Radioss New User: Deformation/Failure does not appear corect
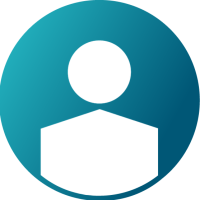
I have setup a simple simulation trying to predict the failure of a washer. I have applied "Imposed Velocity" loading. When animating the results, instead of seeing some type of crack or failure, all the elements appear to be flying apart. Not sure how to fix/resolve this issue. I have attached the animation as well the solver deck that I am running. Any help/pointers are appreciated.
Best Answer
-
Ashmita Tiwari said:
Followup question: I noticed that you created Rigid Body Element and connected all the nodes of components I wanted to be rigid.
I had tried making them Rigid earlier (choosing the Rbody option), but I was getting an error when trying to run the model. I assumed that making them Rigid would be the ideal thing to do. What would you recommend as a modeling practice/guidance?
Yes, for this simulation, the supports and loading part can be rigid, adding them to an RBODY means the elements don't contribute to the timestep calculation and simplifies constraint and loading. You may have got an error when you tried it if you still had the boundary condition as you had it originally (all the nodes of the bottom of the part) as once the RBODY has been defined you may only constrain the main node (not the secondaries).
1
Answers
-
I made some changes (attached), nothing more than necessary to get the model to run, not sure what the critical bit below was (probably a combination of very high stiffness in supports and contact options), I just changed everything I saw that I would do differently.
This runs more happily now, I'm no sure what your end goal is but you may want to make other changes based on this run.
I added ISTF=4 (minimum of main/secondary) stiffness to your contacts, and added to each of them a gapmin value (0.15 at top, 0.2 at bottom) corresponding to approximate spacing of your parts (you should always set gapmin with Type7 otherwise it calculates it's own based on your solid element dimensions)
There was no friction in your contacts, and I haven't added any but you may want to add some? You might also want to look at adding a symmetrical contact (reversing the main and secondary from your existing contacts) between washer and supports/loading part, and edge-edge contact to improve the contact accuracy. You could also consider self contact on the washer, it passes through itself in some areas now it is cracking.
I changed your solid element formulation to HEPH (ISOLID = 24), this is a newer element formulation with less propensity to hourglass.
Since it seems you want the parts other than washer to be rigid?, I made them rigid and set your 'steel' material back to steel properties. (setting very high stiffness like this drives down the timestep dramatically and thereby increase run time substantially, as well as giving a very high contact stiffness)
I modified the constraints to apply to the main nodes of the Rigid Bodies (top and bottom) and added a constraint to the loading part perpendicular to the loading so it doesn't fly away. The washer itself is still unconstrained, and because there is nothing to stop it, it jumps sideways on initial loading, you may want to look at that too.
You had 3 separate conflicting timestep controls, I just kept one of them setting the model to use nodal timestep with no mass scaling.
It doesn't need to run for 5s, I reduced to 700ms, the washer is pretty much destroyed by then!
The washer now fails, and the run goes much more quickly (25 mins on 2 cores on my laptop)
1 -
Thank you so much Paul. Your changes did the job. The model now runs properly. Really appreciate your help.
0 -
Followup question: I noticed that you created Rigid Body Element and connected all the nodes of components I wanted to be rigid.
I had tried making them Rigid earlier (choosing the Rbody option), but I was getting an error when trying to run the model. I assumed that making them Rigid would be the ideal thing to do. What would you recommend as a modeling practice/guidance?
0 -
Ashmita Tiwari said:
Followup question: I noticed that you created Rigid Body Element and connected all the nodes of components I wanted to be rigid.
I had tried making them Rigid earlier (choosing the Rbody option), but I was getting an error when trying to run the model. I assumed that making them Rigid would be the ideal thing to do. What would you recommend as a modeling practice/guidance?
Yes, for this simulation, the supports and loading part can be rigid, adding them to an RBODY means the elements don't contribute to the timestep calculation and simplifies constraint and loading. You may have got an error when you tried it if you still had the boundary condition as you had it originally (all the nodes of the bottom of the part) as once the RBODY has been defined you may only constrain the main node (not the secondaries).
1