Abnormal elements deletion.
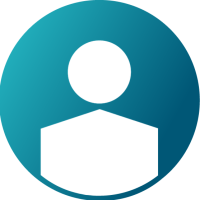
I am doing quasi static compression analysis. I am using matlaw36 with JC fail parameters d1,d2,d3 in my model. Simulation ran without any error but the element deletion is happening like the reference image and some elements are getting extended. What might be the possible reasons behind this.
Answers
-
Hi
Please let me know what Altair product are you using so that I can direct your question to the proper forum.
0 -
Payal Pawar_20288 said:
Hi
Please let me know what Altair product are you using so that I can direct your question to the proper forum.
Hi Payal
I am using Hypermesh 2021.2 and radioss solver.
regards
Akash
0 -
It is difficult to see exactly what is happening there. There are a number of potential reasons you may see instability in failure, the failure parameters themselves, material stress/strain curve, contacts (defined surf part/ext or part/all?) Timestep size, are units all as expected?. Can you share the model?, we could take a look.
0 -
Paul Sharp_21301 said:
It is difficult to see exactly what is happening there. There are a number of potential reasons you may see instability in failure, the failure parameters themselves, material stress/strain curve, contacts (defined surf part/ext or part/all?) Timestep size, are units all as expected?. Can you share the model?, we could take a look.
Dear Paul, Good day.
I am not able to attach the model because of file size.
Kindly provide other ways to upload the model.
regards
Akash
0 -
Hi, if the rad files will not zip down to required size, then you can upload to a file share and provide link, e.g. googledrive or similar.
If you would rather share with Altair directly, if you contact your local Altair Support, they can provide a file transfer link for you.
0 -
Paul Sharp_21301 said:
Hi, if the rad files will not zip down to required size, then you can upload to a file share and provide link, e.g. googledrive or similar.
If you would rather share with Altair directly, if you contact your local Altair Support, they can provide a file transfer link for you.
Dear Paul,
Here is the download link for setup file.
https://drive.google.com/drive/folders/1PShYAvskK-oLXgde_l_Pki3IZ2QoXoGp?usp=share_link
Kindly have a look.
regards
Akash
0 -
akasht said:
Dear Paul,
Here is the download link for setup file.
https://drive.google.com/drive/folders/1PShYAvskK-oLXgde_l_Pki3IZ2QoXoGp?usp=share_link
Kindly have a look.
regards
Akash
I think it is as a result of the /FAIL/JOHNSON criterion, for solid elements the triaxiality state can go substantially negative in compression and the failure strain increases exponentially in this region of the failure curve. leading you to have very squashed elements that do not fail
I substituted a /FAIL/BIQUAD failure with C1 set at 0.249 and all other (C2-5) set at 0.15, Biquad caps the extrapolation below C1 at some level (not exactly sure what!) but it gives a much cleaner failure characteristic for your model (Johnson on Left, Biquad on right)
I also made a couple of other changes:
For the plasticity curve for your material, I added a very small slope to the plastic behaviour so it is not 'perfectly plastic', not sure if necessary here, but I have seen having horizontal stress/strain curve can lead to instabilities in some models
I changed the definition of the self contact surface group to /SURF/PART/ALL (was /SURF/PART/EXT) this puts all surfaces of your elements in contact, with 'EXT' only the outer surfaces are in contact, so fractured surfaces would not be in contact, this makes a big difference for this model particularly in the area where the spoke fractures.
My model attached as 7zipped Radioss input decks
0 -
Paul Sharp_21301 said:
I think it is as a result of the /FAIL/JOHNSON criterion, for solid elements the triaxiality state can go substantially negative in compression and the failure strain increases exponentially in this region of the failure curve. leading you to have very squashed elements that do not fail
I substituted a /FAIL/BIQUAD failure with C1 set at 0.249 and all other (C2-5) set at 0.15, Biquad caps the extrapolation below C1 at some level (not exactly sure what!) but it gives a much cleaner failure characteristic for your model (Johnson on Left, Biquad on right)
I also made a couple of other changes:
For the plasticity curve for your material, I added a very small slope to the plastic behaviour so it is not 'perfectly plastic', not sure if necessary here, but I have seen having horizontal stress/strain curve can lead to instabilities in some models
I changed the definition of the self contact surface group to /SURF/PART/ALL (was /SURF/PART/EXT) this puts all surfaces of your elements in contact, with 'EXT' only the outer surfaces are in contact, so fractured surfaces would not be in contact, this makes a big difference for this model particularly in the area where the spoke fractures.
My model attached as 7zipped Radioss input decks
Dear Paul,
Thankyou for your support.
I ran with the model with your setup parameters. It ran without any error and element deletion is looking fine but in other hand the graph(force v/s stroke) seems many big dips. I am expecting somewhat smooth curve. Please see the attached image for your reference.
regards
Akash
0 -
akasht said:
Dear Paul,
Thankyou for your support.
I ran with the model with your setup parameters. It ran without any error and element deletion is looking fine but in other hand the graph(force v/s stroke) seems many big dips. I am expecting somewhat smooth curve. Please see the attached image for your reference.
regards
Akash
Is this from the model you sent before? Do the dips not correspond to when the spoke fractures occur? That would make sense I think? Sorry, I don't have the results of the run I did any more so I have nothing to compare to.
0 -
Paul Sharp_21301 said:
Is this from the model you sent before? Do the dips not correspond to when the spoke fractures occur? That would make sense I think? Sorry, I don't have the results of the run I did any more so I have nothing to compare to.
Ah... found 1 run, h3d only... looks different to what you got (higher loads, different displacements at the force reductions, so I guess different model?) the 1st big drop occurs around 30-35mm displacement and corresponds to when the 1st spoke fails... and second is at around 80mm when second spoke fails.. so I think it seems ok in this case
0 -
Paul Sharp_21301 said:
Ah... found 1 run, h3d only... looks different to what you got (higher loads, different displacements at the force reductions, so I guess different model?) the 1st big drop occurs around 30-35mm displacement and corresponds to when the 1st spoke fails... and second is at around 80mm when second spoke fails.. so I think it seems ok in this case
Dear Paul good morning.
Thanks for running the analysis.
The graph I attached is from other model(confidential model).
Your analysis graph looks ok.
I will research more on fail Biquad and optimize the c1-c5 parameters.
I will run the model I shared to you and let me cross check the graph against yours.
Thankyou for your kind support
Regards
Akash
0