a modeling error or something is missing.
0 -
@Prakash Pagadala yes there is displacement in the dependent nodes.
Ok, I'll try to send you 2 files, one with one model of my initial model and another with the result of the final optimization
0 -
Altair Forum User said:
Hi Pedro Neves,
the most accurate load introduction is to model the A-arm mounting brackets. Simplifying with RBE2 or RBE3 elements can lead to stress concentrations and non-physical stiffening.
Ok, but even if I model them, I'll have to make a connection with rigids, because they're an independent component of the monocoque, right? Or there's another way that I can simulate the way that the supports are conected to the monocoque?
0 -
The connection between the support brackets and monocoque can be modeled more accurately by bolt connectors.
0 -
@Ivan cool, I didn't know about this feature, I'll try to understand how it's used and put it on my model. Thanks!
0 -
@Prakash Pagadala have you already looked into my model?
0