we want to know that a clip hold a pipe , pipe is fixed , when we tight the clip and apply load on clip is 350 N, pipe is bended and freely rotate . how to stop the pipe for rotating and in clip has stopper for not rotating the pipe what force need s
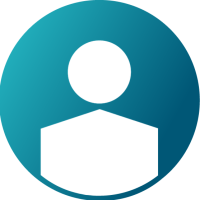
Answers
-
i assume you're running a NL implicit analysis in OptiStruct, right?
you can add details of your model in the message instead of the title.
But a few questions:
- are you using friction in your model?
0 -
Hello sir,
Yes sir, this is a non- linear static analysis process in optistruct. My model has steel property. we want to know the what force feel the stopper when applied 350 N load on a clip when pipe is fixed. and know this process when become fail. yes friction may apply when pipe rotate when load applied into a clip contact browser tool is used.
tell me please solution
Thanks
0 -
PLZ SOLVE THE PROBLEM
0 -
impauto said:
PLZ SOLVE THE PROBLEM
hi,
you need to be more clear on what you're trying to achieve here.
The pipe is fixed at its ends, right?
the force of 350N is fixed and applied at the RBE2.
Now, where is the other force applied? Are you applying them to the 2 small bolts? Is that a pretension force that you're applying? What is the friction coefficient that you have?
Have you modelled the bolt? Have you included pretension? Have you included contacts with friction?
0 -
Adriano A. Koga_21884 said:
hi,
you need to be more clear on what you're trying to achieve here.
The pipe is fixed at its ends, right?
the force of 350N is fixed and applied at the RBE2.
Now, where is the other force applied? Are you applying them to the 2 small bolts? Is that a pretension force that you're applying? What is the friction coefficient that you have?
Have you modelled the bolt? Have you included pretension? Have you included contacts with friction?
Here an example based on your description, but applying a pretension load to beam elements, and varying the pretension load.
In these models, I've requested CONTF output, as it writes both contact forces and status.
From the status, it is possible to see that as the pretension load is smaller, the contact status changes, and at 400N of pretension, the bracket starts to loose friction. Below this value, the model starts struggling to converge, as there is free body movement.
0 -
no other force applied ,only 350 n load apply on rbe2 . here we assume closed assembly already bolted ,we try to find out when we apply load 350 n on the c;lip ,the clip will rotate or not along the pipe. pipe and clip has contact only check for slide.
0 -
Please tell me what conditions apply for this . what uses condition in the deck like as card, boundary conditions etc
0 -
Hii sir,
I have simulated on this clip and pipe.
I have done validate the model and meshing of 1 mm on this model. i have applied material and its properties to the model after that apply load collector ( spc,load as force1 for follwer load).
and used contact browser ( auto conatct , its properties used S2S on all small, finite,continous ).also used param card ( use fllwer 1, hassaam yes,lgdisp 1) and global output request card ( uses disp,spcf,strain, stress).
used collector step inputs ( NLPARAM,NLOUT)
At last used collector step and choose non-linaer static condition and apply spc,load,NLPARM,NLOUT.
I USED LOAD 300 N ,250 N, 200 N, 100 N ETC
WE Observe the vonmises stress at simple, the stress and strain of 100 N is high from 200N,250N,300N,350N.
but sress is less for less force and high for high stress.
but in my model show 100N load stress is high from others load whose more than 100N .
TELL ME THE REASION ,if any mistake in this also tell me.
0 -
impauto said:
Hii sir,
I have simulated on this clip and pipe.
I have done validate the model and meshing of 1 mm on this model. i have applied material and its properties to the model after that apply load collector ( spc,load as force1 for follwer load).
and used contact browser ( auto conatct , its properties used S2S on all small, finite,continous ).also used param card ( use fllwer 1, hassaam yes,lgdisp 1) and global output request card ( uses disp,spcf,strain, stress).
used collector step inputs ( NLPARAM,NLOUT)
At last used collector step and choose non-linaer static condition and apply spc,load,NLPARM,NLOUT.
I USED LOAD 300 N ,250 N, 200 N, 100 N ETC
WE Observe the vonmises stress at simple, the stress and strain of 100 N is high from 200N,250N,300N,350N.
but sress is less for less force and high for high stress.
but in my model show 100N load stress is high from others load whose more than 100N .
TELL ME THE REASION ,if any mistake in this also tell me.
can you share your model? Are all different loads converging?
0 -
impauto said:
no other force applied ,only 350 n load apply on rbe2 . here we assume closed assembly already bolted ,we try to find out when we apply load 350 n on the c;lip ,the clip will rotate or not along the pipe. pipe and clip has contact only check for slide.
slide contact is frictionless contact. If you apply loads on that, you model will rotate, and no convergence will be achieved.
Unless there is some other stopper to avoid this free rotation.
0 -
-
please tell me reply for this problem how to solve it
0 -
Paul Sharp_21301 said:
can you share your model? Are all different loads converging?
ATTACHED MODEL
0 -
Adriano A. Koga_21884 said:
i assume you're running a NL implicit analysis in OptiStruct, right?
you can add details of your model in the message instead of the title.
But a few questions:
- are you using friction in your model?
Hii sir,
I have simulated on this clip and pipe.
I have done validate the model and meshing of 1 mm on this model. i have applied material and its properties to the model after that apply load collector ( spc,load as force1 for follwer load).
and used contact browser ( auto conatct , its properties used S2S on all small, finite,continous ).also used param card ( use fllwer 1, hassaam yes,lgdisp 1) and global output request card ( uses disp,spcf,strain, stress).
used collector step inputs ( NLPARAM,NLOUT)
At last used collector step and choose non-linaer static condition and apply spc,load,NLPARM,NLOUT.
I USED LOAD 300 N ,250 N, 200 N, 100 N ETC
WE Observe the vonmises stress at simple, the stress and strain of 100 N is high from 200N,250N,300N,350N.
but sress is less for less force and high for high stress.
but in my model show 100N load stress is high from others load whose more than 100N .
TELL ME THE REASION ,if any mistake in this also tell me.
0