Stiffness (MAT/LAW59/E) and failure (FAIL/CONNECT) in an adhesive(glue) connector element.
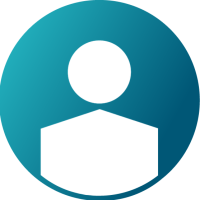
For the verification of the glued connections in a crash simulation, I would like to apply a connector element including failure.
To that end, an adhesive(glue) with /MAT/LAW59, /PROP/TYPE43 and /FAIL/CONNECT should be defined.
As a start, Example RD-E 4802 Solid and Spring Spotweld in Crash box is looked into, since this is the most resembling example.
However, two point remain unclear to me:
- The Youngs modulus of the adhesive(glue) is defined independent of height (i.e. [MPa/mm]), as stated in the theory manual and reference manual.
However, in this example this seems not to be the case.
The provided E = 210GPa, over a spotweld thickness of 1.8mm. That would mean that /MAT/LAW59/E = 210000/1.8 = 116666.67MPa/mm. However, the example .hm file uses a value of 21GPa.
Could you provide clarity w.r.t the Young’s (and shear) modulus? Should it be divided by the element height/connector height and is it than still possible to use >1 coat (multiple elements over the connector height) ? - It is unclear to me what is used as failure criteria.
The reference manual and example manual state that a relative displacement criteria is used (without SI unit).
However, in HM this variable is called epsilon_maxN (or epsilon_maxT) which would normally refer to a strain.
Furthermore, the example reference concludes from the Strain(VonMises) plot, that elements have failed.
Could you provide me clarity w.r.t the criteria on which is based when an element fails (and thus is deleted) and whether this is influenced by element/connector height?
Answers
-
Hi
It seems you send same question on support channel. Then suggest follow up from there
REgards
0 -
Hi Rogerio Nakano,
Would you be kind enough to add the link to the question raised on support channel? It would be useful to understand few inputs related to adhesives.
Regards,
Karthick S.
0 -
Hi Rogerio Nakano,
Would you be kind enough to add the link to the question raised on support channel? It would be useful to understand few inputs related to adhesives.
Regards,
Karthick S.
Hi, I have the same question!
0 -
1)
The modulus is independent of the height, meaning that stress is associated to the elongation of the element. So the connect element can set even as zero height.
The ratio MPa/mm is not obtained by dividing the Material Young Modulus per the element height
In the example, the value 21,000MPa/mm just happens to be by chance a value multiple of Steel Young Modulus. It could have been any other number that you would like to use for your analysis, from your references.
The parallel that can be made is thinking of the connect element as a spring but the elongation is related to stress in the element, not the force (as it would be in spring element).You should not use multiple connect elements 'through the thickness'
2)
The failure criterion used in the example is the relative displacement, or elongation of the element.
I agree the labels may be misleading here, but the 'epsilon_maxT' or 'epsilon_maxN' are maximum elongation in Tangential and Normal directions.0